Why Is Sugar Factory So Expensive
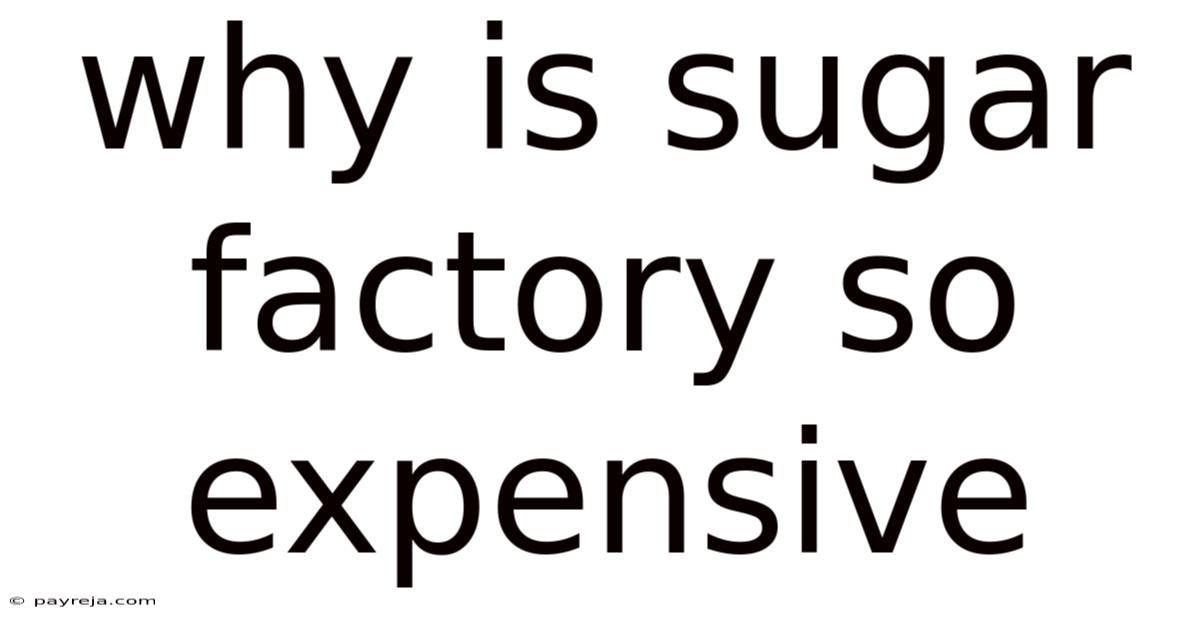
Discover more detailed and exciting information on our website. Click the link below to start your adventure: Visit Best Website meltwatermedia.ca. Don't miss out!
Table of Contents
The High Cost of Sweetness: Unpacking the Expensive Reality of Sugar Factories
Why are sugar factories so incredibly expensive to build and operate?
The sheer scale and complexity of modern sugar production contribute significantly to the high cost of establishing and maintaining a successful sugar factory.
Editor’s Note: This article on the high cost of sugar factories was published on October 26, 2023, and reflects the current state of the sugar industry’s infrastructure and operational costs.
Why Sugar Factories Are So Expensive: A Deep Dive
The seemingly simple act of transforming sugarcane or sugar beets into refined sugar belies an incredibly complex and capital-intensive process. The exorbitant cost of sugar factories stems from a confluence of factors, ranging from initial investment in advanced machinery and infrastructure to the ongoing expenses of skilled labor, energy consumption, and stringent regulatory compliance. This article will delve into the key drivers of this high cost, examining the economic realities and technological advancements that shape the modern sugar industry.
Overview of the Article:
This article provides a comprehensive analysis of the high cost of sugar factories. Readers will gain insights into the multifaceted nature of this cost, encompassing the initial capital investment, ongoing operational expenses, and the influence of global market dynamics. The discussion will explore the intricate interplay of technology, labor, regulatory frameworks, and environmental considerations that contribute to the overall expenditure. Ultimately, the article aims to offer a clear understanding of why building and operating a sugar factory represents a substantial financial undertaking.
The High Initial Investment:
The construction of a sugar factory requires a substantial upfront investment, often running into hundreds of millions of dollars. This significant capital expenditure is primarily attributed to:
-
Advanced Machinery and Equipment: Sugar processing involves a sophisticated series of steps, each requiring specialized equipment. This includes high-capacity harvesters for sugarcane, efficient extraction systems, evaporators, centrifuges, crystallizers, dryers, and sophisticated quality control instruments. The precision and robustness required for these machines contribute significantly to the overall cost. Many components are sourced from specialized manufacturers, further inflating the price.
-
Extensive Infrastructure: Sugar factories are not isolated units. They require extensive infrastructure, including:
- Raw Material Handling: Systems for transporting, storing, and pre-processing massive quantities of sugarcane or sugar beets. This can involve extensive rail networks, storage silos, and cleaning facilities.
- Processing Plant: A large-scale facility housing all the processing equipment, demanding robust construction to withstand the high temperatures, pressures, and corrosive substances involved in sugar production.
- Energy Generation: Sugar factories are energy-intensive, often requiring their own power generation facilities (e.g., cogeneration plants using bagasse, the fibrous residue from sugarcane) to meet their electricity demands.
- Waste Management: Effective waste management systems are crucial, involving wastewater treatment plants and methods for disposing of or utilizing byproducts.
-
Land Acquisition: Sugar factories require significant land areas, both for the processing plant and for storage and transportation infrastructure. Acquiring suitable land, particularly in prime agricultural regions, can be costly.
Ongoing Operational Costs:
Even after the initial investment, the ongoing operational costs of a sugar factory remain substantial. These expenses include:
-
Raw Material Costs: The cost of sugarcane or sugar beets constitutes a major variable expense. Fluctuations in agricultural yields, weather patterns, and global market prices directly impact profitability.
-
Energy Consumption: Sugar refining is an energy-intensive process, making energy costs a significant factor. While cogeneration plants can partially mitigate this, reliance on external energy sources increases operating expenses.
-
Labor Costs: Sugar factories require skilled labor, from agricultural workers to engineers and technicians. Wage costs vary depending on the location and prevailing labor regulations.
-
Maintenance and Repairs: The sophisticated machinery requires regular maintenance and periodic repairs, adding to the ongoing operational expenses.
-
Regulatory Compliance: Sugar factories are subject to stringent environmental regulations, requiring investment in pollution control measures and adherence to safety standards. Non-compliance can result in hefty fines.
Technological Advancements and Their Impact:
Technological advancements have played a significant role in shaping the economics of sugar production. While improving efficiency and yield, these advancements often come with high initial capital costs. Examples include:
-
Automation: Automation in harvesting, processing, and quality control reduces labor costs but requires substantial investment in robotic systems and sophisticated control systems.
-
Precision Agriculture: Utilizing data-driven techniques to optimize crop yields, water usage, and fertilizer application contributes to improved efficiency but demands investment in sensor technology and data analytics.
-
Improved Extraction Techniques: New technologies for extracting sugar from sugarcane or sugar beets enhance yield and reduce waste, although they come with higher initial equipment costs.
Global Market Dynamics and Price Volatility:
The sugar market is subject to significant price volatility influenced by factors such as global supply and demand, government policies (e.g., subsidies, tariffs), and weather patterns. These fluctuations impact the profitability of sugar factories, making the business inherently risky.
Environmental Considerations and Sustainability:
Increasing environmental awareness is driving stricter regulations and pushing for sustainable practices within the sugar industry. This translates into higher costs associated with:
-
Wastewater Treatment: Meeting stringent wastewater discharge standards requires substantial investment in advanced treatment technologies.
-
Greenhouse Gas Reduction: Reducing greenhouse gas emissions from sugar production is becoming increasingly important, requiring investment in cleaner energy sources and more efficient processes.
-
Sustainable Agriculture: Implementing sustainable agricultural practices, such as reducing pesticide use and promoting biodiversity, contributes to higher long-term costs but is essential for environmental responsibility.
Key Takeaways:
Factor | Impact on Cost |
---|---|
Initial Capital Investment | Extremely high due to machinery, infrastructure, and land acquisition. |
Operational Costs | Significant ongoing expenses for raw materials, energy, labor, maintenance, and compliance. |
Technology | Advancements increase efficiency but require high upfront investments. |
Market Volatility | Global market dynamics and price fluctuations impact profitability. |
Environmental Regulations | Stricter rules necessitate investments in sustainable practices. |
The Interplay of Point and Sugar Factory Costs
Let's explore the connection between energy consumption ("point") and the high cost of sugar factories.
Roles and Real-World Examples:
Energy is a crucial input in sugar production. Every stage, from harvesting to refining, consumes significant energy. For example, the evaporation process, where water is removed from sugar juice, requires massive amounts of heat. Many factories rely on bagasse-fired boilers, but others use natural gas or electricity, which are more expensive. The cost of energy directly affects the operating expenses of the factory.
Risks and Mitigations:
Fluctuating energy prices pose a substantial risk. Factories can mitigate this risk through:
- Diversification of energy sources: Combining bagasse-based cogeneration with alternative sources like solar or wind power reduces reliance on volatile markets.
- Energy efficiency improvements: Implementing energy-efficient technologies and optimizing processes minimizes energy consumption.
Impact and Implications:
High energy costs increase the overall production cost, impacting the final price of sugar. This makes sugar producers more vulnerable to market fluctuations and reduces their competitiveness.
Reinforcing the Connection in the Conclusion:
The high cost of energy is inextricably linked to the high cost of running a sugar factory. Strategies to mitigate energy costs, such as investing in renewable energy sources and improving energy efficiency, are not just environmentally beneficial but also crucial for financial sustainability.
Deeper Dive into Energy Consumption:
Energy consumption in sugar factories follows a predictable pattern:
-
Harvesting and Transportation: Fuel is used for harvesting machinery and transportation of sugarcane or beets to the factory.
-
Processing: Energy is crucial for crushing, extraction, clarification, evaporation, crystallization, and drying stages.
-
Auxiliary Operations: Energy is needed for pumping, lighting, and running various equipment.
-
Wastewater Treatment: Energy is used in pumping, aeration, and other treatment processes.
FAQ:
-
Q: Why are some sugar factories more expensive than others? A: Costs vary based on size, technology, location (land prices, labor costs), and the level of automation implemented.
-
Q: Can sugar production be made more sustainable? A: Yes, through renewable energy sources, wastewater recycling, and adopting sustainable agricultural practices.
-
Q: How do government policies affect sugar factory costs? A: Subsidies can reduce costs, while tariffs and environmental regulations can increase them.
-
Q: What is the role of technology in reducing sugar factory costs? A: Automation and improved extraction techniques can boost efficiency, potentially offsetting some costs.
-
Q: What are the main risks involved in building a sugar factory? A: High upfront capital investment, fluctuating raw material prices, energy price volatility, and market competition.
-
Q: What is the future of the sugar industry? A: Sustainability, technological advancements, and efficient resource management will be key for future success.
Actionable Tips:
-
Invest in energy-efficient technologies: Prioritize equipment and processes that minimize energy consumption.
-
Explore renewable energy options: Integrate solar, wind, or biomass energy into your operations.
-
Optimize raw material sourcing: Secure stable and cost-effective supplies of sugarcane or sugar beets.
-
Implement robust maintenance programs: Minimize downtime and reduce repair costs through proactive maintenance.
-
Embrace automation: Automate processes where feasible to reduce labor costs and improve efficiency.
-
Focus on sustainable practices: Reduce waste, minimize environmental impact, and comply with all regulations.
Conclusion:
The high cost of sugar factories is a complex issue shaped by substantial capital investment, continuous operational expenses, and external factors like market dynamics and environmental regulations. While the initial investment and ongoing operational costs are significant, strategic planning, technological advancements, and a focus on sustainability are crucial for success in this challenging but essential industry. Understanding these factors is vital for stakeholders, from investors to consumers, to appreciate the multifaceted journey from sugarcane field to the refined sugar on our tables.
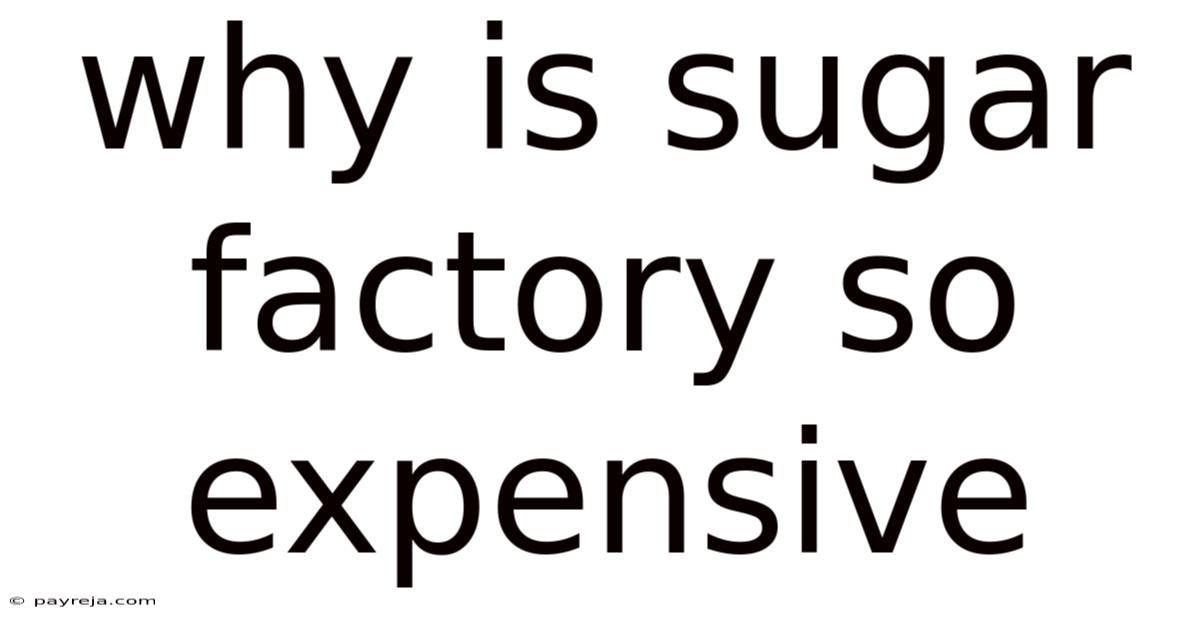
Thank you for visiting our website wich cover about Why Is Sugar Factory So Expensive. We hope the information provided has been useful to you. Feel free to contact us if you have any questions or need further assistance. See you next time and dont miss to bookmark.
Also read the following articles
Article Title | Date |
---|---|
What Is Cloud Based Crm Software | Mar 16, 2025 |
What Does A Crm Director Do | Mar 16, 2025 |
Self Hosted Crm Github | Mar 16, 2025 |
Lightspeed Evo Crm | Mar 16, 2025 |
Zoho Crm Tax Rates | Mar 16, 2025 |