What Is Pegging In Sap
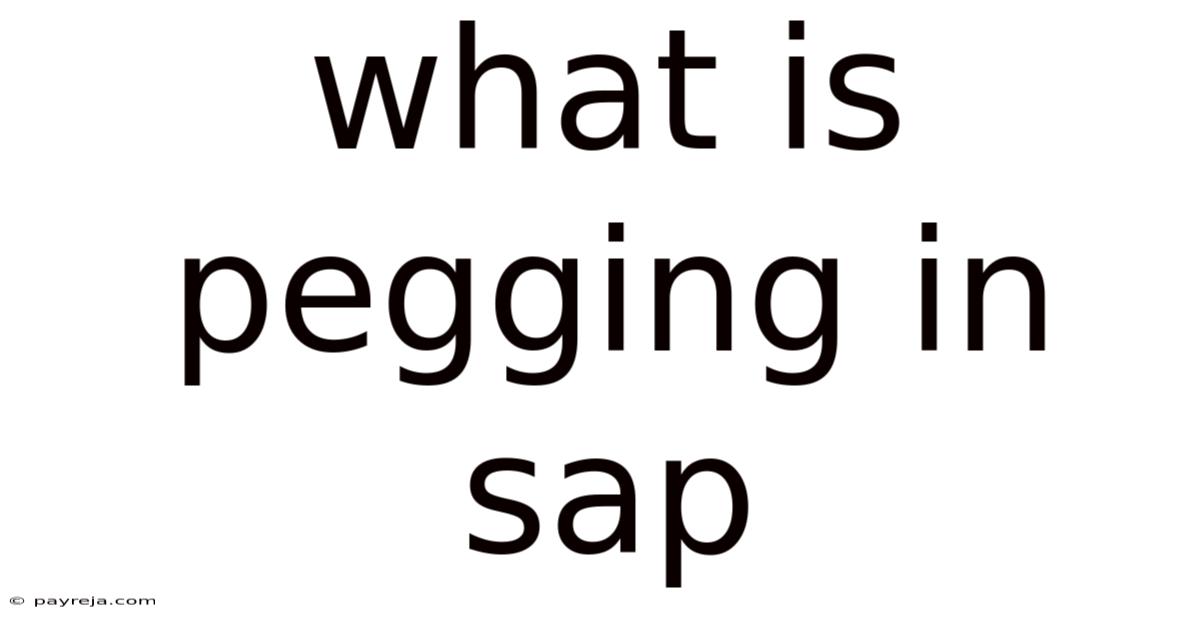
Discover more detailed and exciting information on our website. Click the link below to start your adventure: Visit Best Website meltwatermedia.ca. Don't miss out!
Table of Contents
Unlocking the Power of Pegging in SAP: A Comprehensive Guide
What if mastering pegging in SAP could significantly streamline your procurement and production processes? This powerful functionality offers unparalleled visibility and control, transforming how businesses manage materials and resources.
Editor’s Note: This article on pegging in SAP has been updated today to reflect the latest best practices and functionalities within the SAP ecosystem.
Why Pegging Matters in SAP
Pegging in SAP is a crucial functionality within the Materials Management (MM) and Production Planning (PP) modules. It establishes a direct link between a material requirement (demand) and its source (supply). This link provides complete transparency into the origin of materials used in production orders, sales orders, or project requirements. Understanding and effectively utilizing pegging offers numerous benefits, including improved inventory management, enhanced production planning, reduced material shortages, and optimized procurement processes. This directly impacts profitability by minimizing waste, improving on-time delivery, and enhancing overall supply chain efficiency. Industries ranging from manufacturing and automotive to pharmaceuticals and retail rely heavily on accurate pegging to maintain operational excellence. The ability to trace materials back to their source is also increasingly vital for compliance and traceability requirements in many sectors.
Overview of this Article
This article provides a comprehensive overview of pegging in SAP, exploring its various aspects and applications. Readers will gain a thorough understanding of what pegging is, its different types, how it works within various SAP modules, best practices for implementation and utilization, and troubleshooting common issues. The article also analyzes the relationship between pegging and other crucial SAP functionalities, including Material Requirements Planning (MRP), and provides actionable tips for maximizing the benefits of pegging.
Pegging in SAP: A Detailed Exploration
Pegging in SAP primarily functions within the context of Material Requirements Planning (MRP). MRP is a sophisticated system for planning material requirements based on anticipated production and sales demands. Pegging enhances the MRP process by providing a clear and traceable link between each material requirement and its assigned source. This means that for every material needed, the system shows exactly which production order, purchase order, or stock transfer provides that material. Without pegging, this traceability is absent, making it challenging to manage inventory, analyze material flows, and identify bottlenecks.
There are several types of pegging, each serving a specific purpose:
-
Production Order Pegging: This links a material requirement in a production order to a specific source, such as a purchase order or stock. This is crucial for tracking the materials consumed in a particular production run.
-
Sales Order Pegging: This links a material requirement originating from a sales order to the source supplying that material. This is vital for ensuring that sales orders can be fulfilled on time.
-
Purchase Order Pegging: This connects a material requirement to a specific purchase order raised to procure the required material. This is essential for managing supplier relationships and tracking material deliveries.
-
Stock Pegging: This indicates that the material requirement is met from existing stock on hand. This is helpful for optimizing inventory utilization.
The pegging process typically involves several steps:
-
Demand Creation: The system generates a requirement for a material based on production orders, sales orders, or other planned demands.
-
Source Determination: The system identifies the potential sources that can fulfill this material requirement (e.g., existing stock, purchase orders, production orders).
-
Pegging Assignment: The system assigns the requirement to a specific source, establishing the pegging relationship.
-
Tracking and Monitoring: The system tracks the status of the pegging relationship, updating it as materials are consumed or delivered.
Pegging and Material Requirements Planning (MRP)
Pegging significantly enhances the effectiveness of MRP. By providing a clear view of the material flow, it allows planners to:
-
Identify potential shortages: Early detection of potential shortages allows for proactive procurement or production scheduling adjustments.
-
Optimize inventory levels: A clear understanding of material usage allows for more accurate inventory forecasting and planning.
-
Improve production scheduling: Pegging enables better planning of production schedules, minimizing delays and maximizing throughput.
-
Enhance supply chain visibility: A comprehensive view of the entire material flow provides greater transparency across the entire supply chain.
Pegging in Different SAP Modules
While pegging’s core functionality resides within MM and PP, its effects ripple across other modules. For example:
-
SD (Sales and Distribution): Pegging helps ensure that sales orders are fulfilled on time and accurately reflects available inventory.
-
QM (Quality Management): Pegging facilitates the tracing of materials throughout the quality control process.
-
PS (Project System): In project management, pegging ensures that materials are available for project execution.
Best Practices for Implementing and Utilizing Pegging
-
Accurate Master Data: Maintaining accurate and up-to-date master data for materials, vendors, and production resources is paramount for effective pegging.
-
Regular MRP Runs: Performing regular MRP runs ensures that pegging relationships are continuously updated and accurate.
-
Proper Configuration: Correctly configuring the pegging parameters in the system is crucial for optimal performance.
-
Monitoring and Analysis: Regularly monitoring the pegging relationships allows for proactive identification and resolution of any discrepancies or issues.
-
Training and User Adoption: Adequate training for users is essential to ensure that the pegging functionality is correctly understood and used.
Case Study: Optimizing Production with Pegging in a Manufacturing Setting
A large automotive manufacturer implemented robust pegging in their SAP system. This allowed them to accurately track the origin of components used in vehicle assembly. By analyzing pegging data, they identified a bottleneck in the supply of a specific component. This led to proactive negotiations with their supplier, resulting in faster delivery times and a significant reduction in production delays.
Key Takeaways: Understanding Pegging’s Value in SAP
Key Aspect | Description | Benefit |
---|---|---|
Demand Visibility | Clear linkage between material requirements and their source. | Improved planning and resource allocation. |
Supply Chain Tracing | Ability to trace materials from source to finished product. | Enhanced control and compliance. |
Inventory Optimization | Enables accurate inventory forecasting and reduced holding costs. | Minimized waste and optimized storage. |
Production Scheduling | Supports accurate production scheduling, minimizing delays. | Improved on-time delivery and reduced production bottlenecks. |
Problem Prevention | Early identification of potential material shortages. | Proactive mitigation of supply chain disruptions. |
Reporting & Analysis | Provides detailed reports on material flow and usage patterns. | Data-driven insights for improved decision-making and process optimization. |
Exploring the Connection Between MRP and Pegging
MRP and pegging are intrinsically linked. MRP determines the material requirements, while pegging provides the traceability to the specific sources fulfilling those requirements. Without pegging, MRP's output remains incomplete; it identifies what is needed but not where it comes from. This relationship is crucial for efficient resource allocation, proactive problem-solving, and informed decision-making.
Roles and Real-World Examples:
- Production Planners: Use pegging data to optimize production schedules and prevent delays.
- Procurement Managers: Leverage pegging to track material deliveries and manage supplier relationships.
- Inventory Managers: Use pegging information to optimize inventory levels and reduce storage costs.
Risks and Mitigations:
- Inaccurate Master Data: Regular data cleansing and validation are crucial to mitigate this risk.
- Insufficient Training: Comprehensive training for all users ensures proper utilization of the system.
- System Complexity: Effective implementation requires careful planning and configuration.
Impact and Implications:
- Improved On-Time Delivery: Accurate pegging leads to fewer production delays and improved customer satisfaction.
- Reduced Inventory Costs: Optimized inventory management results in lower storage and holding costs.
- Enhanced Supply Chain Visibility: Improved traceability facilitates better decision-making and risk management.
Diving Deeper into MRP’s Influence on Pegging
MRP's output directly drives the pegging process. The material requirements generated by MRP become the "demand" side of the pegging relationship. The accuracy of MRP calculations significantly impacts the effectiveness of pegging. Inaccurate MRP data leads to inaccurate pegging, resulting in potential material shortages or overstocking. Therefore, optimizing MRP settings and data is critical for achieving optimal pegging functionality.
Frequently Asked Questions (FAQ)
Q1: What is the difference between pegging and tracing?
A1: While related, pegging and tracing are distinct. Pegging links a requirement to a source, while tracing follows the entire material flow history. Tracing offers broader, more detailed information than pegging.
Q2: Can I customize pegging in SAP?
A2: Yes, SAP allows for customization of pegging through configuration settings. This allows adaptation to specific business needs and processes.
Q3: How do I resolve pegging discrepancies?
A3: Discrepancies often arise from inaccurate master data. Reviewing and correcting master data, running MRP again, and checking for inconsistencies in the source documents are typical troubleshooting steps.
Q4: Is pegging mandatory in SAP?
A4: No, pegging is not mandatory but is highly recommended for optimizing material management and production planning.
Q5: What reports can I use to analyze pegging data?
A5: Several standard and custom reports are available to analyze pegging data, providing valuable insights into material flow and usage patterns.
Q6: How often should I review my pegging data?
A6: Regular review frequency depends on your business needs. However, at a minimum, a monthly review is recommended to identify and address any potential issues.
Actionable Tips on Optimizing Pegging in SAP
- Regularly cleanse and validate master data: Ensure accuracy of material, vendor, and production resource data.
- Perform regular MRP runs: Keep pegging relationships up-to-date and accurate.
- Analyze pegging reports: Identify bottlenecks and areas for improvement in your supply chain.
- Train users on pegging functionality: Ensure all relevant personnel understand and utilize this feature effectively.
- Implement a robust change management process: Control modifications to pegging configurations and data to avoid errors.
- Use alerts and notifications: Set up system alerts to notify of potential material shortages or discrepancies.
- Integrate pegging with other modules: Leverage pegging data across different SAP modules for a holistic view.
Conclusion
Pegging in SAP is a powerful tool that significantly enhances material management and production planning. By establishing a direct link between demand and supply, pegging provides unparalleled visibility into material flows, leading to improved inventory management, optimized production scheduling, and enhanced supply chain efficiency. Mastering pegging requires a combination of accurate master data, regular MRP runs, appropriate system configuration, and user training. By implementing the best practices outlined in this article, businesses can unlock the full potential of pegging and transform their operational efficiency. The ability to accurately track materials from origin to finished product is not only beneficial for cost savings and on-time delivery but also increasingly crucial in meeting compliance requirements and building a more resilient and robust supply chain. Understanding and effectively leveraging pegging is an investment that yields significant long-term returns.
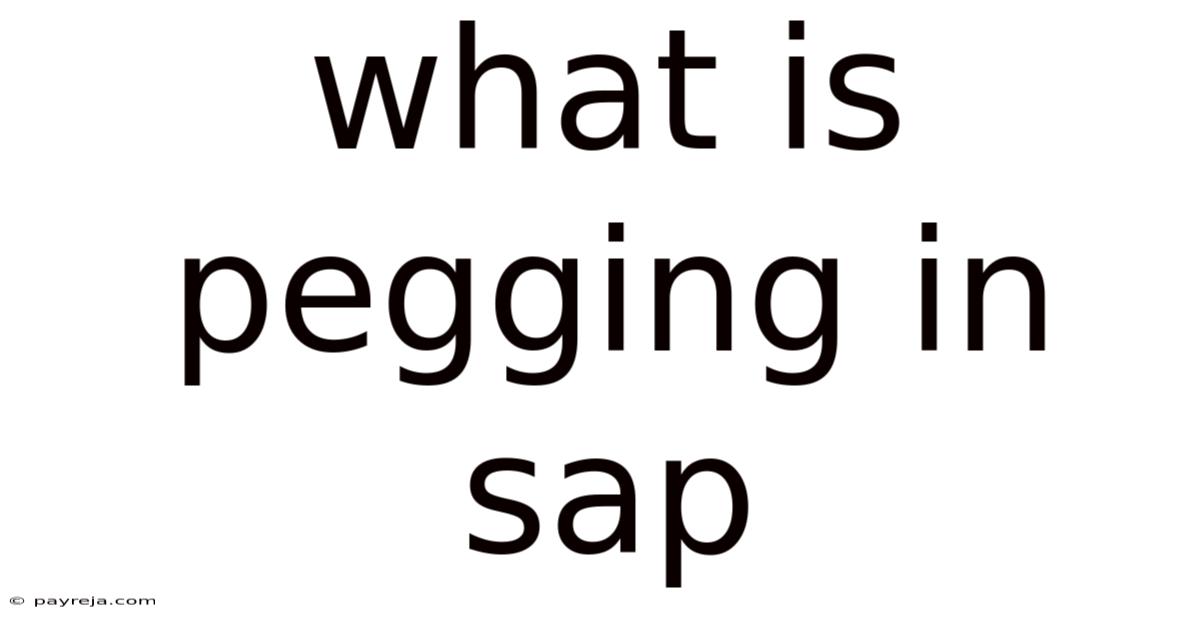
Thank you for visiting our website wich cover about What Is Pegging In Sap. We hope the information provided has been useful to you. Feel free to contact us if you have any questions or need further assistance. See you next time and dont miss to bookmark.
Also read the following articles
Article Title | Date |
---|---|
Does Sap Freeze | Apr 19, 2025 |
Who Hires Sap Drivers | Apr 19, 2025 |
When Does Tree Sap Stop Falling | Apr 19, 2025 |
Who Killed El Sapo Dexter | Apr 19, 2025 |
Does Goo Gone Remove Tree Sap | Apr 19, 2025 |