What Is Braze
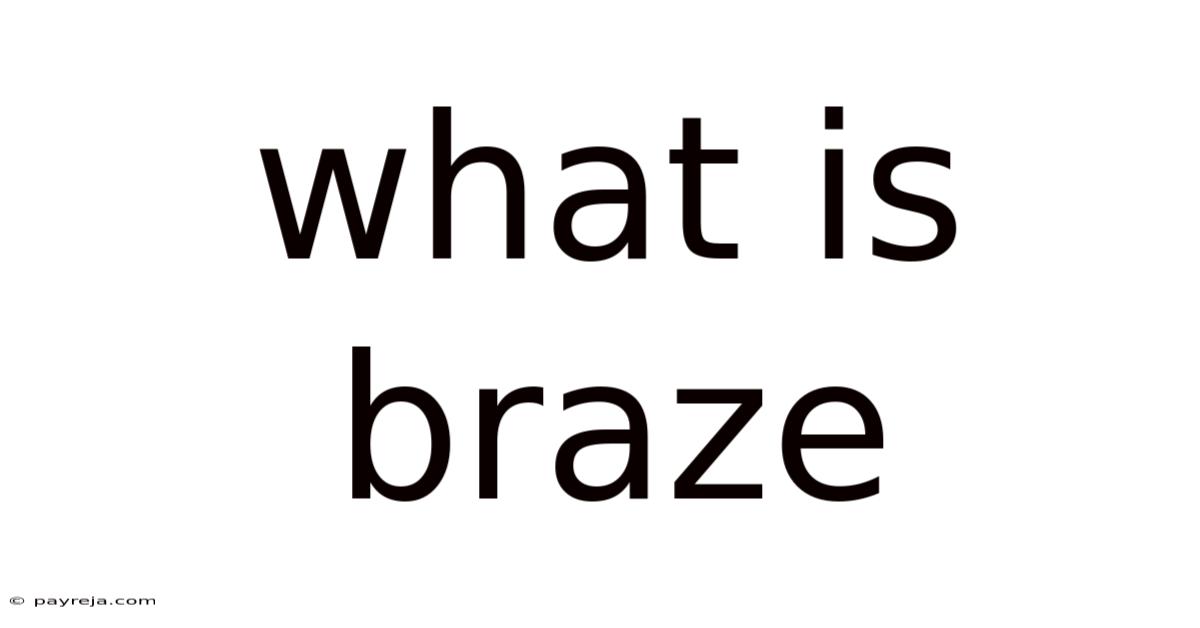
Discover more detailed and exciting information on our website. Click the link below to start your adventure: Visit Best Website meltwatermedia.ca. Don't miss out!
Table of Contents
Unlocking the Secrets of Brazing: A Deep Dive into Joining Techniques
What if mastering the art of brazing could revolutionize your manufacturing process? This versatile joining technique is transforming industries and offering unprecedented possibilities.
Editor’s Note: This article on brazing has been published today, providing you with the latest insights and information on this crucial joining technology.
Why Brazing Matters
Brazing, a metal-joining process, is far more than a niche technique; it’s a foundational element in countless industries. From aerospace components requiring extreme durability to intricate jewelry demanding exquisite detail, brazing's versatility is undeniable. Understanding its nuances offers businesses the potential to optimize production, enhance product quality, and unlock innovative design possibilities. The application of brazing extends to diverse sectors, including automotive, electronics, HVAC, and medical device manufacturing, highlighting its significant impact on modern manufacturing. The economic implications are considerable; efficient brazing translates to reduced manufacturing costs, improved product lifespan, and a competitive edge in the marketplace. Furthermore, the environmental benefits associated with the efficient use of materials and reduced waste underscore the importance of brazing as a sustainable joining method.
This article will cover the fundamental principles of brazing, explore different brazing techniques, analyze various filler metals and their applications, and discuss the critical factors influencing brazing success. Readers will gain a comprehensive understanding of brazing's capabilities, enabling them to assess its suitability for their specific applications. The value lies in acquiring actionable knowledge to improve processes, select appropriate materials, and troubleshoot potential problems.
A Comprehensive Overview of Brazing
Brazing is a joining process that uses a filler metal with a lower melting point than the base metals being joined. The filler metal flows into the joint by capillary action, creating a strong, reliable bond. Unlike welding, brazing doesn't melt the base metals. This distinction is crucial, as it preserves the base metal's properties, preventing weakening or distortion often associated with welding. The process relies on the precise control of temperature and the careful selection of filler metal to achieve optimal joint strength and quality.
This article will delve into the key aspects of brazing, including:
- The Brazing Process: A step-by-step explanation of the procedure.
- Filler Metals: Exploring different types and their applications.
- Brazing Techniques: Examining various methods like furnace brazing, torch brazing, and dip brazing.
- Joint Design: Understanding the crucial role of proper joint design for successful brazing.
- Quality Control: Methods for ensuring consistent, high-quality brazed joints.
- Applications Across Industries: Illustrative examples showcasing brazing's diverse uses.
Research and Data-Driven Insights: The Science of Brazing
The effectiveness of brazing hinges on several key scientific principles. Capillary action, the driving force behind filler metal flow, is governed by surface tension and the wetting behavior of the filler metal on the base metals. The selection of filler metal is critical; it must possess a lower melting point than the base metals and achieve proper wetting and adhesion. Metallurgical considerations, including the compatibility of the base and filler metals, are paramount. Research from institutions like the American Welding Society (AWS) provides extensive data on filler metal properties, brazing temperatures, and joint strength. Studies on the influence of various parameters (such as temperature, time, and pressure) on joint quality highlight the precision required for optimal results. Furthermore, advancements in brazing technology are constantly being developed, focusing on improved efficiency, reduced environmental impact, and enhanced joint strength.
Key Insights at a Glance: Essential Takeaways
Insight | Description |
---|---|
Capillary Action is Key | Filler metal flow depends on surface tension and wetting properties. |
Filler Metal Selection is Crucial | The right filler metal ensures proper melting, wetting, and adhesion. |
Joint Design Impacts Strength | Proper joint design maximizes capillary action and ensures a strong, reliable bond. |
Temperature Control is Essential | Precise temperature control is vital for optimal filler metal flow and prevents base metal damage. |
Cleaning is Paramount | Thorough cleaning of base metals removes oxides and ensures proper wetting. |
Quality Control is Mandatory | Consistent quality requires meticulous monitoring of process parameters and regular inspection of brazed joints. |
Delving into the Core: Understanding the Brazing Process
The brazing process typically involves several key steps:
-
Preparation: This includes cleaning the base metals to remove oxides and other contaminants that can hinder proper wetting. Various cleaning methods, including chemical cleaning, mechanical cleaning (such as grinding or brushing), and ultrasonic cleaning, might be employed depending on the base metals and the level of contamination.
-
Flux Application: A flux is applied to the joint surfaces to prevent oxidation during heating. The flux lowers the surface tension of the filler metal, improving wetting and flow. Different fluxes are used depending on the base and filler metals.
-
Heating: The assembly is heated to a temperature above the filler metal's melting point but below the melting point of the base metals. Heating methods vary; common approaches include torch brazing, furnace brazing, induction brazing, and resistance brazing.
-
Filler Metal Application: The filler metal, either in wire or pre-placed form, is introduced into the joint. Capillary action draws the molten filler metal into the joint, filling the gap between the base metals.
-
Cooling: The assembly is allowed to cool slowly to solidify the filler metal and ensure a strong, reliable joint.
Exploring Brazing Techniques: A Variety of Approaches
Several techniques exist for performing brazing, each suited to specific applications and production scales:
-
Torch Brazing: A versatile technique using a torch to heat the assembly locally. It's suitable for smaller parts and allows precise control over the heating process.
-
Furnace Brazing: Ideal for high-volume production, furnace brazing heats entire batches of components simultaneously in a controlled atmosphere furnace.
-
Dip Brazing: Parts are dipped into a molten bath of filler metal. This method is efficient for mass production of small, similar parts.
-
Induction Brazing: An efficient technique using electromagnetic induction to heat the assembly. It offers precise heating and is well-suited for automation.
-
Resistance Brazing: Electrical resistance is used to heat the joint, providing good control and repeatability.
The Interplay Between Filler Metals and Brazing Success
The choice of filler metal significantly impacts the brazing process. Different filler metals offer varying melting points, strengths, and corrosion resistance. Common filler metals include silver alloys, copper alloys, nickel alloys, and aluminum alloys. The selection is based on the base metals being joined, the desired joint properties, and the brazing environment. The chemical compatibility between the filler metal and the base metals is critical to ensure proper wetting and joint strength. Choosing an inappropriate filler metal can lead to weak joints, poor wetting, or even failure.
The Crucial Role of Joint Design in Brazing
Proper joint design is essential for successful brazing. The design must facilitate capillary action, ensuring complete filling of the joint gap. Common joint designs include butt joints, lap joints, and corner joints. The gap between the base metals should be carefully controlled; too large a gap can prevent complete filling, while too small a gap can hinder capillary action. The design must also consider the thermal expansion and contraction of the base and filler metals to prevent stress cracking during cooling.
Quality Control and Ensuring Consistent Results
Quality control is paramount in brazing to maintain consistent joint quality and reliability. This includes:
-
Regular inspection of brazed joints: Visual inspection, radiographic inspection, and other non-destructive testing methods are used to detect flaws.
-
Process monitoring: Temperature, time, and pressure are carefully monitored to ensure consistent brazing parameters.
-
Material testing: Regular testing of filler metals and base materials ensures that they meet the required specifications.
Brazing's Impact Across Industries: Real-World Applications
Brazing finds extensive application across numerous industries:
-
Aerospace: Brazing is used to join high-strength, lightweight alloys in aircraft and spacecraft components.
-
Automotive: Brazing is used in radiators, heat exchangers, and other components requiring high thermal conductivity.
-
Electronics: Brazing joins components in electronic devices, offering high electrical conductivity and reliability.
-
Medical Devices: Brazing's biocompatibility and precision make it ideal for medical implants and instruments.
-
Jewelry: The precision and aesthetic quality of brazing make it suitable for intricate jewelry designs.
The Connection Between Flux and Successful Brazing
Flux plays a vital role in successful brazing. It acts as a cleaning agent, removing oxides and other contaminants from the surface of the base metals, allowing for better wetting and bonding with the filler metal. Without flux, the molten filler metal would not flow smoothly into the joint, resulting in a weak or incomplete bond. Different fluxes are formulated for various metal combinations to ensure compatibility and optimal performance. The selection of the correct flux is crucial for ensuring a successful braze. Incorrect flux can lead to poor wetting, porosity in the braze joint, and overall failure.
Roles and Real-World Examples: Flux in Action
The role of flux is demonstrated in various industries. In the electronics industry, for example, the use of a specialized flux is critical for brazing delicate components onto circuit boards, preventing damage and ensuring proper electrical conductivity. In automotive applications, flux is essential for brazing heat exchangers and radiators, where high thermal conductivity is critical. Improper flux selection can lead to leaks and performance issues in these components.
Risks and Mitigations: Flux Related Challenges
While flux is essential, its improper use can lead to issues. Residual flux can cause corrosion, impacting the long-term durability of the brazed joint. Therefore, thorough cleaning after brazing is crucial to remove any remaining flux. Incorrect flux selection can also lead to poor wetting or even damage to the base metals. Careful consideration of the base metals and filler metal is needed when selecting the appropriate flux.
Impact and Implications: The Long-Term Effects of Flux Choice
The correct flux choice impacts the long-term performance and reliability of the brazed joint. A properly selected and applied flux ensures a strong, corrosion-resistant joint with optimal performance. Conversely, improper flux selection or application can lead to premature failure due to corrosion, leaks, or weakening of the joint. The long-term implications of flux choice are significant, impacting product life, safety, and overall cost-effectiveness.
Deeper Dive into Flux: A Detailed Examination
Flux is typically a mixture of inorganic salts designed to lower the surface tension of molten metals, thus improving their wetting ability. Different fluxes are designed for different metal combinations and brazing temperatures. The chemical composition of the flux is carefully chosen to react with oxides on the base metal surfaces, creating a clean surface for the filler metal to adhere to. The selection of the flux is crucial, as incompatible fluxes can react with the base metals, causing damage or inhibiting proper wetting. Advanced fluxes are now being developed to minimize environmental impact and improve efficiency.
Frequently Asked Questions about Brazing
Q1: What is the difference between brazing and soldering?
A1: Brazing uses filler metals with higher melting points (typically above 450°C or 842°F) than soldering, resulting in stronger joints. Soldering uses lower melting point fillers.
Q2: Can I braze any two metals together?
A2: No, the compatibility of base and filler metals is crucial. Some metal combinations may not braze well due to poor wetting or chemical incompatibility.
Q3: How important is cleanliness in brazing?
A3: Cleanliness is paramount. Oxides and contaminants prevent proper wetting and lead to weak joints.
Q4: What type of equipment is needed for brazing?
A4: Equipment depends on the technique (torch, furnace, etc.). This can include torches, furnaces, induction heaters, jigs, and safety equipment.
Q5: How can I ensure a strong brazed joint?
A5: Proper joint design, correct filler metal selection, precise temperature control, and thorough cleaning are essential.
Q6: What are the common problems encountered in brazing?
A6: Common problems include incomplete filling, porosity, cracking, and improper wetting. These often stem from poor preparation, incorrect filler metal, or improper temperature control.
Actionable Tips for Successful Brazing
- Thoroughly clean base metals: Remove all oxides and contaminants.
- Select the appropriate filler metal: Ensure compatibility with base metals.
- Use the correct flux: This prevents oxidation and promotes wetting.
- Control temperature precisely: Avoid overheating or underheating.
- Properly design the joint: Optimize for capillary action.
- Inspect the joint: Verify complete filling and absence of defects.
- Use appropriate safety precautions: Brazing involves high temperatures and potentially hazardous materials.
Conclusion: The Enduring Power of Brazing
Brazing remains a vital joining technique across diverse industries, offering strength, precision, and versatility. Understanding its intricacies – from the role of capillary action to the importance of proper joint design and flux selection – is crucial for optimizing manufacturing processes and achieving superior results. As technological advancements continue, brazing’s importance in modern manufacturing will only continue to grow, shaping innovative designs and driving efficiency in various sectors. The exploration of this versatile joining technique offers a path to improved manufacturing practices and a competitive edge in today's dynamic industrial landscape. The detailed insights shared here empower readers to harness the potential of brazing for enhanced product quality, reduced costs, and sustainable manufacturing practices.
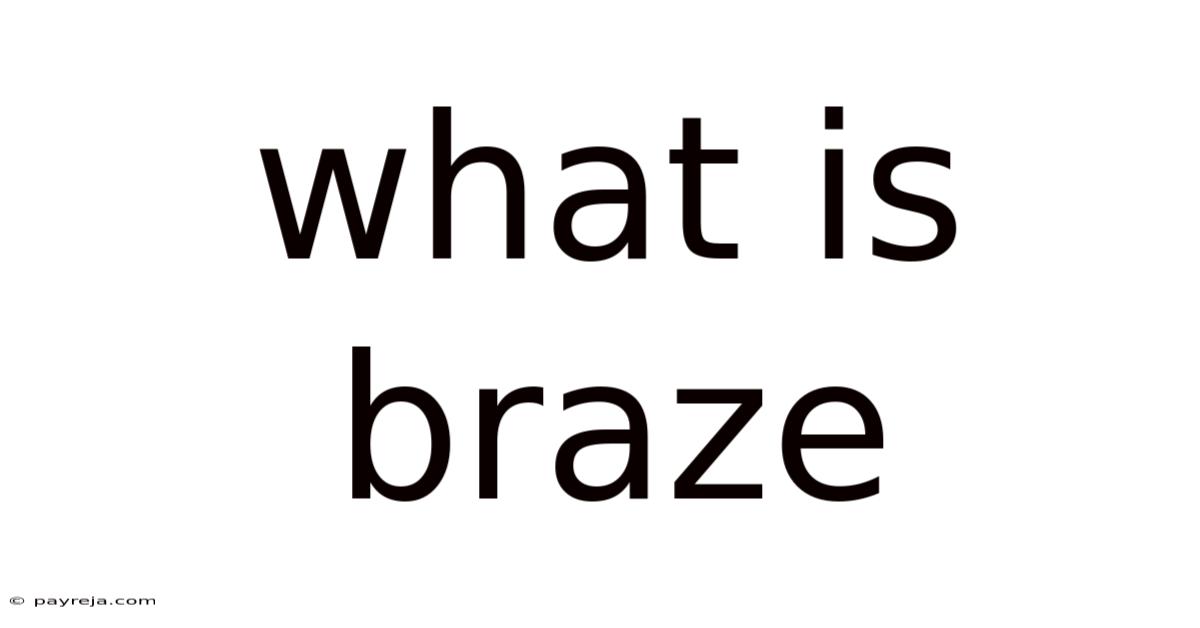
Thank you for visiting our website wich cover about What Is Braze. We hope the information provided has been useful to you. Feel free to contact us if you have any questions or need further assistance. See you next time and dont miss to bookmark.
Also read the following articles
Article Title | Date |
---|---|
What Are The Stages Of Crm | Apr 20, 2025 |
What Is Braze Software | Apr 20, 2025 |
What Are Some Crm Databases | Apr 20, 2025 |
A Crm System Includes All Of The Following Activities Except Quizlet | Apr 20, 2025 |
How To Create Crm Trial Instance | Apr 20, 2025 |