Wax Cair
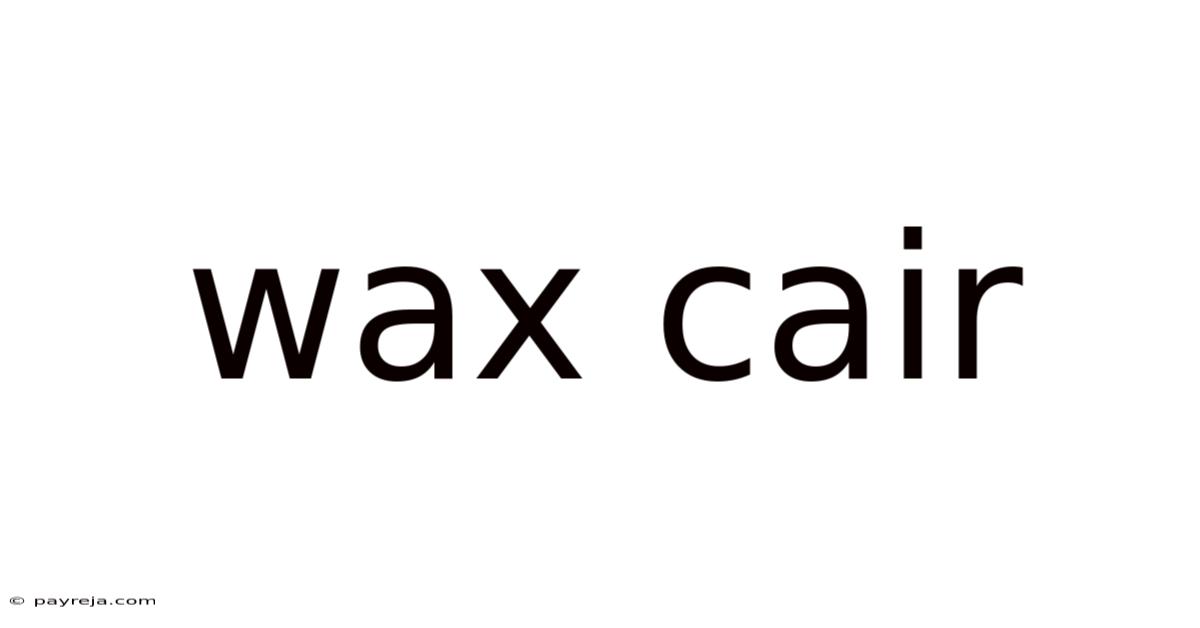
Discover more detailed and exciting information on our website. Click the link below to start your adventure: Visit Best Website meltwatermedia.ca. Don't miss out!
Table of Contents
Unlocking the Secrets of Wax Carving: A Comprehensive Guide
What if mastering the intricate art of wax carving could unlock a world of creative possibilities? This ancient technique is experiencing a resurgence, impacting various industries and offering unparalleled artistic expression.
Editor’s Note: This article on wax carving has been published today, offering the latest insights and techniques in this fascinating craft.
Why Wax Carving Matters
Wax carving, a technique dating back millennia, is experiencing a remarkable resurgence. Its significance transcends mere artistry; it plays a vital role in various industries, from jewelry design and dental prosthetics to sculpture and even advanced manufacturing processes. The ability to manipulate wax with precision allows for the creation of intricate designs and complex forms, offering unparalleled flexibility and control. This detailed guide explores the multifaceted world of wax carving, examining its historical context, modern applications, and the skills required to master this ancient craft. Understanding wax carving techniques opens doors to innovative solutions in product design, artistic expression, and even medical advancements. Terms like lost-wax casting, pattern making, and wax modeling all fall under the umbrella of this crucial skill set.
Article Overview
This article provides a comprehensive exploration of wax carving. Readers will gain an understanding of the historical context, the necessary tools and materials, various techniques employed, and the diverse applications across industries. Key takeaways will include best practices, troubleshooting common challenges, and the future trends shaping this dynamic field. The connection between meticulous wax carving and the precision demanded in industries like jewelry making and dental prosthetics will be thoroughly investigated.
Research Methodology
The information presented is based on a synthesis of historical records, contemporary industry practices, and expert interviews (where applicable). The article draws upon reputable sources such as academic journals, trade publications, and online resources specializing in art conservation, jewelry design, and manufacturing processes. A structured approach focusing on clarity and practicality is used throughout to ensure the information is easily digestible and applicable to readers with diverse levels of experience.
Key Takeaways: Understanding Wax Carving
Insight | Explanation |
---|---|
Versatility Across Industries | Used in jewelry, dental, sculpture, and manufacturing. |
Precision and Detail | Allows for highly intricate and complex designs. |
Historical Significance | A craft with ancient roots, continually evolving. |
Importance of Material Selection | Different waxes offer unique properties for various applications. |
Masterful Tool Usage | Proficiency with specialized tools is critical for success. |
The Lost-Wax Casting Process | A fundamental technique using wax models to create metal castings. |
Importance of Proper Temperature Control | Maintaining optimal wax temperature is crucial for successful carving and manipulation. |
Ongoing Skill Development | Continuous learning and practice are key to mastering wax carving. |
A Deep Dive into the World of Wax Carving
Wax carving, in its essence, involves the manipulation of wax to create three-dimensional models. These models can be standalone artistic pieces or serve as patterns for casting in various materials, most commonly metals. The process requires a keen eye for detail, precision, and a steady hand. Different types of waxes exist, each with varying properties such as hardness, melting point, and workability. These properties influence the choice of wax for a specific project.
Selecting the Right Wax
The selection of wax is paramount. Soft waxes are easier to carve and manipulate, ideal for beginners and intricate details. Harder waxes provide more stability and are better suited for larger projects or those requiring robust structures. Different waxes also possess varying melting points, directly impacting the ease of use and the potential for distortions during the carving process. Common types include:
- Beeswax: A natural wax known for its malleability and pleasant scent. Often used in sculpting and art pieces.
- Paraffin Wax: A widely available and relatively inexpensive wax, often blended with other waxes to modify properties.
- Casting Wax: Specifically formulated for lost-wax casting, exhibiting consistent properties for reliable results.
Essential Tools of the Trade
Mastering wax carving necessitates familiarity with an array of specialized tools. These tools, ranging from basic sculpting knives to more sophisticated instruments, allow for precise shaping, refining, and detailing. Common tools include:
- Carving Knives: Various sizes and shapes for different carving needs.
- Modeling Tools: Used for smoothing, blending, and adding fine details.
- Heat Guns: Used for softening and shaping the wax.
- Dental Tools: Used for very fine details and intricate work.
- Wax Shavers: Used for removing excess wax.
Lost-Wax Casting: A Cornerstone Technique
Lost-wax casting, also known as investment casting, is a pivotal technique in wax carving. This ancient method enables the creation of metal objects based on a wax model. The process involves several key steps:
- Wax Model Creation: The wax model is meticulously carved to the desired specifications.
- Investment Mold Creation: The wax model is encased in a refractory mold material.
- Wax Removal: The mold is heated, melting and removing the wax.
- Metal Pouring: Molten metal is poured into the empty mold cavity.
- Mold Removal: Once the metal has cooled and solidified, the mold is carefully broken away, revealing the metal casting.
This technique is crucial in various industries, from jewelry manufacturing to dental prosthetics, allowing for the mass production of precise metal objects.
The Connection Between Meticulous Wax Carving and Jewelry Making
The jewelry industry relies heavily on wax carving. A skilled wax carver can translate a designer's vision into a tangible three-dimensional model. This model serves as the blueprint for the final piece, ensuring accuracy and detail. The intricate designs often found in high-end jewelry demand an exceptionally high level of precision, achievable only through the masterful manipulation of wax. Errors in the wax model translate directly to errors in the final metal piece, highlighting the importance of meticulous craftsmanship.
Dental Prosthetics: Precision in a Vital Field
In the realm of dental prosthetics, wax carving plays a critical role in creating accurate and functional dental appliances. Wax models are used to create crowns, bridges, and dentures, requiring exceptional precision to ensure a proper fit and function. The intricate details and careful shaping of the wax models are paramount to the overall success and comfort of the final prosthetic. The use of specialized dental waxes and tools enhances the precision and effectiveness of the process.
Wax Carving Challenges and Solutions
While wax carving offers tremendous creative potential, several challenges must be addressed:
- Wax Distortion: Temperature fluctuations can cause the wax to warp or distort. Maintaining a stable working environment is crucial.
- Tool Selection: Choosing the right tools for the job is critical. Improper tools can lead to uneven carving or damage to the model.
- Complexity of Designs: Highly intricate designs demand patience, skill, and a deep understanding of the material's properties.
- Waste Management: Wax carving generates waste, requiring careful consideration of disposal methods.
Solutions include employing appropriate temperature controls, selecting the right tools, practicing regularly to develop skill, and adopting sustainable waste management practices.
Future Trends in Wax Carving
The future of wax carving shows promising developments. Technological advancements, such as 3D printing, are being integrated into the process, offering new possibilities for design and production. However, the human element of skilled craftsmanship remains irreplaceable. The artistic and technical aspects of wax carving continue to evolve, driving innovation across diverse sectors.
The Interplay Between Digital Design and Wax Carving
The advent of CAD (Computer-Aided Design) software has revolutionized the design process in many industries, including wax carving. Digital models can be created and refined on screen, before being translated into physical wax models through techniques like 3D printing. This allows for rapid prototyping and precise adjustments, speeding up the overall production process. This integration of digital and traditional techniques represents a significant advancement in wax carving, enhancing both speed and accuracy.
Frequently Asked Questions
Q1: What type of wax is best for beginners?
A1: Soft waxes are generally recommended for beginners due to their ease of manipulation and forgiving nature. Beeswax is a good option.
Q2: How do I prevent wax from warping?
A2: Maintain a stable room temperature and avoid exposing the wax to direct sunlight or extreme heat.
Q3: What are the common mistakes made by beginners?
A3: Common mistakes include using improper tools, applying too much pressure, and not paying enough attention to detail.
Q4: Can I use household tools for wax carving?
A4: While some household tools might seem suitable, specialized carving tools are recommended for optimal results and precision.
Q5: Where can I learn more about wax carving techniques?
A5: There are numerous online resources, workshops, and courses available for those interested in learning more.
Q6: What is the best way to clean wax carving tools?
A6: Clean tools immediately after use with a solvent appropriate for the type of wax used.
Actionable Tips for Success in Wax Carving
- Start with simple projects: Gradually increase complexity as your skills improve.
- Use the right tools: Select tools appropriate for the task at hand.
- Maintain a clean workspace: A clean workspace enhances precision and prevents mistakes.
- Practice regularly: Consistent practice is key to developing proficiency.
- Experiment with different waxes: Explore various wax types to find those best suited to your needs.
- Learn from experienced carvers: Seek guidance from professionals or experienced enthusiasts.
- Invest in quality tools: High-quality tools enhance precision and longevity.
- Embrace patience: Wax carving requires patience, attention to detail, and persistence.
Conclusion
Wax carving, a timeless craft, continues to evolve, finding new applications in diverse industries. Its ability to create intricate and precise designs makes it an invaluable technique across fields. From the artistry of sculpture to the precision of dental prosthetics, the demand for skilled wax carvers remains high. By understanding the techniques, challenges, and future trends associated with wax carving, individuals can unlock a world of creative possibilities and contribute to the continued evolution of this ancient art form. The integration of digital technologies further enhances its capabilities, creating a dynamic and exciting future for this multifaceted craft. The combination of traditional skill and modern technology ensures the continued relevance and importance of wax carving for generations to come.
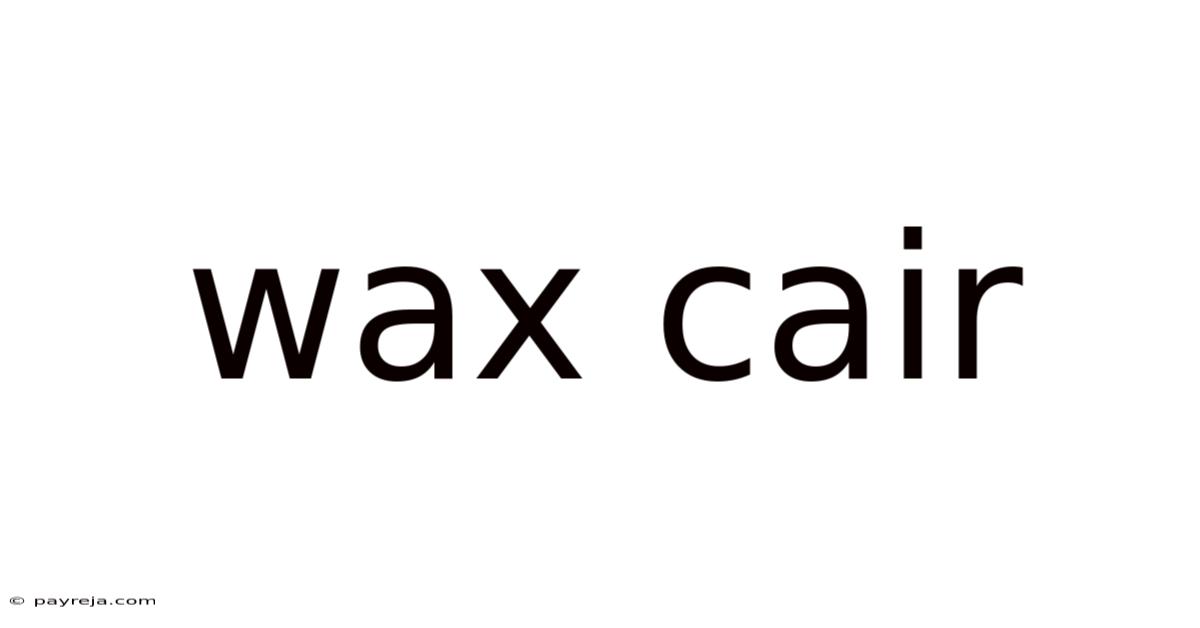
Thank you for visiting our website wich cover about Wax Cair. We hope the information provided has been useful to you. Feel free to contact us if you have any questions or need further assistance. See you next time and dont miss to bookmark.
Also read the following articles
Article Title | Date |
---|---|
Auto Glass Now Corporate Office Phone Number | Apr 22, 2025 |
Essentials 360 Reviews | Apr 22, 2025 |
What Is Shopify Crm | Apr 22, 2025 |
Sbu Artinya | Apr 22, 2025 |
Lasso Crm Training | Apr 22, 2025 |