Top 10 Manufacturing Erp Systems
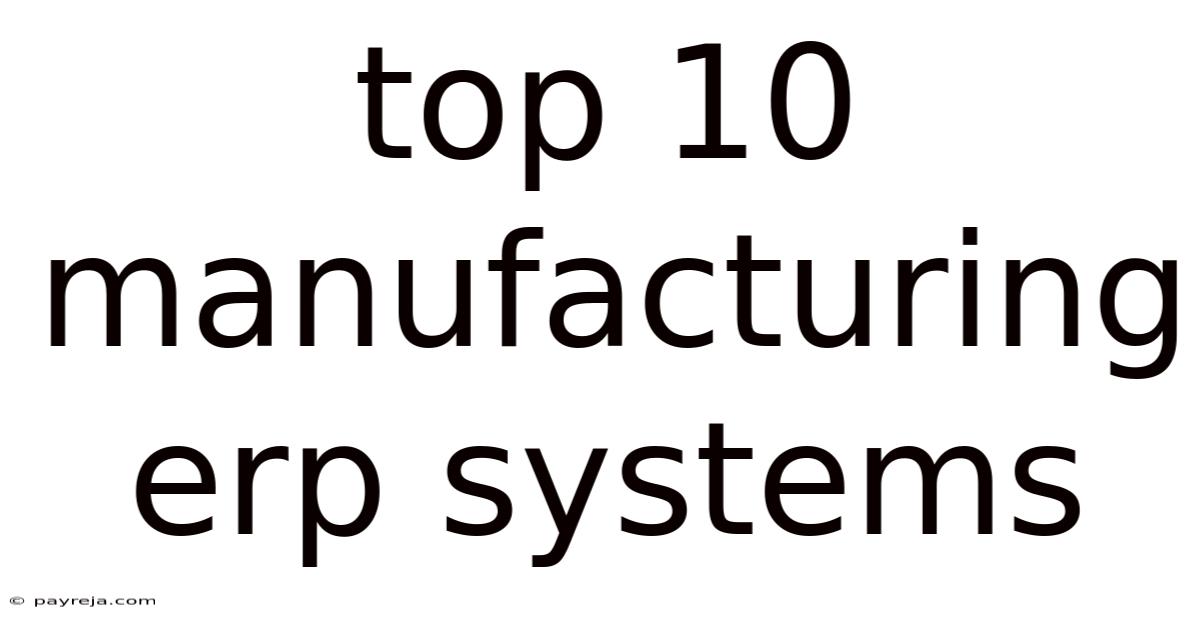
Discover more detailed and exciting information on our website. Click the link below to start your adventure: Visit Best Website meltwatermedia.ca. Don't miss out!
Table of Contents
Top 10 Manufacturing ERP Systems: A Comprehensive Guide to Streamlining Operations
Unlocking the potential of advanced manufacturing requires a robust ERP system. Which one is right for your business?
Choosing the right Manufacturing ERP system can revolutionize your operational efficiency and profitability.
Editor’s Note: This article on the top 10 manufacturing ERP systems was published on October 26, 2023, and reflects the current market landscape. The information provided is based on extensive research and analysis of industry reports and vendor offerings.
Why a Manufacturing ERP System Matters
In today's competitive manufacturing landscape, efficiency and agility are paramount. A Manufacturing Enterprise Resource Planning (ERP) system is no longer a luxury; it's a necessity for survival and growth. These integrated software solutions streamline operations across the entire manufacturing value chain, from planning and procurement to production and delivery. This results in improved inventory management, reduced costs, enhanced quality control, and better decision-making. The impact extends across various industries, including automotive, aerospace, food and beverage, pharmaceuticals, and electronics, significantly affecting production schedules, supply chain resilience, and overall profitability. Understanding the nuances of different ERP systems and selecting the best fit is crucial for realizing these benefits. The ability to manage complex manufacturing processes, track materials, and analyze real-time data empowers businesses to respond quickly to market demands and optimize their operations for maximum efficiency.
This article will provide an overview of ten leading Manufacturing ERP systems, outlining their key features, strengths, and weaknesses. It will also explore the crucial factors to consider when choosing a system tailored to specific business needs and scale. Readers will gain a comprehensive understanding of the current market landscape and insights to aid in informed decision-making.
Overview of the Article
This article delves into the features, benefits, and suitability of ten prominent Manufacturing ERP systems. We will explore their capabilities in areas such as production planning, inventory management, quality control, supply chain management, and financial reporting. The article further analyzes the factors influencing ERP selection, including scalability, integration capabilities, implementation costs, and vendor support. Readers will learn how to assess their specific requirements and choose a system that aligns with their business goals and long-term growth strategy. Finally, the article concludes with a summary of key considerations and actionable steps for successful ERP implementation.
Top 10 Manufacturing ERP Systems
The following list presents ten leading Manufacturing ERP systems, categorized for clarity and to highlight their key strengths. This is not an exhaustive list, and the ranking does not imply a superiority of one system over another; suitability depends heavily on individual business needs.
-
SAP S/4HANA: SAP's flagship ERP system is known for its comprehensive functionality, scalability, and robust integration capabilities. It's a powerful solution for large enterprises with complex manufacturing processes. However, its complexity can lead to high implementation costs and require specialized expertise.
-
Oracle NetSuite ERP: A cloud-based solution favored by mid-sized businesses, NetSuite offers strong financial management features alongside robust manufacturing capabilities. Its ease of use and scalability make it an attractive option for companies seeking a flexible, adaptable system.
-
Microsoft Dynamics 365 for Finance and Operations: Integrated with the broader Microsoft ecosystem, Dynamics 365 provides a user-friendly interface and good integration with other Microsoft products. It offers a range of manufacturing modules suitable for businesses of various sizes.
-
Infor CloudSuite Industrial (SyteLine): This industry-specific ERP system focuses on discrete manufacturing, process manufacturing, and mixed-mode environments. Its strength lies in its deep manufacturing functionalities and vertical market expertise.
-
Epicor ERP: Epicor offers various ERP solutions tailored to specific manufacturing industries. Its strength lies in its industry-specific functionalities and deep vertical market expertise. It provides solutions for discrete, process, and mixed-mode manufacturing.
-
Plex: A cloud-based ERP system designed specifically for manufacturing, Plex excels in its real-time visibility and advanced analytics capabilities. It’s particularly well-suited for companies requiring robust data analysis and digital transformation initiatives.
-
Sage X3: A mid-market ERP solution, Sage X3 offers a balance between functionality and affordability. It’s a suitable option for growing businesses seeking a scalable and relatively easy-to-implement system.
-
Acumatica: Another cloud-based ERP system, Acumatica provides strong manufacturing functionalities alongside its financial and supply chain management capabilities. Its open architecture and flexible customization options are key advantages.
-
QAD Adaptive ERP: QAD offers a specialized ERP solution for global manufacturing businesses. Its focus on global operations, supply chain visibility, and regulatory compliance makes it a strong contender for multinational corporations.
-
Exact Globe: Exact Globe provides a comprehensive ERP solution designed to handle complex manufacturing processes. It's often chosen by businesses seeking a robust system that can scale with their growth.
Key Factors to Consider When Choosing a Manufacturing ERP System
Several crucial factors must be considered when choosing an ERP system for manufacturing. These include:
-
Business Size and Complexity: The size and complexity of your manufacturing operations will significantly influence the type of ERP system you need. Large enterprises with complex processes may require a robust, enterprise-grade solution, while smaller businesses may find a mid-market system more suitable.
-
Industry-Specific Requirements: Different manufacturing industries have unique requirements. For example, the food and beverage industry will have stringent quality control and traceability needs, while the automotive industry may require sophisticated supply chain management capabilities.
-
Integration Capabilities: The ERP system should seamlessly integrate with existing systems, such as CRM, PLM, and WMS, to avoid data silos and ensure a smooth flow of information.
-
Scalability and Flexibility: The chosen system should be able to scale with your business growth, adapting to changes in production volume, product lines, and market demands.
-
Implementation Costs and Time: Consider the total cost of ownership, including software licensing, implementation services, training, and ongoing maintenance. The implementation time should also align with your business needs and timeline.
-
Vendor Support and Training: Choose a vendor that offers reliable support, comprehensive training, and timely updates to ensure the smooth operation of the system.
-
Cloud vs. On-Premise Deployment: Consider the advantages and disadvantages of cloud-based vs. on-premise deployment. Cloud-based systems offer flexibility and scalability, while on-premise systems provide greater control and customization options.
The Interplay Between Supply Chain Management and Manufacturing ERP Systems
Supply chain management (SCM) is inextricably linked to the effectiveness of a manufacturing ERP system. A robust ERP system provides real-time visibility into the entire supply chain, from raw material sourcing to finished goods delivery. This visibility enables proactive management of inventory levels, supplier relationships, and logistics, minimizing disruptions and optimizing efficiency. Effective SCM integration within the ERP system ensures accurate forecasting of demand, efficient procurement processes, and timely delivery of products to customers. This reduces lead times, minimizes waste, and enhances overall supply chain resilience. Poor SCM integration, conversely, can lead to stockouts, production delays, and increased costs.
Roles and Real-World Examples:
-
Production Planning: ERP systems enable optimized production scheduling by considering factors like material availability, capacity constraints, and customer demand. For example, a clothing manufacturer can use its ERP system to plan production runs based on seasonal trends and inventory levels.
-
Inventory Management: Real-time inventory tracking ensures that the right materials are available at the right time, minimizing stockouts and reducing waste. An electronics manufacturer can use its ERP system to track the availability of critical components and proactively manage their procurement.
-
Quality Control: Integrated quality control modules help manufacturers monitor product quality throughout the production process, identifying and resolving defects early on. A pharmaceutical company can use its ERP system to track batch numbers, ensuring traceability and compliance with regulatory standards.
Risks and Mitigations:
-
High Implementation Costs: ERP implementations can be expensive and time-consuming. Mitigation strategies include careful planning, selecting a suitable vendor, and phased implementation.
-
Data Migration Challenges: Migrating data from legacy systems can be complex and error-prone. Careful data cleansing, validation, and testing are essential to ensure data accuracy.
-
Integration Issues: Integrating the ERP system with other systems can be challenging. Selecting a system with strong integration capabilities and engaging experienced integration specialists can help mitigate these issues.
Impact and Implications:
Effective implementation of a manufacturing ERP system can significantly improve operational efficiency, reduce costs, enhance product quality, and improve customer satisfaction. It can also contribute to better decision-making, leading to improved profitability and sustainable growth. Conversely, a poorly implemented or unsuitable ERP system can lead to increased costs, operational disruptions, and decreased competitiveness.
A Deeper Dive into Supply Chain Management
Effective supply chain management (SCM) is vital for modern manufacturing. It involves the planning, sourcing, and management of all resources involved in the production and delivery of goods. Disruptions in the supply chain can have devastating consequences, leading to production delays, stockouts, and financial losses. Therefore, integrating SCM capabilities into an ERP system is crucial. This integration enables real-time visibility into the entire supply chain, allowing for proactive identification and mitigation of potential risks.
Cause-and-Effect Analysis:
-
Poor Supplier Relationships: Poor communication and collaboration with suppliers can lead to delays in material delivery, impacting production schedules.
-
Inaccurate Demand Forecasting: Inaccurate forecasting can result in either excess inventory or stockouts, leading to increased costs or lost sales.
-
Inefficient Logistics: Inefficient logistics processes, such as inadequate transportation planning or warehouse management, can delay product delivery and increase costs.
Industry Examples:
-
The automotive industry relies heavily on efficient supply chains to ensure the timely delivery of parts and components for vehicle assembly. Disruptions in the supply chain can lead to significant production delays and financial losses.
-
The pharmaceutical industry must maintain strict quality control and traceability throughout the supply chain to ensure product safety and regulatory compliance. Any disruption can lead to significant recalls and financial penalties.
Frequently Asked Questions (FAQ)
Q1: How much does a manufacturing ERP system cost?
A1: The cost of a manufacturing ERP system varies widely depending on several factors, including the size of your business, the complexity of your manufacturing processes, the number of users, and the features included. Expect costs to range from several thousand dollars for smaller systems to hundreds of thousands or even millions for enterprise-level solutions.
Q2: How long does it take to implement a manufacturing ERP system?
A2: Implementation time also varies greatly, depending on the complexity of the system, the size of your business, and the level of customization required. Smaller implementations can take several months, while larger implementations may take a year or more.
Q3: What are the key benefits of using a manufacturing ERP system?
A3: Key benefits include improved operational efficiency, reduced costs, enhanced quality control, better inventory management, improved supply chain visibility, and better decision-making.
Q4: How can I choose the right ERP system for my manufacturing business?
A4: Consider factors like your business size, industry-specific requirements, integration needs, scalability, budget, and vendor support when choosing an ERP system. It's also beneficial to conduct a thorough needs assessment and compare different systems before making a decision.
Q5: What are the common challenges associated with ERP implementation?
A5: Common challenges include high implementation costs, data migration issues, integration difficulties, user adoption issues, and lack of sufficient training. Careful planning, adequate resources, and experienced implementation partners can help mitigate these challenges.
Q6: What are some key metrics for measuring the success of an ERP implementation?
A6: Key metrics include improved order fulfillment rates, reduced inventory holding costs, increased production efficiency, shorter lead times, and enhanced customer satisfaction.
Actionable Tips for Successful ERP Implementation
-
Conduct a thorough needs assessment: Define your business requirements and objectives before selecting an ERP system.
-
Choose the right vendor: Select a vendor that offers a suitable system, reliable support, and comprehensive training.
-
Develop a detailed implementation plan: Create a comprehensive plan that outlines timelines, resources, and responsibilities.
-
Involve key stakeholders: Engage key users and stakeholders throughout the implementation process to ensure buy-in and smooth transition.
-
Provide adequate training: Provide thorough training to users to ensure they can effectively utilize the system.
-
Test thoroughly: Conduct thorough testing before going live to identify and resolve any issues.
-
Monitor and optimize: Continuously monitor the system's performance and make adjustments as needed to optimize its effectiveness.
Conclusion
Selecting and implementing a manufacturing ERP system is a significant undertaking but a crucial step towards enhancing operational efficiency, improving profitability, and driving sustainable growth. By carefully considering the factors outlined in this article, businesses can choose a system that aligns with their specific needs and lays the foundation for a streamlined, data-driven manufacturing operation. The synergy between a robust ERP system and efficient supply chain management creates a powerful engine for success in the modern manufacturing landscape. Remember that continuous optimization and adaptation are key to maximizing the long-term benefits of your chosen ERP solution. The future of manufacturing depends on embracing technology, and the right ERP system is a cornerstone of that transformation.
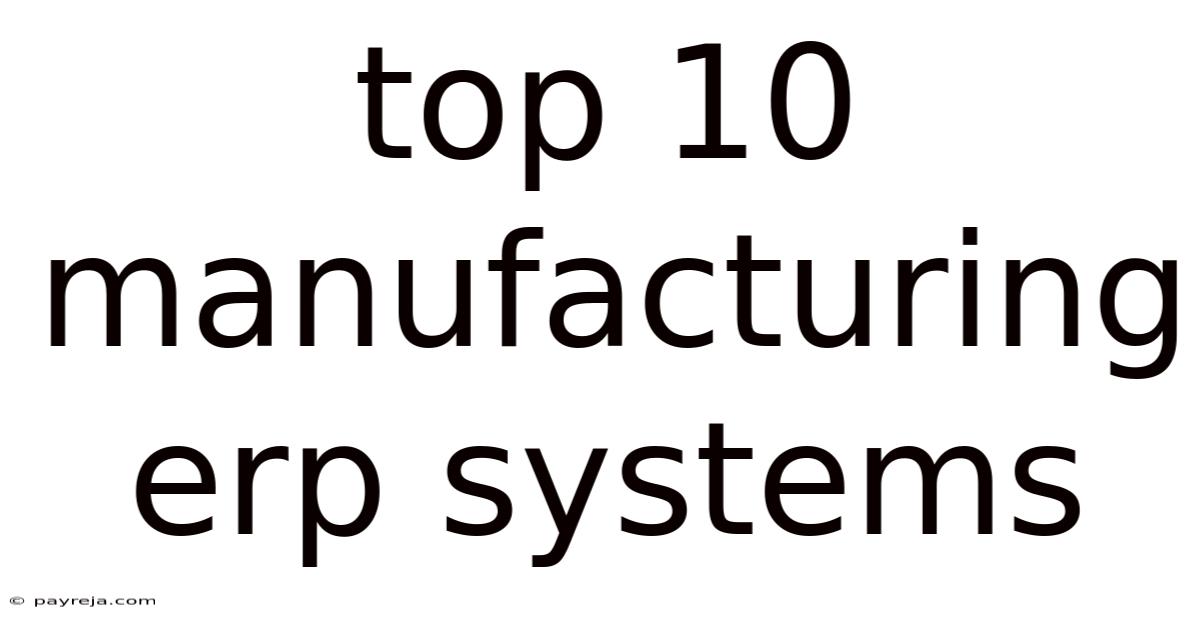
Thank you for visiting our website wich cover about Top 10 Manufacturing Erp Systems. We hope the information provided has been useful to you. Feel free to contact us if you have any questions or need further assistance. See you next time and dont miss to bookmark.
Also read the following articles
Article Title | Date |
---|---|
Infor Erp Xa | Apr 17, 2025 |
Erp Tms | Apr 17, 2025 |
How To Get Tree Sap Off Skin | Apr 17, 2025 |
Fivem Erp Videos | Apr 17, 2025 |
How To Remove Tree Sap From Car Paint | Apr 17, 2025 |