Top 10 Erp Systems For Manufacturing
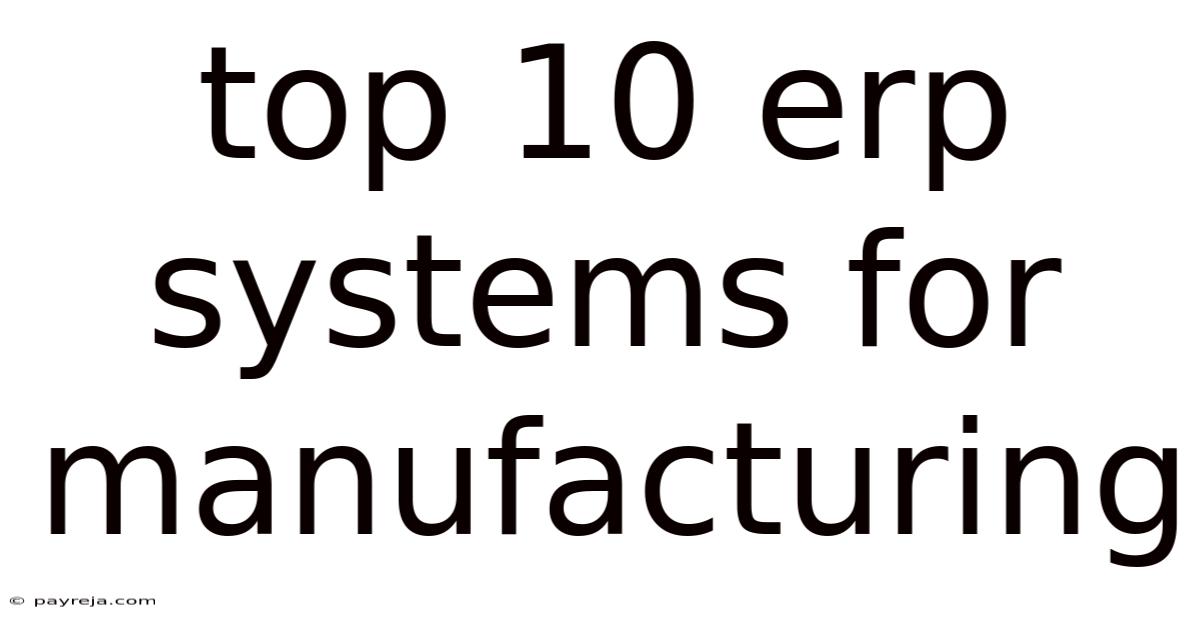
Discover more detailed and exciting information on our website. Click the link below to start your adventure: Visit Best Website meltwatermedia.ca. Don't miss out!
Table of Contents
Top 10 ERP Systems for Manufacturing: A Comprehensive Guide
What if selecting the right ERP system could dramatically streamline your manufacturing processes and boost profitability? Investing in the right ERP is no longer a luxury, but a necessity for modern manufacturing competitiveness.
Editor’s Note: This article on the top 10 ERP systems for manufacturing has been updated today to reflect the latest market trends and software features.
Why ERP Matters for Manufacturing
The manufacturing industry faces intense pressure to optimize production, manage complex supply chains, and meet ever-changing customer demands. Enterprise Resource Planning (ERP) systems provide a centralized platform to integrate various business functions, from planning and procurement to production and distribution. A well-implemented ERP system offers significant advantages, including:
- Improved Efficiency: Streamlined workflows and automated processes reduce manual tasks and errors, leading to increased productivity.
- Enhanced Collaboration: Real-time data sharing across departments fosters better communication and coordination.
- Better Inventory Management: Accurate inventory tracking minimizes stockouts and excess inventory, optimizing carrying costs.
- Reduced Costs: Improved efficiency, minimized waste, and optimized resource allocation contribute to significant cost savings.
- Data-Driven Decision Making: Access to real-time data and comprehensive reporting enables informed strategic decisions.
- Increased Agility: ERP systems facilitate faster response times to market changes and customer demands.
- Better Compliance: Streamlined processes ensure compliance with industry regulations and standards.
This article will explore ten leading ERP systems specifically designed to address the unique challenges and opportunities within the manufacturing sector. We’ll examine their key features, benefits, target markets, and considerations for implementation.
Overview of the Article
This comprehensive guide will delve into the top 10 ERP systems for manufacturing, providing an in-depth analysis of each platform's capabilities, strengths, and weaknesses. Readers will gain a clear understanding of the factors to consider when choosing an ERP system and how to select the best fit for their specific needs and business goals. The article will also examine the crucial relationship between data analytics and successful ERP implementation in manufacturing. Finally, it will offer practical tips for a smooth implementation process.
Showcase of Research and Data-Driven Insights
The rankings and analysis presented in this article are based on a combination of factors, including market share, industry reviews (e.g., Gartner, IDC), user feedback, and feature comparisons. Data from reputable industry analysts and case studies from successful ERP implementations in manufacturing companies have been utilized to ensure accuracy and provide valuable insights.
Top 10 ERP Systems for Manufacturing
While the "top" ERP systems can vary based on specific needs and perspectives, the following list represents a strong selection of leading platforms frequently recognized for their capabilities in the manufacturing sector. Note that this is not an exhaustive list, and many other excellent ERP solutions exist. The order does not reflect a definitive ranking.
-
SAP S/4HANA: A comprehensive suite offering advanced functionalities for manufacturing, including production planning, quality management, and supply chain optimization. SAP's strength lies in its scalability and ability to handle complex manufacturing processes in large enterprises.
-
Oracle NetSuite: A cloud-based ERP system providing a strong platform for mid-sized and large manufacturing businesses. Known for its robust financial management capabilities and integration with other business applications.
-
Microsoft Dynamics 365: A highly versatile ERP system offering various modules tailored to different manufacturing needs. Its strength lies in its ease of use and integration with the Microsoft ecosystem.
-
Infor CloudSuite Industrial (SyteLine): Designed specifically for discrete and process manufacturing, offering industry-specific functionalities and advanced planning and scheduling tools.
-
Epicor ERP: A well-established ERP system with a strong focus on manufacturing, providing comprehensive solutions for discrete, process, and hybrid manufacturing environments.
-
Sage X3: A cloud-based ERP system suitable for mid-sized manufacturers, offering a good balance of functionality and affordability. Its ease of use and strong customer support are key benefits.
-
Acumatica: A cloud-based ERP offering a flexible and scalable platform with strong manufacturing capabilities. Acumatica is known for its open architecture and ease of customization.
-
Odoo: An open-source ERP system with a wide range of modules suitable for various business sizes and industries, including manufacturing. Its flexibility and cost-effectiveness make it an attractive option.
-
SYSPRO: A long-standing ERP solution known for its strength in manufacturing, offering industry-specific functionalities and robust reporting tools. It's particularly well-suited for companies requiring highly configurable solutions.
-
BlueCherry: A cloud-based ERP system tailored specifically to the apparel, footwear, and other fashion-related manufacturing industries. It offers deep industry-specific functionalities for managing complex production processes.
Key Takeaways: Choosing the Right ERP System
Feature | Importance | Considerations |
---|---|---|
Scalability | Ability to adapt to future growth and changing business needs. | Consider future expansion plans and projected data volumes. |
Industry-Specific Features | Tailored functionalities for unique manufacturing processes and challenges. | Evaluate the system's alignment with your specific industry and manufacturing type. |
Integration Capabilities | Seamless data exchange with other business applications. | Assess compatibility with existing systems and future integration requirements. |
User-Friendliness | Ease of use and intuitive interface for efficient adoption by employees. | Prioritize systems with clear navigation, comprehensive training, and user-friendly interfaces. |
Cost of Implementation | Total cost of ownership, including software licensing, implementation, and support. | Carefully evaluate all associated costs, including ongoing maintenance and support fees. |
Cloud vs. On-Premise | Deployment model based on your infrastructure, security, and budget. | Weigh the pros and cons of cloud-based vs. on-premise deployments based on your specific needs. |
The Connection Between Data Analytics and ERP Implementation
Effective ERP implementation goes beyond simply installing software. A crucial component is the integration and utilization of robust data analytics. By leveraging the vast data generated within the ERP system, manufacturers can gain valuable insights into operational efficiency, supply chain optimization, and overall profitability. This data can be used for:
- Predictive Maintenance: Forecasting potential equipment failures to minimize downtime.
- Demand Forecasting: Accurately predicting future demand to optimize production planning.
- Supply Chain Optimization: Identifying bottlenecks and inefficiencies in the supply chain.
- Quality Control: Tracking and analyzing quality metrics to identify areas for improvement.
- Performance Monitoring: Tracking key performance indicators (KPIs) to monitor progress and identify areas for improvement.
Roles and Real-World Examples: Data Analytics in Manufacturing ERP
Many successful manufacturers leverage data analytics embedded in their ERP systems. For instance, a food processing company might use real-time data on production line speeds and yields to predict potential delays or quality issues, allowing for proactive adjustments. A car manufacturer might use predictive analytics to schedule preventative maintenance on its assembly line robots, minimizing production downtime.
Risks and Mitigations: ERP Implementation Challenges
Implementing an ERP system can present challenges, including:
- High Initial Costs: The investment in software, implementation, and training can be substantial.
- Integration Complexity: Integrating the ERP system with existing systems can be complex and time-consuming.
- Data Migration: Transferring data from legacy systems can be challenging and prone to errors.
- User Adoption: Resistance to change from employees can hinder successful implementation.
- Lack of Expertise: A shortage of skilled personnel can delay implementation and create challenges.
Mitigating these risks involves thorough planning, selecting the right implementation partner, providing comprehensive training, and addressing employee concerns proactively.
Impact and Implications: The Long-Term Benefits of ERP in Manufacturing
A successful ERP implementation can deliver significant long-term benefits, including increased productivity, reduced costs, improved quality, and enhanced agility. This translates to a stronger competitive position in the market and improved profitability.
Reinforcing the Connection in the Conclusion: Data Analytics and ERP Success
The success of an ERP system in manufacturing is intrinsically linked to the effective utilization of data analytics. By leveraging data-driven insights, manufacturers can optimize processes, improve decision-making, and gain a competitive edge.
Dive Deeper into Data Analytics: Types and Applications
Data analytics in the context of manufacturing ERP utilizes various techniques, including:
- Descriptive Analytics: Summarizing past data to understand trends and patterns.
- Diagnostic Analytics: Identifying the root causes of problems and issues.
- Predictive Analytics: Forecasting future outcomes based on historical data and patterns.
- Prescriptive Analytics: Recommending actions to optimize performance and outcomes.
These techniques can be applied across various aspects of manufacturing, from production planning and inventory management to supply chain optimization and quality control.
FAQ Section
Q1: What is the average cost of implementing an ERP system for manufacturing?
A1: The cost varies significantly depending on the size of the company, the complexity of the system, and the chosen implementation partner. Expect a range from tens of thousands to millions of dollars.
Q2: How long does it typically take to implement an ERP system?
A2: Implementation timelines vary, but it typically ranges from several months to over a year, depending on the project's scope and complexity.
Q3: What are the key features to look for in a manufacturing ERP system?
A3: Key features include production planning, inventory management, supply chain management, quality control, and robust reporting and analytics.
Q4: How can I ensure successful user adoption of a new ERP system?
A4: Thorough training, clear communication, and addressing employee concerns are crucial. Involve employees in the implementation process to gain buy-in.
Q5: What are the common challenges faced during ERP implementation?
A5: Common challenges include data migration issues, integration complexities, user resistance, and cost overruns.
Q6: Can a small manufacturing company benefit from an ERP system?
A6: Yes, even small manufacturers can benefit from ERP systems, especially cloud-based options offering scalability and affordability.
Actionable Tips on ERP Selection and Implementation
- Define your business needs: Clearly articulate your requirements and goals for the ERP system.
- Conduct thorough research: Evaluate different ERP vendors and their offerings.
- Seek expert advice: Consult with ERP consultants to guide the selection and implementation process.
- Develop a detailed implementation plan: Outline all phases of the project, including timelines and responsibilities.
- Invest in thorough employee training: Ensure employees are adequately trained to use the new system.
- Establish a strong change management process: Address employee concerns and foster buy-in.
- Monitor performance and make adjustments: Continuously monitor the system's performance and make necessary adjustments.
- Establish a robust support system: Secure ongoing support and maintenance from the vendor or a qualified third party.
Strong Final Conclusion
Selecting and implementing the right ERP system is a crucial investment for modern manufacturers. This article has explored the top 10 ERP systems currently available, highlighting their key features and benefits. By understanding the importance of data analytics and addressing potential challenges, manufacturers can successfully leverage an ERP system to optimize operations, boost productivity, and gain a competitive advantage in today's dynamic market. The journey towards digital transformation in manufacturing begins with a strategic and well-informed ERP selection.
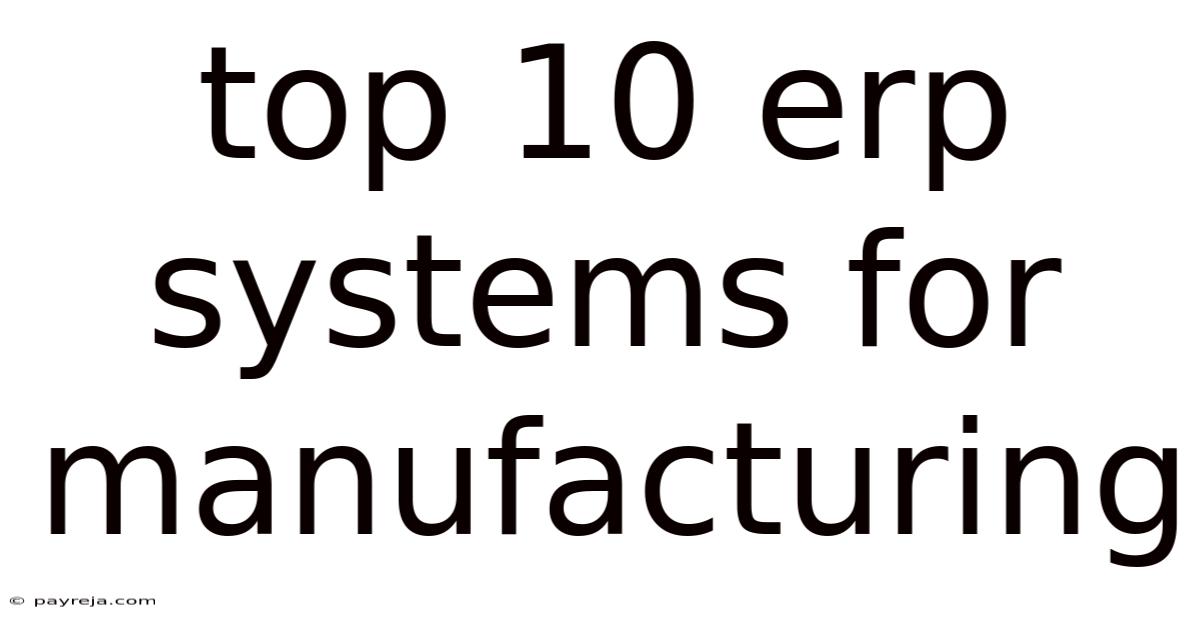
Thank you for visiting our website wich cover about Top 10 Erp Systems For Manufacturing. We hope the information provided has been useful to you. Feel free to contact us if you have any questions or need further assistance. See you next time and dont miss to bookmark.
Also read the following articles
Article Title | Date |
---|---|
How To Get Tree Sap Off Of Car | Apr 17, 2025 |
How Do You Clean Tree Sap Off A Car | Apr 17, 2025 |
Hvac Erp | Apr 17, 2025 |
Erp Software For Plastic Injection Molding | Apr 17, 2025 |
Erp System Implementation Project Plan | Apr 17, 2025 |