Pipeline Appurtenances
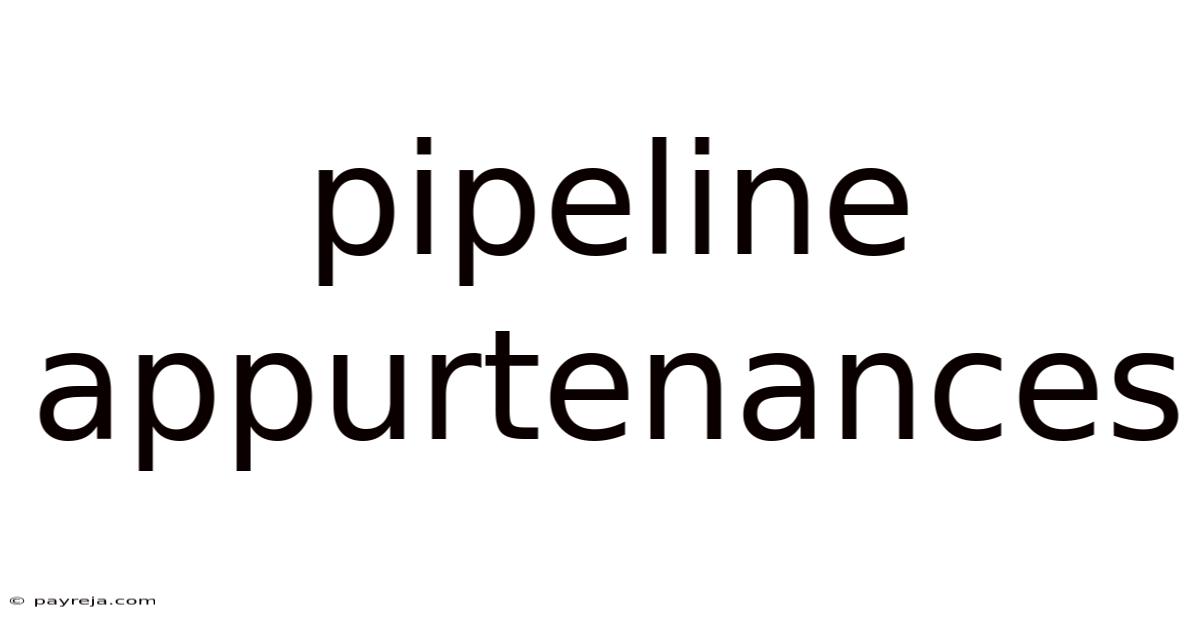
Discover more detailed and exciting information on our website. Click the link below to start your adventure: Visit Best Website meltwatermedia.ca. Don't miss out!
Table of Contents
Unveiling the Crucial Role of Pipeline Appurtenances: A Comprehensive Guide
What if understanding the intricacies of pipeline appurtenances could significantly enhance pipeline safety and efficiency?
Pipeline appurtenances are not mere accessories; they are critical components that ensure the safe, efficient, and reliable operation of pipeline systems.
Editor’s Note: This article on pipeline appurtenances has been published today, providing readers with the latest insights and best practices in this crucial field.
Why Pipeline Appurtenances Matter
Pipeline appurtenances are the essential components that connect, control, protect, and monitor pipelines. They are far from mere add-ons; they are integral to the safe and efficient transportation of liquids and gases across vast distances. Their proper selection, installation, and maintenance directly impact operational efficiency, safety, environmental protection, and the overall longevity of the pipeline system. From preventing leaks and corrosion to facilitating maintenance and monitoring, appurtenances play a multifaceted role in the entire pipeline lifecycle. Understanding their functionality is crucial for engineers, operators, and anyone involved in the design, construction, or maintenance of pipelines. This includes considerations for various pipeline types, such as oil and gas pipelines, water pipelines, and even slurry pipelines, each with unique appurtenance requirements.
This article will cover key aspects of pipeline appurtenances, providing a comprehensive understanding of their types, functions, and significance in ensuring pipeline integrity. Readers will gain insights into different appurtenance categories, their applications, and the importance of proper selection and maintenance. The article also explores the connection between proper appurtenance selection and overall pipeline safety, highlighting the potential consequences of negligence and emphasizing best practices for effective management.
Overview of the Article
This article will delve into the diverse world of pipeline appurtenances, starting with a detailed classification of these essential components. We will explore specific examples of common appurtenances, examining their functionality and applications within different pipeline systems. Furthermore, the article will analyze the critical role of appurtenances in ensuring pipeline safety and environmental protection, emphasizing the importance of regular inspection and maintenance. Finally, we will discuss the selection criteria for appropriate appurtenances, emphasizing the importance of considering factors like pipeline material, fluid properties, and operational conditions. The article concludes with a discussion on emerging trends and technologies in pipeline appurtenance design and maintenance.
Research Methodology
This article draws upon extensive research encompassing industry standards (like ASME, API, and ISO), technical publications, industry reports, and case studies from reputable sources. The information presented is synthesized from a variety of sources to ensure accuracy and completeness. A structured approach, emphasizing clear definitions, examples, and logical connections, has been employed to ensure readability and understanding.
Key Insights: A Summary
Insight | Description |
---|---|
Diverse Appurtenance Types | Pipelines utilize a wide array of appurtenances, each with specific functions and applications. |
Safety and Environmental Protection | Proper appurtenances are vital for leak prevention, reducing environmental risks, and ensuring operator safety. |
Impact of Material Selection | The choice of appurtenance material significantly impacts durability, corrosion resistance, and overall lifespan. |
Importance of Regular Inspection | Routine inspections and maintenance are crucial for identifying potential issues and preventing costly failures. |
Advanced Technologies | Innovative appurtenances and monitoring technologies enhance pipeline efficiency and safety. |
Regulatory Compliance | Adherence to industry standards and regulations is paramount for safe and legal pipeline operations. |
Core Discussion: Types and Functions of Pipeline Appurtenances
Pipeline appurtenances can be broadly categorized based on their function. These include:
1. Valves: These are essential for controlling the flow of fluids within the pipeline. Different valve types, such as gate valves, globe valves, ball valves, and check valves, serve distinct purposes depending on the specific application and flow requirements. The selection of the appropriate valve type considers factors like pressure, temperature, fluid viscosity, and required flow control precision.
2. Fittings: Fittings are used to connect pipeline sections, change direction, or alter the pipeline's diameter. Common fittings include elbows, tees, reducers, and couplings. The material and design of these fittings must be compatible with the pipeline material and the operating conditions to ensure a secure and leak-free connection. Proper welding or joining techniques are crucial for maintaining pipeline integrity.
3. Meters and Gauges: These appurtenances monitor pipeline parameters such as flow rate, pressure, and temperature. Accurate measurement is crucial for operational efficiency, safety monitoring, and leak detection. Modern systems often incorporate advanced sensors and data logging capabilities for real-time monitoring and remote control.
4. Support Structures: These include anchors, clamps, and hangers designed to support the pipeline and prevent sagging or movement. Proper support is crucial for preventing stress buildup and ensuring the long-term integrity of the pipeline. The design of support structures must consider factors like soil conditions, pipeline weight, and thermal expansion.
5. Protection Devices: These appurtenances protect the pipeline from external factors such as corrosion and damage. This includes cathodic protection systems to mitigate corrosion, coatings to prevent external corrosion, and protective casings for buried pipelines. Regular inspections and maintenance of these protective measures are essential for maintaining pipeline integrity.
6. Pigging Systems: Pigging systems use specialized devices called "pigs" to clean, inspect, or perform maintenance operations within the pipeline. These systems improve pipeline efficiency and safety by removing accumulated debris or performing internal inspections without interrupting flow.
The Interplay Between Corrosion and Pipeline Appurtenances
Corrosion is a significant threat to pipeline integrity, and appurtenances play a vital role in mitigating its effects. The choice of materials for appurtenances, particularly in areas susceptible to corrosion, is crucial. Materials like stainless steel, ductile iron, and certain polymers offer superior corrosion resistance. Furthermore, cathodic protection systems, often integrated into the pipeline and its appurtenances, provide an electrochemical barrier to prevent corrosion. Regular inspections to detect corrosion and timely repairs are paramount in preventing catastrophic failures. Failure to address corrosion adequately can lead to leaks, spills, and significant environmental damage.
Roles and Real-World Examples
Cathodic protection systems: These are routinely used on pipelines, especially buried ones, to prevent corrosion. They involve introducing a sacrificial anode or applying an electrical current to counteract the electrochemical reactions that cause corrosion. Failure of the cathodic protection system on an underground pipeline can lead to significant corrosion damage over time.
Pressure relief valves (PRVs): These valves automatically release excess pressure within the pipeline to prevent over-pressurization, a major safety hazard. They are crucial in situations such as unexpected pressure surges. A failure to properly maintain or select an appropriate PRV can lead to pipeline ruptures.
Flow meters: Accurate flow measurement is crucial for pipeline operations. Advanced flow meters with automated data logging capabilities enhance the efficiency of operations and allow for better monitoring of the pipeline’s performance. Inaccurate flow measurements can lead to production losses or operational inefficiencies.
Risks and Mitigations
Corrosion: The primary risk is material degradation, leading to leaks and failures. Mitigation involves selecting corrosion-resistant materials, implementing cathodic protection, and regular inspection.
Improper Installation: Incorrect installation can lead to leaks and failures. Mitigation involves using skilled labor, adhering to strict installation procedures, and rigorous quality control.
Lack of Maintenance: Neglecting maintenance increases the risk of failures. Mitigation involves developing and adhering to a comprehensive maintenance schedule, including regular inspections and timely repairs.
Material Selection Errors: Choosing inappropriate materials for specific environments can compromise the longevity and performance of appurtenances. Mitigation involves careful consideration of material properties, environmental factors, and operational parameters.
Impact and Implications
The proper selection and maintenance of pipeline appurtenances are critical for maintaining pipeline safety and minimizing environmental risks. Leaks, spills, and explosions caused by appurtenance failures can result in significant economic losses, environmental damage, and potential loss of life. On the other hand, the use of advanced appurtenances and monitoring technologies can enhance efficiency, optimize operations, and improve overall pipeline reliability.
Reinforcing the Connection in the Conclusion
Corrosion and pipeline appurtenances are inextricably linked. The choice of corrosion-resistant materials, the implementation of cathodic protection, and the regular inspection of appurtenances are all essential strategies for mitigating the risks associated with corrosion and ensuring pipeline integrity. Understanding this relationship is vital for ensuring the safe and efficient operation of pipeline systems.
Diving Deeper into Corrosion
Corrosion is an electrochemical process that involves the degradation of metal due to its interaction with its environment. Various factors influence the rate of corrosion, including the type of metal, the environmental conditions (moisture, temperature, pH), and the presence of corrosive agents. Different types of corrosion exist, including uniform corrosion, pitting corrosion, galvanic corrosion, and stress corrosion cracking. Understanding the specific type of corrosion affecting a pipeline is crucial for selecting appropriate mitigation strategies. This often involves sophisticated analysis of the pipeline environment and materials.
Frequently Asked Questions (FAQ)
Q1: What are the most common types of pipeline appurtenances?
A1: Common types include valves (gate, globe, ball, check), fittings (elbows, tees, reducers), meters and gauges (flow meters, pressure gauges), support structures (anchors, clamps), protection devices (coatings, cathodic protection), and pigging systems.
Q2: How often should pipeline appurtenances be inspected?
A2: Inspection frequency depends on factors like pipeline location, operating conditions, and material type. Regular inspections, often following a pre-defined schedule, are essential for early detection of potential problems.
Q3: What are the consequences of neglecting pipeline appurtenance maintenance?
A3: Neglecting maintenance can lead to leaks, spills, equipment failures, reduced operational efficiency, and increased safety risks. It can also result in substantial financial penalties and environmental damage.
Q4: How are pipeline appurtenances selected?
A4: Appurtenance selection involves considering factors like pipeline material, fluid properties, operating pressure and temperature, flow rate, and regulatory requirements. Engineering calculations and simulations are often employed to ensure appropriate selection.
Q5: What are some advanced technologies used in pipeline appurtenances?
A5: Smart pigging technologies, advanced flow meters with remote monitoring capabilities, and corrosion monitoring systems using sensors are examples of advanced technologies improving pipeline efficiency and safety.
Q6: What role do regulations play in pipeline appurtenance selection and maintenance?
A6: Regulations set minimum standards for pipeline design, construction, operation, and maintenance. Compliance with relevant regulations is crucial for ensuring pipeline safety and preventing environmental damage.
Actionable Tips on Pipeline Appurtenance Management
- Develop a comprehensive maintenance schedule: Regular inspections, preventive maintenance, and timely repairs are crucial.
- Utilize advanced inspection technologies: Employ smart pigging, remotely operated vehicles (ROVs), and other technologies for thorough and efficient inspections.
- Properly select materials: Choose corrosion-resistant materials appropriate for the pipeline environment and operating conditions.
- Ensure skilled labor: Proper installation is critical; use qualified personnel for installation and maintenance.
- Implement robust risk management protocols: Identify potential hazards and develop mitigation strategies to minimize risks.
- Maintain detailed records: Keep thorough records of inspections, maintenance activities, and any repairs performed.
- Stay updated on industry standards: Keep abreast of changes in regulations, best practices, and advanced technologies.
- Invest in training: Ensure personnel are adequately trained on pipeline appurtenance operation, maintenance, and safety procedures.
Conclusion
Pipeline appurtenances are not simply supplementary components; they are critical for the safe, efficient, and reliable operation of pipeline systems. Understanding their diverse types, functions, and the critical role they play in preventing corrosion and ensuring overall pipeline integrity is paramount. By implementing proactive maintenance, employing advanced technologies, and adhering to industry best practices, operators can significantly enhance the safety and efficiency of their pipeline systems, minimizing risks and maximizing economic benefits. The future of pipeline management will increasingly rely on advanced technologies and data-driven insights to ensure the reliable and sustainable transportation of essential resources.
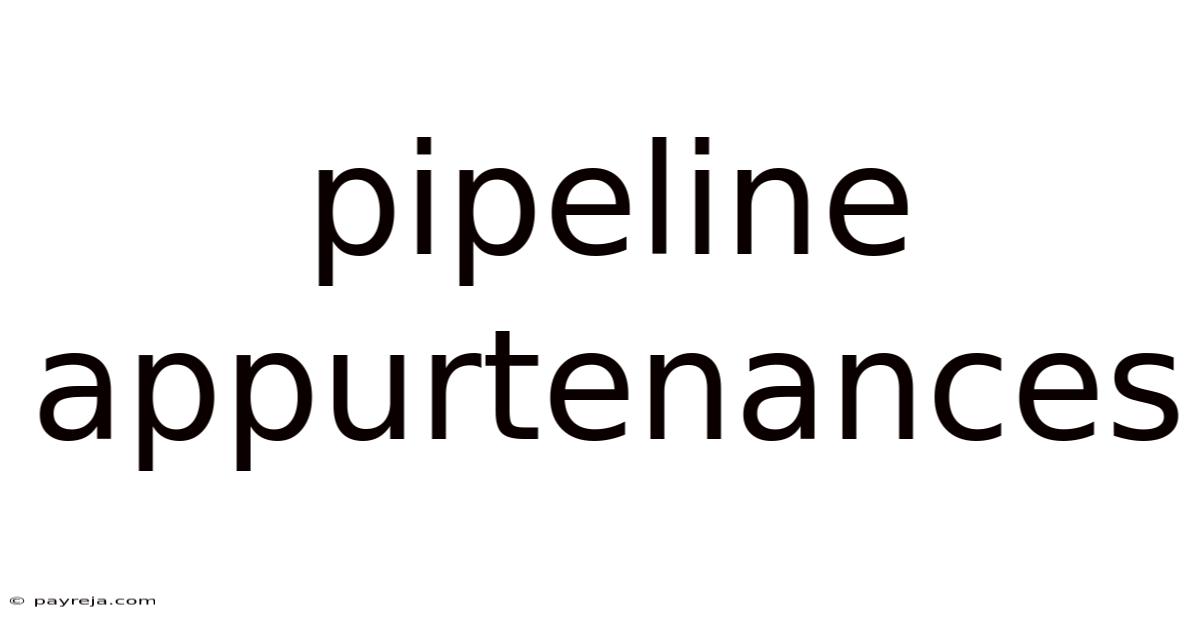
Thank you for visiting our website wich cover about Pipeline Appurtenances. We hope the information provided has been useful to you. Feel free to contact us if you have any questions or need further assistance. See you next time and dont miss to bookmark.
Also read the following articles
Article Title | Date |
---|---|
Notion Real Estate Crm Template | Apr 26, 2025 |
Piper Drive Apartments | Apr 26, 2025 |
What Is Relationship Management Theory | Apr 26, 2025 |
Sonar Social Listening | Apr 26, 2025 |
Union Square Crm | Apr 26, 2025 |