Improve Piping
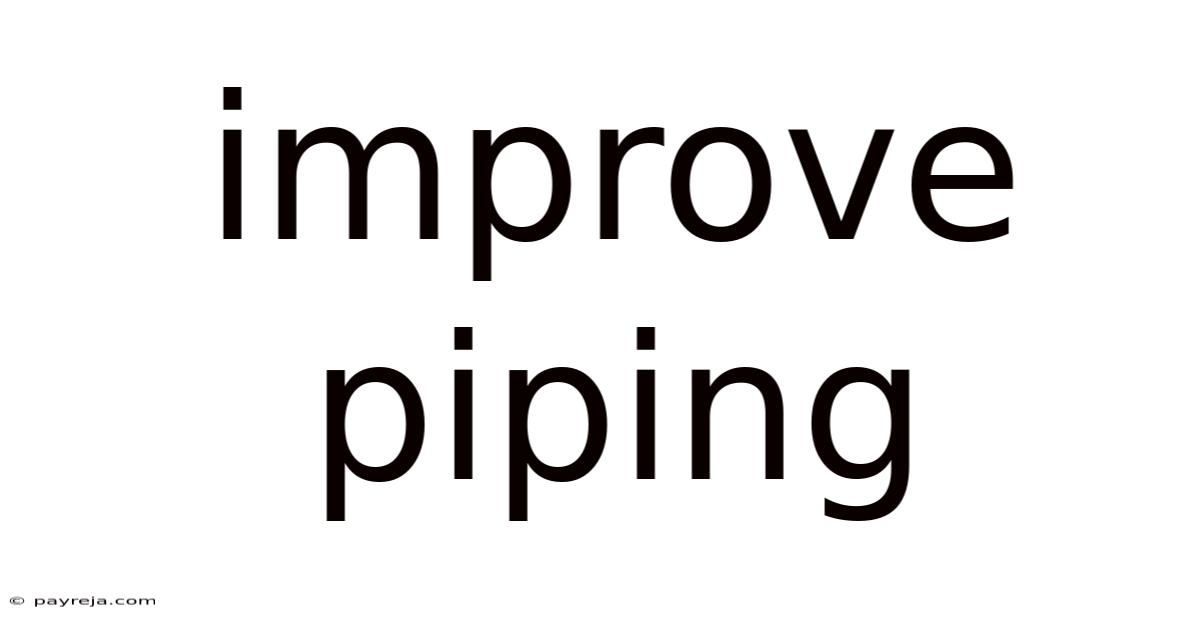
Discover more detailed and exciting information on our website. Click the link below to start your adventure: Visit Best Website meltwatermedia.ca. Don't miss out!
Table of Contents
Optimize Your Piping Systems: A Comprehensive Guide to Improvement
What if optimizing your piping systems could significantly reduce operational costs and enhance safety? Improved piping design and maintenance are crucial for efficient operations across numerous industries.
Editor’s Note: This article on improving piping systems has been published today, offering the latest insights and best practices in the field.
Why Improving Piping Systems Matters
Efficient and reliable piping systems are foundational to countless industries, from oil and gas to pharmaceuticals and water treatment. Suboptimal piping design, inadequate maintenance, or the use of inappropriate materials can lead to significant consequences: costly downtime, production losses, safety hazards, environmental damage, and increased operational expenses. Improving piping systems directly impacts profitability, safety, and environmental responsibility. The implications extend to minimizing leaks, reducing energy consumption, extending the lifespan of equipment, and enhancing overall operational efficiency. This article will delve into various aspects of piping system optimization, providing actionable strategies for improvement. Understanding these improvements is critical for optimizing the efficiency and longevity of any facility relying on piping infrastructure. Keywords like pipe integrity management, leak detection, corrosion prevention, and piping design optimization are central to this discussion.
Overview of this Article
This article provides a comprehensive exploration of strategies to enhance piping systems. Readers will gain insights into optimizing pipe selection, improving installation techniques, implementing robust maintenance schedules, and utilizing advanced technologies for leak detection and predictive maintenance. The value lies in learning practical techniques to reduce operational costs, minimize risks, and increase the lifespan of piping infrastructure. The article will explore the critical connection between proper material selection and overall system longevity, discussing the impact of corrosion and erosion on piping integrity.
Showcase Research and Data-Driven Insights
Studies by organizations like the Pipeline and Hazardous Materials Safety Administration (PHMSA) consistently highlight the significant economic and safety implications of pipeline failures. These failures often result from corrosion, inadequate maintenance, and design flaws. Reports from the American Society of Mechanical Engineers (ASME) emphasize the importance of adhering to strict standards and best practices in piping design and construction to minimize risks. Data consistently shows that proactive maintenance and the implementation of advanced technologies, such as smart sensors and predictive analytics, significantly reduce the likelihood of failures and associated costs.
Key Improvements to Piping Systems: A Summary
Improvement Area | Key Takeaway |
---|---|
Pipe Material Selection | Choosing the right material based on operating conditions is crucial for longevity and preventing corrosion. |
Improved Installation Techniques | Proper installation minimizes stress on pipes, reducing the risk of leaks and premature failure. |
Robust Maintenance Schedules | Regular inspection and maintenance prevent small problems from escalating into costly failures. |
Advanced Leak Detection | Utilizing advanced technologies can significantly reduce downtime caused by leaks. |
Predictive Maintenance | Proactive maintenance based on data analysis helps optimize maintenance schedules and prevent failures. |
Corrosion Prevention Strategies | Implementing corrosion control measures dramatically extends the lifespan of piping systems. |
The Core Discussion: Enhancing Piping System Performance
This section delves into the key aspects of optimizing piping systems.
-
Material Selection: The foundation of a robust piping system lies in selecting the appropriate material. Factors such as operating temperature, pressure, fluid type (corrosive or non-corrosive), and environmental conditions must be carefully considered. Materials like carbon steel, stainless steel, PVC, and HDPE each possess unique properties suitable for specific applications. Failure to choose the correct material can result in rapid degradation, leaks, and system failure.
-
Proper Installation: Correct installation is critical. Improperly installed pipes are susceptible to stress concentrations, leading to leaks and premature failure. This includes ensuring proper pipe support, avoiding sharp bends, and using appropriate joining methods. Following industry standards and best practices during installation significantly reduces the likelihood of future problems.
-
Effective Maintenance: A comprehensive maintenance plan is essential for the longevity of any piping system. This involves regular inspections to identify potential issues early on, cleaning and flushing to remove debris and buildup, and timely repairs or replacements as needed. Implementing a Computerized Maintenance Management System (CMMS) can help streamline maintenance scheduling and improve tracking.
-
Advanced Leak Detection: Advanced technologies, such as acoustic leak detection and smart sensors, can detect leaks early, minimizing downtime and environmental damage. These technologies provide real-time data, allowing for proactive intervention before leaks escalate.
-
Corrosion Management: Corrosion is a major contributor to piping system failures. Implementing effective corrosion control measures, including coatings, cathodic protection, and regular inspections, is crucial for extending the lifespan of the system.
-
Data-Driven Decisions: Collecting and analyzing data from various sources, such as pressure sensors, flow meters, and temperature sensors, can provide valuable insights into system performance. This data-driven approach can help optimize maintenance schedules, improve efficiency, and identify potential issues before they become major problems.
Exploring the Connection Between Corrosion and Piping System Improvement
Corrosion significantly impacts piping system integrity. Its influence on system longevity and operational efficiency cannot be overstated. The type of corrosion (uniform, pitting, galvanic, etc.) dictates the mitigation strategy. For instance, galvanized steel pipes are susceptible to galvanic corrosion, requiring careful consideration of the surrounding materials. Understanding the mechanism of corrosion and its effects is vital for effective prevention. Case studies demonstrate the dramatic cost savings and increased operational reliability achievable through proactive corrosion management. Mitigation strategies involve materials selection (using corrosion-resistant materials), coatings, cathodic protection (applying a protective current), and inhibitors (chemicals that slow down corrosion). Neglecting corrosion control leads to leaks, failures, and costly repairs.
Reinforcing the Corrosion Connection in the Conclusion
The interconnectedness of corrosion and piping system performance is undeniable. Understanding and mitigating corrosion are central to optimizing any piping network. Proactive measures, such as choosing corrosion-resistant materials and implementing protective coatings, significantly extend system lifespan and reduce operational costs. Ignoring this connection leads to expensive repairs, production downtime, and safety hazards. This underscores the need for a holistic approach to piping system management, incorporating corrosion control as a fundamental component.
Diving Deeper into Corrosion
Corrosion is a naturally occurring electrochemical process where a metal reacts with its environment, leading to degradation. Different factors contribute to the rate and type of corrosion, including the material's composition, environmental conditions (temperature, humidity, pH), and the presence of corrosive agents. Case studies frequently show that even small levels of corrosion, if left unchecked, can lead to catastrophic failures over time. A structured approach to corrosion management involves identifying the root causes, selecting appropriate mitigation strategies, and implementing regular inspection and monitoring programs. A well-defined corrosion management plan is key to ensuring the long-term integrity and safety of piping systems.
Frequently Asked Questions (FAQ)
Q1: How often should piping systems be inspected?
A1: Inspection frequency depends on factors like material, operating conditions, and the fluid being transported. However, regular inspections, at least annually, are typically recommended, with more frequent checks for critical systems.
Q2: What are the signs of a failing pipe?
A2: Signs include leaks, corrosion, bulging or swelling, unusual noises, and changes in pressure or flow rate.
Q3: What is the best material for piping systems?
A3: The "best" material depends on the specific application. Factors like operating temperature, pressure, and the corrosive nature of the fluid determine the most suitable choice.
Q4: How can I prevent corrosion in my piping system?
A4: Corrosion prevention involves selecting corrosion-resistant materials, applying protective coatings, implementing cathodic protection, and using corrosion inhibitors.
Q5: What is the cost of repairing a piping system failure?
A5: Repair costs vary dramatically depending on the extent of the damage, location, and the downtime involved. Prevention is far more cost-effective than repair.
Q6: How can I improve the efficiency of my piping system?
A6: Efficiency improvements can be achieved through optimized design, proper installation, regular maintenance, advanced leak detection, and the use of data-driven insights for decision-making.
Actionable Tips to Improve Piping Systems
- Conduct a thorough risk assessment: Identify potential failure points and prioritize areas needing immediate attention.
- Develop a comprehensive maintenance plan: Schedule regular inspections, cleaning, and repairs.
- Implement a CMMS: Use software to track maintenance activities and optimize scheduling.
- Invest in advanced leak detection technologies: Detect leaks early to prevent costly damage.
- Choose corrosion-resistant materials: Select materials suited to the operating conditions.
- Apply protective coatings: Enhance material resistance to corrosion and wear.
- Utilize cathodic protection: Prevent corrosion in susceptible materials.
- Train personnel on proper piping system maintenance: Ensure personnel are competent to handle routine inspections and repairs.
Strong Final Conclusion
Improving piping systems is a multifaceted process involving material selection, installation techniques, maintenance strategies, and the implementation of advanced technologies. This article has highlighted the critical role of corrosion management and the benefits of data-driven decision-making. By proactively addressing these factors, organizations can significantly reduce operational costs, enhance safety, and extend the lifespan of their piping infrastructure. The long-term benefits of a well-maintained and optimized piping system far outweigh the initial investment, contributing significantly to overall operational efficiency and sustainability. Implementing the strategies outlined in this article will lead to a more reliable, safer, and ultimately more profitable operation.
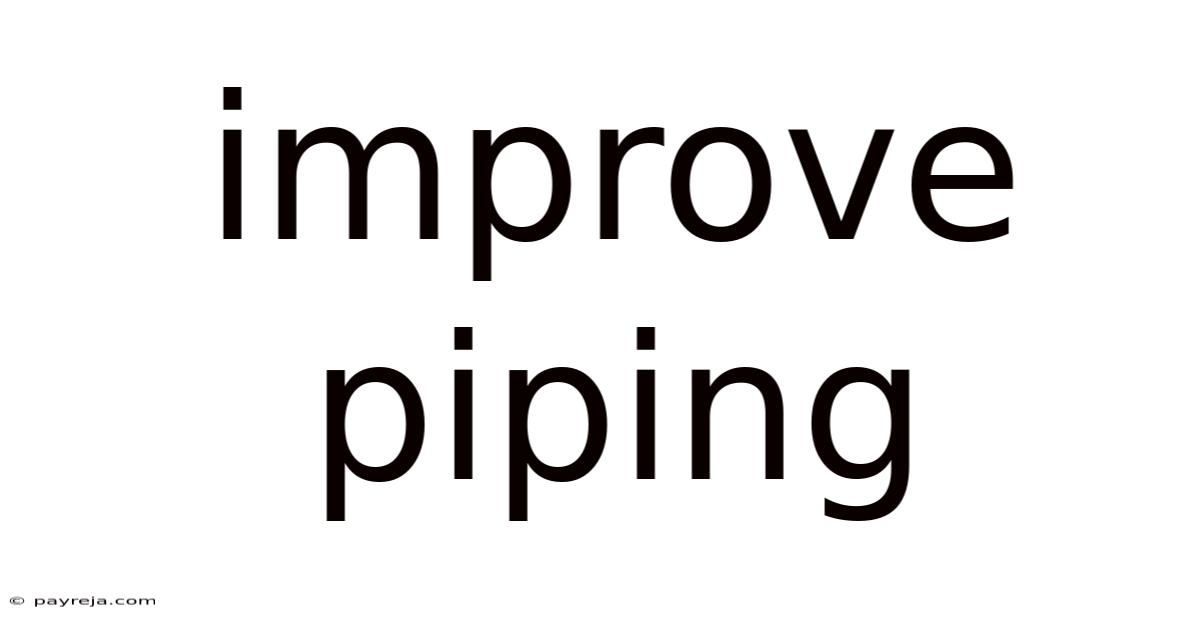
Thank you for visiting our website wich cover about Improve Piping. We hope the information provided has been useful to you. Feel free to contact us if you have any questions or need further assistance. See you next time and dont miss to bookmark.
Also read the following articles
Article Title | Date |
---|---|
Eps Attach Success Rate | Apr 23, 2025 |
Salesforce Database Savepoint | Apr 23, 2025 |
Zoho Crm And Outlook Calendar Integration | Apr 23, 2025 |
Welcome Home Synopsis | Apr 23, 2025 |
Scott Mark | Apr 23, 2025 |