How To Make Cement
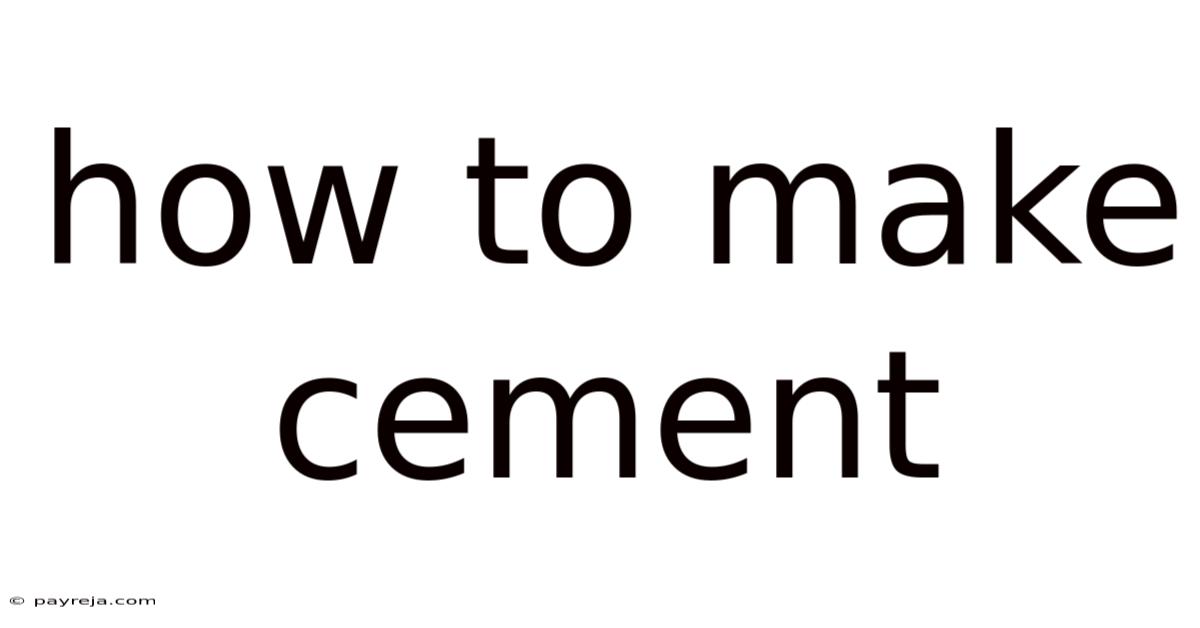
Discover more detailed and exciting information on our website. Click the link below to start your adventure: Visit Best Website meltwatermedia.ca. Don't miss out!
Table of Contents
Unlock Cement's Secrets: A Comprehensive Guide to Manufacturing
What if mastering the art of cement production could revolutionize construction? This fundamental material underpins modern infrastructure, and understanding its creation unlocks vast potential.
Editor’s Note: This article on cement manufacturing has been updated today to reflect the latest industry best practices and technological advancements.
Cement, a ubiquitous construction material, is far more complex than its seemingly simple appearance suggests. Its production is a fascinating blend of chemistry, engineering, and industrial processes. This article delves into the intricacies of cement manufacturing, exploring the raw materials, processes, and considerations involved in creating this essential building block of modern civilization. Understanding cement production not only offers insights into a crucial industry but also highlights opportunities for innovation and sustainability. We will cover the entire process, from sourcing raw materials to the final product, touching upon quality control, environmental concerns, and future trends.
This article will cover the following key topics:
- Raw Material Acquisition and Preparation: Exploring the sourcing and processing of limestone, clay, and other essential components.
- The Cement Kiln Process: A detailed look at the heart of cement production, including the chemical reactions and energy requirements.
- Cooling and Grinding: The final steps that transform the clinker into usable cement.
- Quality Control and Testing: Ensuring consistency and meeting stringent quality standards.
- Environmental Considerations and Sustainability: Examining the industry's environmental impact and ongoing efforts towards greener manufacturing.
- The Future of Cement Production: Exploring innovative techniques and technologies aimed at improving efficiency and sustainability.
Raw Material Acquisition and Preparation
Cement production begins with the careful selection and preparation of raw materials. The primary ingredients are limestone (calcium carbonate) and clay (containing silica, alumina, and iron oxides). The precise proportions of these materials are crucial, as they determine the final properties of the cement. Other minor components, such as gypsum, may be added to regulate setting time.
Limestone is typically quarried, and clay can be sourced from various geological formations. The raw materials undergo rigorous quality control checks to ensure consistency and adherence to precise chemical compositions. This involves analyzing the chemical makeup of the materials to maintain the optimal blend for cement production. Variations in raw material composition can significantly impact the final product's quality, strength, and durability.
Once sourced, the raw materials undergo a process called blending. This often involves crushing and grinding the limestone and clay into a fine powder. Sophisticated techniques, such as X-ray fluorescence (XRF) analysis, are used to monitor the chemical composition throughout the blending process, ensuring uniform consistency. The goal is to create a homogenous mixture with the ideal chemical composition, optimizing the efficiency of the subsequent kiln process. Precise control over the fineness of the raw material blend is crucial; finer blends result in more efficient reactions in the kiln.
The Cement Kiln Process: The Heart of Cement Manufacturing
The heart of cement production lies within the rotary kiln, a long, rotating cylindrical furnace. The blended raw materials are fed into the upper end of the kiln, where they are gradually heated to progressively higher temperatures as they move towards the lower end. This process involves several key stages:
- Preheating Zone: The raw material gradually heats up, driving off moisture and volatile components.
- Calcination Zone: The temperature rises to around 800-900°C, causing the calcium carbonate in the limestone to decompose into calcium oxide (lime) and carbon dioxide.
- Clinkerization Zone: This is the crucial stage where the temperature reaches 1450-1500°C. At this high temperature, a series of complex chemical reactions occur, forming clinker, the primary component of cement. The clinker is composed mainly of four minerals: alite, belite, aluminate, and ferrite. The precise proportions of these minerals are critical to controlling the properties of the final cement.
- Cooling Zone: The clinker is cooled rapidly to prevent unwanted reactions and maintain its desired properties.
The entire kiln process is energy-intensive, primarily relying on fossil fuels like coal or natural gas. However, alternative fuels and energy sources are increasingly being explored to reduce the industry's carbon footprint.
Cooling and Grinding
Once the clinker is cooled, it undergoes grinding to produce the fine cement powder. This process is typically carried out in ball mills, which contain steel balls that grind the clinker into a fine powder. The fineness of the cement powder is a critical factor influencing its properties, particularly its setting time and strength development. Gypsum is added during the grinding process to regulate the setting time of the cement, preventing it from setting too quickly.
Quality Control and Testing
Throughout the entire manufacturing process, rigorous quality control measures are implemented to ensure the cement meets the required specifications. This involves regular testing of the raw materials, the intermediate products, and the final cement. Standard tests assess the cement's fineness, setting time, strength, soundness (resistance to expansion), and other important properties. These tests adhere to established standards such as ASTM (American Society for Testing and Materials) and ISO (International Organization for Standardization).
Environmental Considerations and Sustainability
Cement production has a significant environmental impact, primarily due to its high energy consumption and carbon dioxide emissions from the decomposition of limestone and the combustion of fossil fuels. However, the industry is actively seeking ways to mitigate these impacts. These efforts include:
- Alternative Fuels: Utilizing alternative fuels like biomass, waste-derived fuels, and industrial byproducts to replace fossil fuels.
- Carbon Capture and Storage: Developing technologies to capture and store the carbon dioxide emitted during the process.
- Waste Heat Recovery: Recovering and utilizing waste heat from the kiln to reduce energy consumption.
- Improved Kiln Efficiency: Optimizing kiln operation to improve energy efficiency and reduce emissions.
- Blending with supplementary cementitious materials (SCMs): Incorporating materials like fly ash and slag to reduce clinker content and associated CO2 emissions.
The Future of Cement Production
The future of cement production involves ongoing research and development to improve efficiency and sustainability. This includes exploring innovative processes, such as:
- Dry process modifications: Optimizing dry process techniques for increased energy efficiency.
- Alternative binder materials: Investigating the use of alternative binder materials that have a lower carbon footprint.
- Digitalization and automation: Implementing advanced control systems and automation techniques for improved process efficiency and reduced emissions.
- Circular economy approaches: Exploring ways to integrate cement production into a circular economy by using recycled materials and reducing waste.
Key Takeaways: Understanding Cement Manufacturing
Insight | Description |
---|---|
Raw Material Importance | The precise ratio of limestone and clay is crucial for the final cement properties. |
Kiln Process Complexity | The rotary kiln involves several critical stages, each requiring precise temperature and time control. |
Cooling and Grinding Significance | Proper cooling and grinding are vital for achieving the desired fineness and properties of the cement powder. |
Quality Control is Paramount | Rigorous testing throughout the process ensures the final product meets stringent quality standards. |
Environmental Responsibility | The industry is actively working to reduce its environmental impact through various sustainable practices. |
Innovation Drives the Future | Continuous research and development are pushing for greater efficiency and sustainability in cement production. |
Exploring the Connection Between Energy Consumption and Cement Production
The energy intensity of cement production is a significant environmental concern. The high temperatures required in the kiln process necessitate substantial energy input, typically from fossil fuels. This results in significant greenhouse gas emissions, contributing to climate change.
Roles and Real-World Examples:
- The energy source (coal, natural gas, alternative fuels) directly influences the carbon footprint of cement production. Many cement plants are investing in alternative fuels, such as biomass or waste-derived fuels, to reduce their reliance on fossil fuels.
- The efficiency of the kiln plays a vital role. Modern, well-maintained kilns consume less energy per ton of cement produced. Technological advancements, including improved heat recovery systems, are continually improving efficiency.
Risks and Mitigations:
- High energy costs can impact the profitability of cement production. Hedging strategies, fuel diversification, and improved efficiency can mitigate this risk.
- Greenhouse gas emissions are a major environmental concern. Carbon capture and storage technologies, along with the use of alternative fuels, are crucial mitigation strategies.
Impact and Implications:
- The cost of energy directly affects the price of cement, influencing the overall cost of construction projects.
- The environmental impact of cement production has far-reaching implications for climate change and sustainable development.
Reinforcing the Connection in the Conclusion:
The high energy consumption inherent in cement production is inextricably linked to its environmental impact. While the industry is striving for greater sustainability, reducing energy consumption remains a crucial challenge. The transition to alternative fuels and improved energy efficiency technologies are key to mitigating the environmental footprint of this essential material.
Diving Deeper into Energy Consumption
The energy consumption of cement production can be broken down into several key components:
- Preheating and calcination: Energy is required to heat the raw materials to the temperatures necessary for calcination.
- Clinkerization: This stage, requiring the highest temperatures, consumes the most energy.
- Cooling and grinding: Energy is used to cool the clinker and grind it into fine powder.
The efficiency of each stage influences the overall energy consumption. Modern kilns, employing advanced technologies like precalciners and waste heat recovery systems, significantly improve energy efficiency compared to older designs.
Frequently Asked Questions (FAQ)
-
Q: What are the main raw materials used in cement production?
- A: The primary raw materials are limestone and clay, with minor components like gypsum added to control setting time.
-
Q: How is the quality of cement ensured?
- A: Rigorous quality control measures are employed throughout the process, involving testing of raw materials, intermediate products, and the final cement.
-
Q: What is clinker, and why is it important?
- A: Clinker is the main component of cement, formed through high-temperature reactions in the kiln. Its properties determine the final cement quality.
-
Q: What are the environmental concerns associated with cement production?
- A: The primary concerns are high energy consumption and carbon dioxide emissions.
-
Q: What is being done to make cement production more sustainable?
- A: The industry is actively pursuing alternative fuels, carbon capture technologies, and improved kiln efficiency.
-
Q: What are supplementary cementitious materials (SCMs)?
- A: SCMs are materials like fly ash and slag that can be blended with cement to reduce the amount of clinker needed, lowering the carbon footprint.
Actionable Tips for Understanding Cement Manufacturing
- Research the cement manufacturing plants in your region to learn about their operations and sustainability initiatives.
- Explore the different types of cement and their respective properties.
- Understand the different quality control tests used to ensure cement meets standards.
- Investigate the role of alternative fuels in reducing the environmental impact of cement production.
- Learn about the advancements in kiln technology and their impact on efficiency.
- Stay updated on the latest research and innovations in cement manufacturing.
- Explore the potential of supplementary cementitious materials (SCMs) in sustainable cement production.
Conclusion:
Understanding the complexities of cement manufacturing provides valuable insights into a critical industry. From the careful selection of raw materials to the intricate kiln process and stringent quality control measures, each stage plays a crucial role in creating this fundamental construction material. The ongoing efforts towards sustainability underscore the industry's commitment to reducing its environmental impact. As we look to the future, innovative technologies and sustainable practices will continue to shape the evolution of cement production, ensuring its continued role in building a sustainable future. The journey from raw materials to the finished product highlights the remarkable engineering and chemical processes behind this seemingly simple material, highlighting the continuous quest for efficiency and environmentally responsible practices within the cement industry.
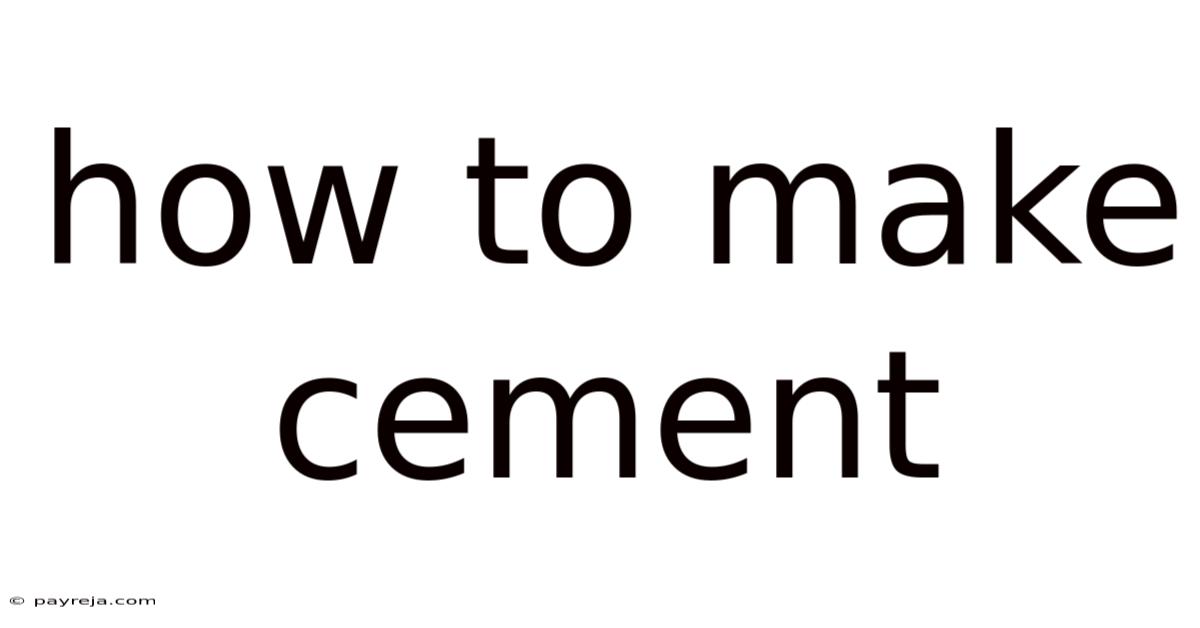
Thank you for visiting our website wich cover about How To Make Cement. We hope the information provided has been useful to you. Feel free to contact us if you have any questions or need further assistance. See you next time and dont miss to bookmark.
Also read the following articles
Article Title | Date |
---|---|
Infinity Siloam | Apr 13, 2025 |
Hcm Vs Crm | Apr 13, 2025 |
Custom Jewelry Ideas | Apr 13, 2025 |
Sbu Student Crm Login | Apr 13, 2025 |
Instantly Crm Integration | Apr 13, 2025 |