How To Check Maintenance Cost In Sap Reports
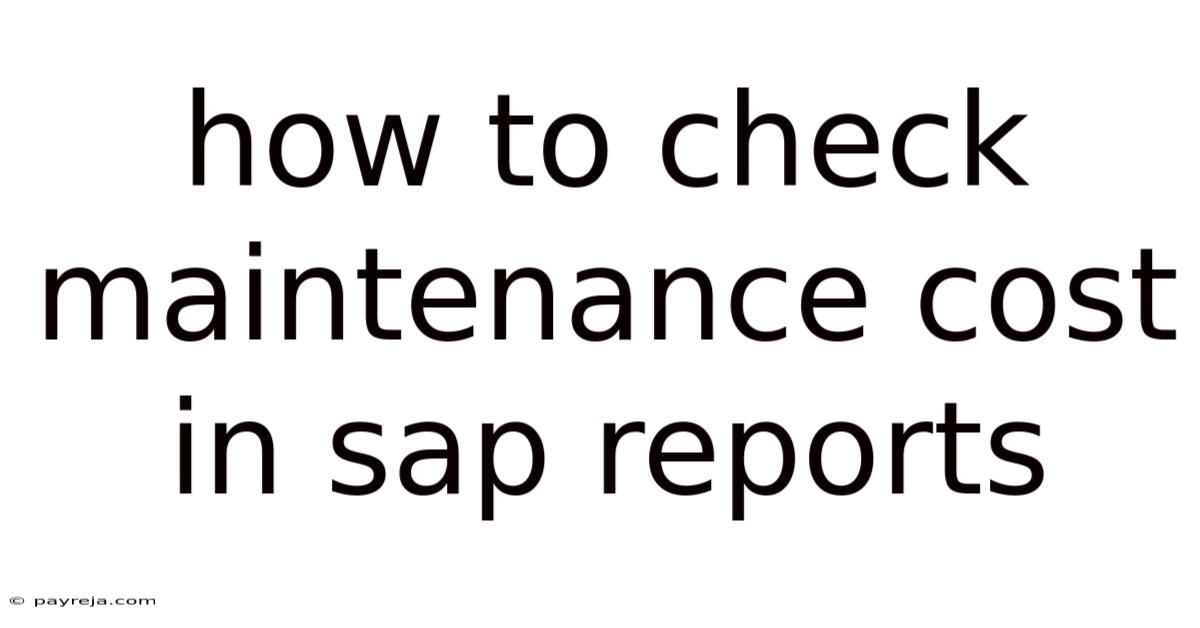
Discover more detailed and exciting information on our website. Click the link below to start your adventure: Visit Best Website meltwatermedia.ca. Don't miss out!
Table of Contents
Unlocking the Secrets of SAP Maintenance Cost Reports: A Comprehensive Guide
What if effortlessly accessing accurate maintenance cost data in SAP could drastically improve your operational efficiency?
Understanding and leveraging SAP's reporting capabilities for maintenance costs is crucial for effective resource allocation and strategic decision-making.
Editor’s Note: This article on how to check maintenance cost in SAP reports has been updated today to reflect the latest SAP functionalities and best practices.
Why Understanding SAP Maintenance Costs Matters
In today's competitive landscape, organizations need granular control over operational expenditures. Maintenance costs, often a significant portion of a company's budget, are no exception. Effective maintenance cost management requires visibility and control. SAP's robust reporting capabilities offer a powerful tool to achieve this. By analyzing maintenance cost data, businesses can identify areas for improvement, optimize resource allocation, predict future expenses, and ultimately, enhance profitability. This is especially important in industries like manufacturing, where equipment downtime directly impacts production and revenue. Accurate cost analysis can inform decisions about preventative maintenance, repairs, and even equipment upgrades, leading to significant long-term savings. The ability to drill down into detailed cost breakdowns enables targeted interventions, maximizing ROI on maintenance activities.
Overview of this Article
This article will explore the various SAP reports and transactions used to analyze maintenance costs. It will cover different reporting strategies, focusing on how to extract relevant data, interpret the results, and leverage this information for better decision-making. Readers will gain a practical understanding of accessing, interpreting, and utilizing maintenance cost data within the SAP environment. The guide includes examples, best practices, and a troubleshooting section to address common challenges encountered when working with SAP maintenance cost reports.
Accessing and Interpreting Key SAP Maintenance Cost Reports
SAP offers a multitude of reports and transactions designed to analyze maintenance costs. The specific reports utilized will depend on the SAP module (e.g., Plant Maintenance (PM), Production Planning (PP)) and the desired level of detail. A structured approach is essential to navigate this complexity effectively. This often involves a combination of standard SAP reports and custom reports developed to meet specific organizational needs.
1. Transaction Codes and Reports:
- KO88 (Actual Costing for Orders): This transaction provides a detailed breakdown of actual costs incurred for specific maintenance orders. Users can filter by order number, period, cost element, and other criteria to pinpoint cost variances and identify areas of concern.
- KK03 (Display Cost Center): This displays cost center accounting data, allowing analysis of maintenance costs allocated to specific cost centers. The ability to view actual versus planned costs is crucial for variance analysis.
- KS03 (Display Profit Center): Similar to KK03, but focuses on profit centers, providing a broader perspective on maintenance costs' contribution to profitability.
- S_ALR_87012278 (Maintenance Order Actual Costs): This standard report provides an overview of actual maintenance costs, often used for high-level analysis and reporting to management. It allows filtering by various criteria, offering flexibility in the data analysis process.
- Custom Reports: Many organizations develop custom reports to meet their unique needs. These reports often integrate data from multiple sources to provide comprehensive, tailored insights. The design of these reports is crucial to ensure data accuracy and relevance.
2. Data Extraction and Analysis:
Data extraction can be performed directly through the transactions listed above, or using tools like SAP BW (Business Warehouse) for more advanced analytics and reporting. Data interpretation involves comparing actual costs against planned costs, identifying significant variances, and analyzing trends over time. Understanding the cost drivers and factors influencing maintenance costs is paramount for effective decision-making.
3. Key Performance Indicators (KPIs):
Several KPIs can be derived from maintenance cost data in SAP, providing valuable insights into operational efficiency. These include:
- Maintenance Cost per Unit of Production: Relates maintenance costs to the output generated, providing a measure of maintenance efficiency.
- Mean Time Between Failures (MTBF): Indicates the average time between equipment failures, reflecting the effectiveness of preventative maintenance strategies.
- Mean Time To Repair (MTTR): Measures the average time taken to repair equipment failures, highlighting areas for improvement in repair processes.
- Maintenance Cost as a Percentage of Revenue: Provides a high-level view of the overall impact of maintenance costs on profitability.
Key Insights from SAP Maintenance Cost Reporting
Insight | Description | Actionable Implications |
---|---|---|
Cost Overruns | Identification of maintenance orders exceeding budgeted costs. | Investigation of causes, optimization of maintenance processes, improved budget planning. |
Trend Analysis | Tracking maintenance costs over time to identify patterns and predict future expenses. | Proactive planning for maintenance activities, optimized resource allocation. |
Inefficient Equipment | Pinpointing equipment with disproportionately high maintenance costs. | Evaluation of equipment replacement or upgrade, improved maintenance strategies. |
Material Cost Analysis | Detailed breakdown of material costs associated with maintenance activities. | Negotiation of better material prices, optimization of inventory management. |
Labor Cost Analysis | Analysis of labor costs associated with maintenance activities. | Improved workforce scheduling, training programs, process optimization. |
The Connection Between Preventative Maintenance and SAP Maintenance Cost Reports
Preventative maintenance plays a crucial role in controlling maintenance costs. By using SAP PM module, organizations can schedule regular maintenance activities, reducing the likelihood of unexpected breakdowns and costly emergency repairs. The integration of preventative maintenance schedules with SAP's reporting tools provides a powerful mechanism for tracking the effectiveness of preventative maintenance strategies and quantifying their cost-saving benefits. Reports can demonstrate the return on investment (ROI) of preventative maintenance programs, justifying investment in these programs to management.
Roles and Real-World Examples:
- Maintenance Managers: Use SAP reports to monitor maintenance costs, identify problem areas, and optimize resource allocation.
- Plant Managers: Leverage reports to assess the overall impact of maintenance costs on production efficiency and profitability.
- Financial Controllers: Utilize SAP reports for budgeting, forecasting, and variance analysis.
Example: A manufacturing plant uses SAP reports to analyze the maintenance costs of its assembly line. By identifying a particular machine with consistently high maintenance costs, they decide to invest in a more robust and reliable model, resulting in significant long-term cost savings.
Risks and Mitigations:
- Data Inaccuracy: Ensuring data accuracy is crucial. This involves regular data validation and reconciliation processes.
- Reporting Delays: Timely reporting is vital for effective decision-making. Implementing efficient data processing and reporting mechanisms is essential.
- Lack of User Training: Proper training for users is needed to ensure effective utilization of SAP reporting capabilities.
Impact and Implications:
Effective maintenance cost management using SAP reports can lead to significant improvements in operational efficiency, reduced downtime, improved equipment reliability, and enhanced profitability. It can inform strategic decisions about investments in equipment upgrades and maintenance strategies, leading to long-term cost savings.
Diving Deeper into Preventative Maintenance Strategies
Preventative maintenance (PM) is crucial for minimizing unplanned downtime and reducing long-term maintenance costs. Effective PM involves a planned approach to maintaining equipment, ensuring regular inspections, servicing, and repairs, preventing major failures. Through regular inspections and preventative maintenance, businesses can avoid expensive emergency repairs, prolong equipment lifespan, and ensure consistent production output. Analyzing PM data in SAP reports provides critical insights into the effectiveness of PM strategies and their cost-saving benefits.
Preventative Maintenance Activity | SAP Data Source | Cost Impact |
---|---|---|
Regular Inspections | PM Orders, Notifications | Early detection of potential problems, preventing costly repairs. |
Lubrication and Cleaning | PM Orders | Reduced wear and tear, extended equipment lifespan. |
Parts Replacement | Material Master, PM Orders | Proactive replacement of worn-out components, preventing failures. |
Calibration and Testing | PM Orders | Ensuring equipment accuracy and reliability. |
Frequently Asked Questions (FAQ)
Q1: What if I don't have access to specific SAP transactions?
A1: Contact your SAP administrator or IT support team to request the necessary authorizations.
Q2: How can I improve the accuracy of my maintenance cost data?
A2: Ensure accurate data entry, regularly reconcile data with actual costs, and conduct periodic data audits.
Q3: How can I create custom reports tailored to my specific needs?
A3: Engage with your SAP development team or an external consultant to create custom reports that meet your unique requirements.
Q4: What are the best practices for analyzing maintenance cost reports?
A4: Compare actual costs to planned costs, analyze trends over time, identify significant variances, and drill down into detailed cost breakdowns.
Q5: How can I integrate maintenance cost data with other business systems?
A5: Utilize SAP's integration capabilities to connect maintenance cost data with other systems, such as financial accounting and production planning.
Q6: How can I effectively communicate maintenance cost insights to management?
A6: Present data in a clear, concise, and easily understandable format, using charts, graphs, and key performance indicators.
Actionable Tips for Optimizing Maintenance Cost Management in SAP
- Regularly review and analyze maintenance cost reports: Make this a routine process to identify trends and potential issues early.
- Implement a robust preventative maintenance program: Schedule regular maintenance activities to prevent costly breakdowns.
- Optimize your spare parts inventory: Maintain an adequate supply of spare parts to minimize downtime during repairs.
- Invest in employee training: Ensure your maintenance team has the skills and knowledge to perform efficient repairs.
- Utilize SAP's reporting capabilities: Leverage SAP's reporting tools to gain a clear understanding of your maintenance costs and identify areas for improvement.
- Collaborate with other departments: Work closely with production, finance, and purchasing to optimize maintenance processes.
- Benchmark your maintenance costs: Compare your costs to industry benchmarks to identify opportunities for improvement.
- Regularly update your maintenance plans: Adjust your maintenance plans based on the analysis of your maintenance cost reports and operational feedback.
Conclusion
Effective maintenance cost management is critical for optimizing operational efficiency and enhancing profitability. SAP's powerful reporting tools provide the visibility and control needed to achieve this. By understanding the various SAP reports and transactions, and applying the strategies outlined in this article, organizations can effectively analyze maintenance costs, identify areas for improvement, and make data-driven decisions to optimize their maintenance strategies. Through a proactive approach and the effective utilization of SAP's capabilities, organizations can significantly reduce maintenance expenses, minimize downtime, and enhance overall operational performance. The ongoing monitoring and analysis of maintenance costs, coupled with continuous improvement initiatives, will ultimately contribute to significant cost savings and improved operational excellence.
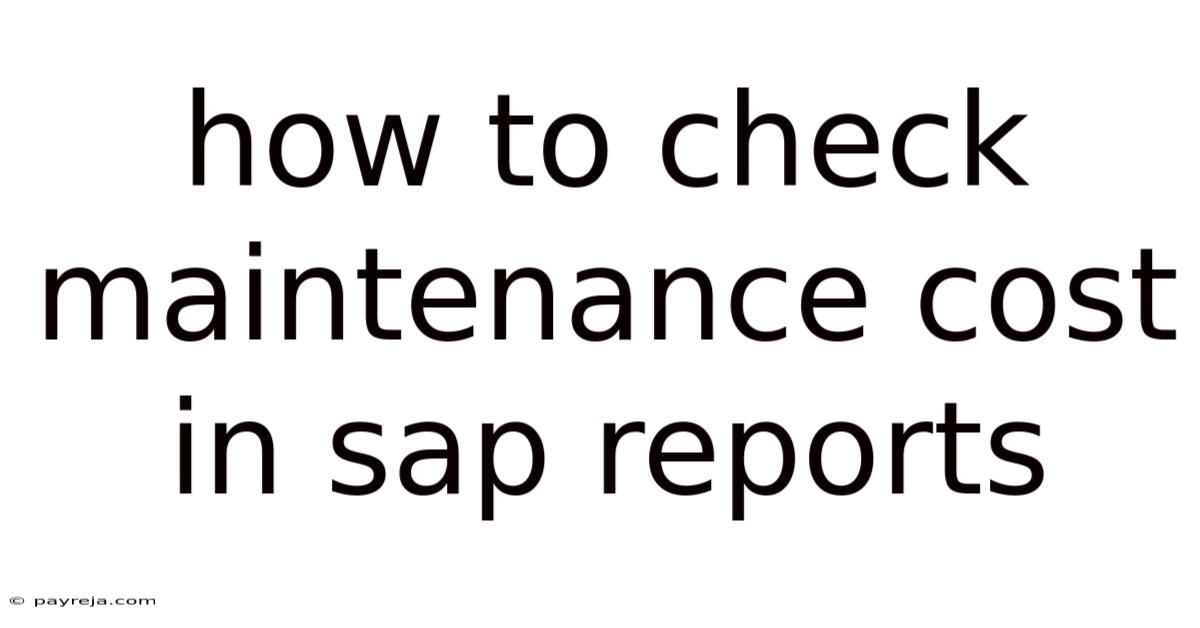
Thank you for visiting our website wich cover about How To Check Maintenance Cost In Sap Reports. We hope the information provided has been useful to you. Feel free to contact us if you have any questions or need further assistance. See you next time and dont miss to bookmark.
Also read the following articles
Article Title | Date |
---|---|
Higher Ed Erp Systems | Apr 17, 2025 |
Is Quickbooks Online An Erp System | Apr 17, 2025 |
How To Create A Post Like Sap Technology Influencer | Apr 17, 2025 |
Microsoft Erp Navision | Apr 17, 2025 |
Erp System For Construction Company | Apr 17, 2025 |