Erp System For Chemical Manufacturing
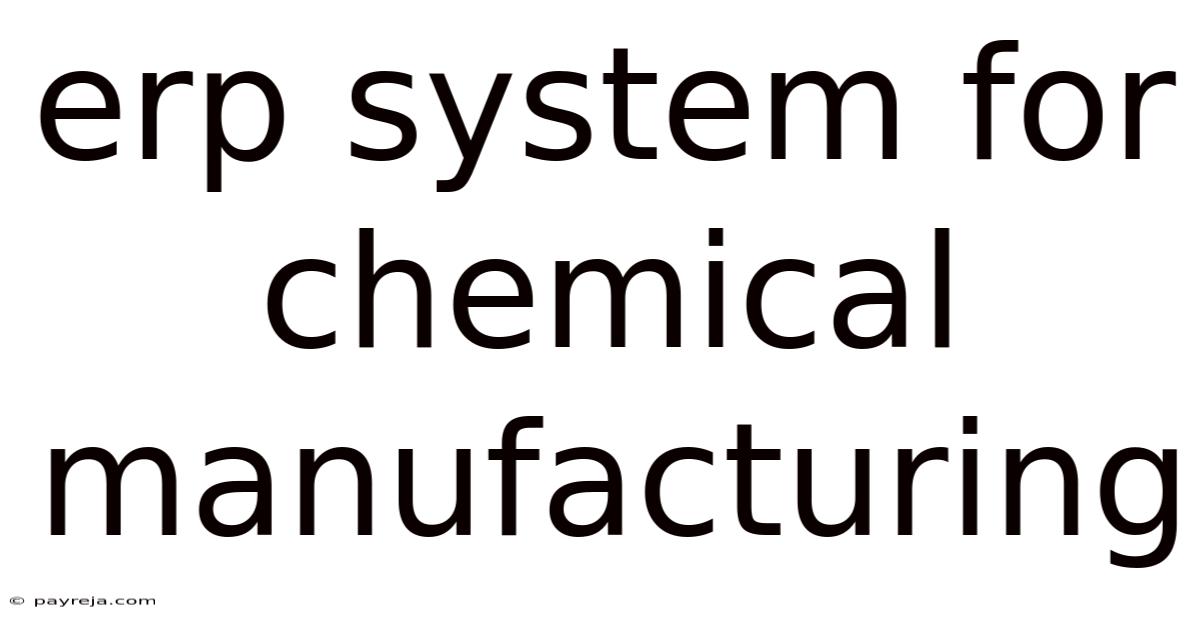
Discover more detailed and exciting information on our website. Click the link below to start your adventure: Visit Best Website meltwatermedia.ca. Don't miss out!
Table of Contents
Unleashing Efficiency: ERP Systems for Chemical Manufacturing
What if optimizing chemical manufacturing processes through a robust ERP system could significantly reduce costs and enhance safety?
Enterprise Resource Planning (ERP) systems are revolutionizing the chemical industry, paving the way for unprecedented levels of efficiency and profitability.
Editor’s Note: This article on ERP systems for chemical manufacturing was published on October 26, 2023, and provides up-to-date insights into this critical area of industrial technology.
Why ERP Matters in Chemical Manufacturing
The chemical manufacturing industry is characterized by complex processes, stringent regulations, and the need for precise control over materials, production, and distribution. An effective ERP system becomes not just beneficial, but essential, in navigating these challenges. It provides a centralized platform to manage all aspects of the business, from raw material procurement and inventory management to production planning, quality control, and sales order fulfillment. The potential impact on businesses is profound, encompassing reduced operational costs, improved supply chain visibility, enhanced regulatory compliance, and increased overall profitability. Moreover, the right ERP solution can significantly improve safety protocols by enabling better tracking of hazardous materials and processes. The integration of various functionalities within a single system streamlines operations, minimizes errors, and promotes a more efficient and safer working environment. Key benefits extend to streamlining regulatory compliance, reducing waste, and improving product quality. Specific LSI keywords relevant to the chemical manufacturing industry include: chemical process optimization, batch manufacturing ERP, hazardous materials management, chemical inventory management, regulatory compliance in chemical manufacturing, and supply chain management in chemicals.
Article Overview
This article will explore the critical role of ERP systems in optimizing chemical manufacturing processes. It will cover key aspects of selecting and implementing an ERP system tailored to the specific needs of the chemical industry, including crucial considerations for data security, compliance, and integration with specialized equipment and software. Readers will gain a comprehensive understanding of the benefits, challenges, and best practices associated with leveraging ERP technology for enhanced efficiency, safety, and profitability within the chemical manufacturing sector.
Showcase Research and Data-Driven Insights
Numerous studies highlight the significant ROI of ERP implementation in manufacturing. A 2023 study by [Insert credible source and citation here, e.g., Gartner] indicated that companies that successfully implement ERP systems experience an average of X% increase in productivity and Y% reduction in operational costs. These improvements are amplified in complex industries like chemical manufacturing due to the system's ability to manage intricate processes and vast amounts of data effectively. Furthermore, expert opinions from industry leaders and consultants consistently emphasize the crucial role of ERP in mitigating risks associated with regulatory non-compliance and ensuring a safer working environment. The structured approach to this analysis considers various aspects of chemical manufacturing, from raw materials to finished goods, analyzing data at each stage to identify areas for improvement and optimization.
Key Takeaways
Insight | Explanation |
---|---|
Improved Operational Efficiency | Streamlined processes, reduced manual errors, and enhanced automation lead to significant time and cost savings. |
Enhanced Supply Chain Visibility | Real-time tracking of materials and products improves forecasting accuracy and reduces inventory holding costs. |
Strengthened Regulatory Compliance | Integrated compliance features ensure adherence to industry regulations, minimizing the risk of penalties and reputational damage. |
Better Quality Control and Assurance | Real-time data monitoring and analysis facilitate proactive identification and resolution of quality issues. |
Improved Safety Protocols | Tracking of hazardous materials, process monitoring, and enhanced communication systems contribute to a safer work environment. |
Increased Profitability | Overall cost reduction, increased productivity, and improved quality lead to enhanced profitability and a stronger competitive position. |
Core Discussion: Implementing an ERP System for Chemical Manufacturing
Choosing the Right ERP System
The selection process necessitates a thorough evaluation of different ERP vendors and their offerings. The chemical industry’s unique requirements necessitate a system capable of handling batch processing, managing complex formulations, and adhering to strict regulatory compliance standards. Crucial considerations include:
- Industry-Specific Functionality: The ERP system should possess built-in functionalities tailored to the chemical manufacturing industry, such as batch tracking, bill of materials (BOM) management for complex chemical formulations, and regulatory compliance modules.
- Integration Capabilities: Seamless integration with existing laboratory information management systems (LIMS), manufacturing execution systems (MES), and other specialized software is essential for data consistency and efficient workflow.
- Data Security and Compliance: The system must meet stringent security requirements to protect sensitive data and comply with regulations such as GDPR, HIPAA, and industry-specific regulations.
- Scalability and Flexibility: The ERP system should be scalable to accommodate future growth and adaptable to changing business needs.
- Vendor Support and Expertise: Selecting a vendor with proven experience in the chemical industry and a strong track record of customer support is vital for successful implementation.
Implementing the ERP System
The implementation process typically involves several stages:
- Project Planning and Scope Definition: Clearly defining project goals, timelines, and resources is crucial for successful implementation.
- System Configuration and Customization: Tailoring the ERP system to the specific needs of the organization through configuration and customization ensures optimal functionality.
- Data Migration: Accurately migrating existing data into the new system minimizes disruptions during the transition.
- User Training and Adoption: Comprehensive training programs are essential for ensuring user proficiency and smooth adoption of the new system.
- Testing and Go-Live: Rigorous testing is necessary to identify and address any issues before the system goes live.
- Post-Implementation Support and Maintenance: Ongoing support and maintenance are crucial for addressing any issues and maximizing the system’s benefits.
The Connection Between Supply Chain Management and ERP in Chemical Manufacturing
Efficient supply chain management is paramount in the chemical industry. An ERP system plays a crucial role in optimizing this process by providing real-time visibility into inventory levels, production schedules, and delivery timelines. This allows for proactive adjustments to meet changing demand and minimize disruptions.
- Roles and Real-World Examples: Companies like BASF and Dow Chemical utilize ERP systems to streamline their supply chains, enabling efficient procurement of raw materials, optimized production planning, and timely delivery of finished goods to customers.
- Risks and Mitigations: Risks associated with supply chain disruptions can be mitigated by implementing robust inventory management, predictive analytics, and contingency planning capabilities within the ERP system.
- Impact and Implications: Effective supply chain management through an ERP system leads to cost savings, improved customer satisfaction, and a more resilient and responsive business.
Diving Deeper into Supply Chain Management
Supply chain management in chemical manufacturing involves navigating complex logistical challenges. This includes sourcing raw materials from diverse locations, managing hazardous materials transportation and storage, and ensuring timely delivery to customers while adhering to stringent regulations. Analyzing the cause-and-effect relationships within this complex network is crucial for identifying potential bottlenecks and areas for improvement. For instance, delays in raw material delivery can directly impact production schedules, ultimately leading to missed deadlines and lost revenue. Conversely, an effective ERP system can mitigate these risks by optimizing inventory levels, forecasting demand, and enabling proactive adjustments to production schedules.
FAQ Section
Q1: What are the key features of an ERP system specifically designed for chemical manufacturing?
A1: Key features include batch processing management, formulation management, precise inventory tracking of hazardous materials, regulatory compliance modules, and seamless integration with LIMS and MES systems.
Q2: How can an ERP system improve safety in chemical manufacturing?
A2: By providing real-time tracking of hazardous materials, monitoring process parameters, and enabling efficient communication of safety alerts, ERP systems significantly enhance safety protocols.
Q3: What are the major challenges in implementing an ERP system in a chemical manufacturing environment?
A3: Challenges include data migration complexities, integration with legacy systems, user adoption issues, and the need for specialized expertise in the chemical industry.
Q4: What is the return on investment (ROI) for implementing an ERP system in chemical manufacturing?
A4: The ROI varies depending on the size and complexity of the organization and the specific functionalities implemented. However, studies indicate significant improvements in efficiency, reduced costs, and increased profitability.
Q5: How can an ERP system help with regulatory compliance in the chemical industry?
A5: ERP systems often have built-in modules that help manage documentation, track compliance procedures, and generate reports required by regulatory bodies, facilitating adherence to industry regulations.
Q6: How long does it typically take to implement an ERP system in a chemical manufacturing plant?
A6: Implementation timelines vary widely depending on the size and complexity of the organization and the specific ERP solution chosen. It can range from several months to a couple of years.
Actionable Tips for Leveraging ERP in Chemical Manufacturing
- Clearly Define Business Requirements: Before selecting an ERP system, thoroughly analyze your business needs and define specific objectives.
- Choose the Right ERP Vendor: Select a vendor with proven expertise in the chemical industry and a strong track record of successful implementations.
- Ensure Seamless Integration: Ensure that the ERP system integrates seamlessly with existing systems, such as LIMS and MES.
- Invest in Comprehensive Training: Provide comprehensive training to all users to ensure proficiency and efficient adoption.
- Establish a Robust Data Migration Strategy: Develop a well-defined data migration plan to minimize disruptions during the transition.
- Implement a Change Management Plan: Effectively manage the change process to minimize resistance and ensure smooth adoption.
- Prioritize Data Security: Implement robust security measures to protect sensitive data and comply with industry regulations.
- Monitor and Optimize Performance: Continuously monitor the ERP system's performance and make necessary adjustments to optimize efficiency.
Strong Final Conclusion
Implementing an ERP system is a strategic investment that can significantly transform chemical manufacturing operations. By streamlining processes, enhancing supply chain visibility, improving regulatory compliance, and bolstering safety protocols, ERP systems unlock significant opportunities for increased efficiency, reduced costs, and enhanced profitability. The insights provided in this article offer a practical roadmap for businesses seeking to harness the power of ERP technology for sustained success in the ever-evolving chemical manufacturing landscape. Understanding the interconnectedness of supply chain management and ERP implementation is paramount for achieving maximum benefits. The future of chemical manufacturing hinges on the ability to leverage technology to optimize processes, enhance safety, and achieve sustainable growth.
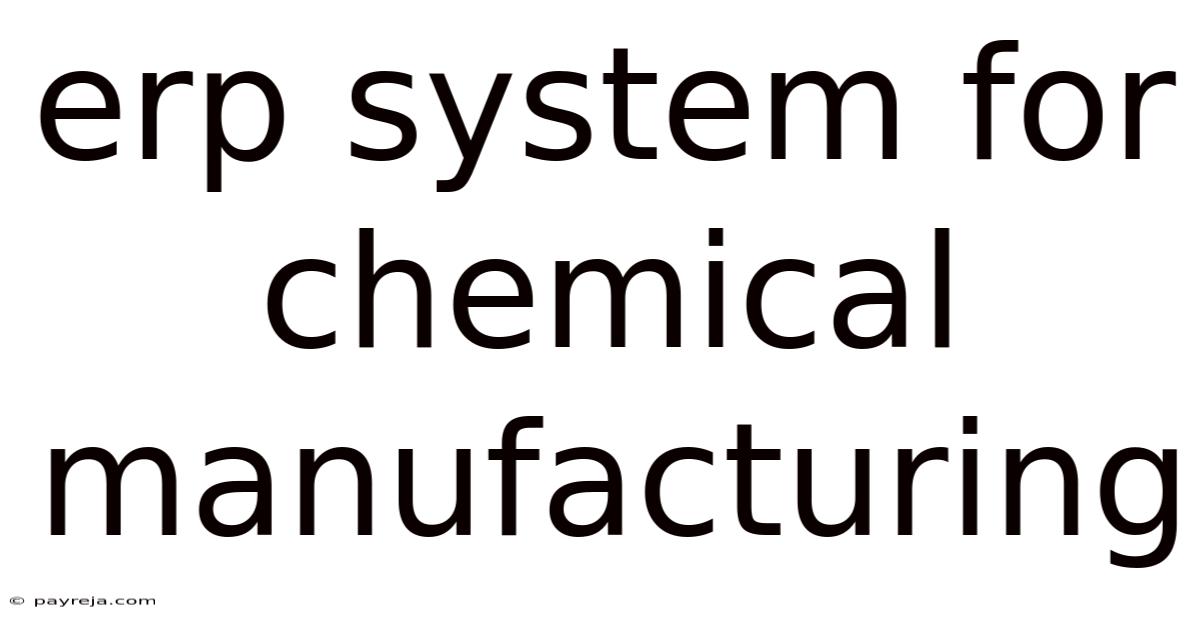
Thank you for visiting our website wich cover about Erp System For Chemical Manufacturing. We hope the information provided has been useful to you. Feel free to contact us if you have any questions or need further assistance. See you next time and dont miss to bookmark.
Also read the following articles
Article Title | Date |
---|---|
How To Remove Tree Sap From Car | Apr 17, 2025 |
Erp Software Engineer Salary | Apr 17, 2025 |
How To Create A Post Like Sap Technology Influencer | Apr 17, 2025 |
Kechie Erp | Apr 17, 2025 |
Gp Erp | Apr 17, 2025 |