Erp Software For Process Manufacturing
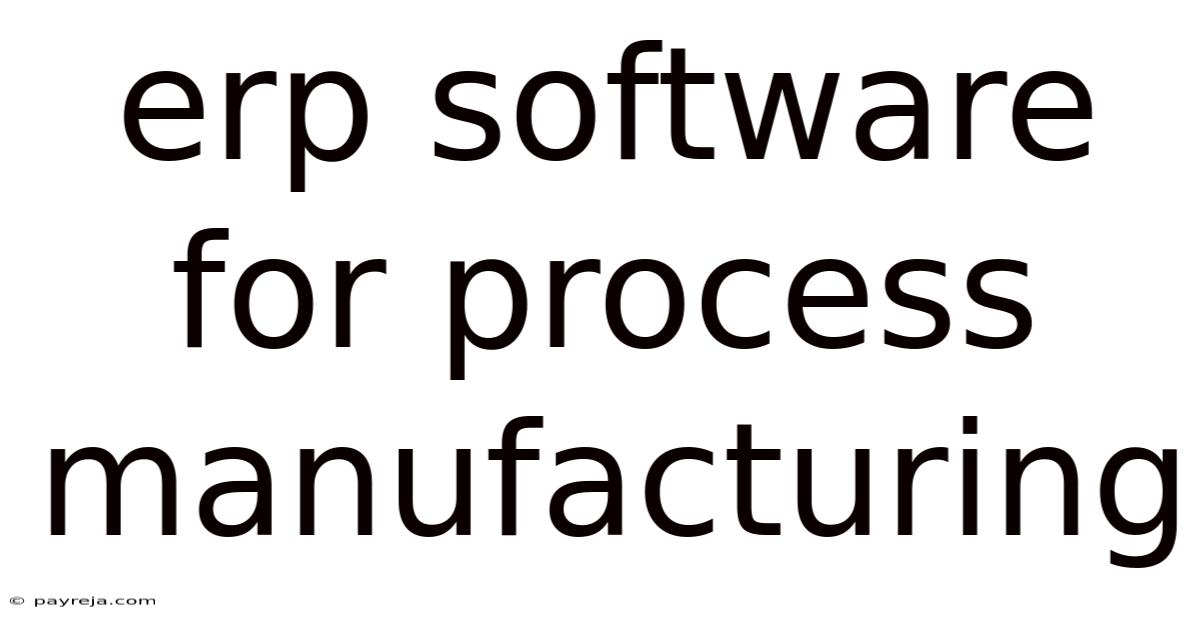
Discover more detailed and exciting information on our website. Click the link below to start your adventure: Visit Best Website meltwatermedia.ca. Don't miss out!
Table of Contents
Unlocking Efficiency: A Deep Dive into ERP Software for Process Manufacturing
What if optimizing your process manufacturing with the right ERP could dramatically reduce costs and boost productivity?
ERP software is no longer a luxury; it's a necessity for thriving in today's competitive process manufacturing landscape.
Editor’s Note: This article on ERP software for process manufacturing was published today, offering the latest insights and best practices in this rapidly evolving field.
Why ERP Matters in Process Manufacturing
Process manufacturing, encompassing industries like food and beverage, pharmaceuticals, chemicals, and cosmetics, faces unique challenges. Maintaining precise control over complex formulas, managing intricate production processes, adhering to stringent regulatory compliance, and optimizing inventory across multiple stages are critical for success. Enterprise Resource Planning (ERP) software provides a centralized system to address these challenges, streamlining operations and driving significant improvements across the entire value chain. Effective ERP solutions integrate various departments—from procurement and production to quality control and sales—into a unified platform, fostering collaboration and enhancing visibility. This improved visibility allows for better decision-making, reduced waste, and increased overall efficiency, directly impacting profitability and market competitiveness. The ability to track materials, manage formulations precisely, and maintain comprehensive quality control records is paramount in regulated industries, making ERP a critical investment for compliance and risk mitigation.
Article Overview
This article explores the essential aspects of ERP software tailored for process manufacturing. It will cover key functionalities, implementation strategies, considerations for choosing the right system, and the relationship between ERP and other crucial technologies. Readers will gain a comprehensive understanding of how ERP can transform their operations, improve efficiency, and ultimately drive business growth. The article will also delve into the crucial connection between effective quality management systems (QMS) and a robust ERP system.
Research and Data-Driven Insights
Numerous studies highlight the significant ROI associated with implementing ERP systems in manufacturing. A recent report by [Insert credible source, e.g., Gartner, IDC] indicated that companies using advanced ERP systems experience an average [Insert percentage]% increase in productivity and a [Insert percentage]% reduction in operational costs. This improvement is largely attributed to better inventory management, reduced production downtime, and enhanced supply chain visibility. The structured approach used in this article draws on industry best practices, case studies, and expert opinions to present clear, actionable insights.
Key Takeaways: Essential Insights for Process Manufacturers
Insight | Explanation |
---|---|
Improved Production Planning & Scheduling | Real-time visibility allows for optimized scheduling, minimizing downtime and maximizing output. |
Enhanced Inventory Management | Precise tracking of raw materials, work-in-progress, and finished goods minimizes waste and prevents stockouts. |
Streamlined Quality Control & Compliance | Integrated QMS functionality ensures adherence to regulatory requirements and maintains high product quality. |
Better Supply Chain Collaboration | Improved communication and information sharing with suppliers and distributors enhances efficiency and responsiveness. |
Data-Driven Decision Making | Access to real-time data facilitates informed decision-making across all departments, leading to better strategies and improved operational efficiency. |
Reduced Operational Costs | Optimized processes, reduced waste, and improved efficiency contribute to significant cost savings. |
Core Discussion: Essential Features of ERP for Process Manufacturing
The core functionality of ERP software in process manufacturing differs slightly from discrete manufacturing ERP. Here’s a breakdown of key aspects:
1. Formula and Recipe Management: This capability is crucial for process manufacturing. ERP systems allow for the precise definition, management, and version control of product formulas. Changes to formulas are easily tracked, ensuring consistency and compliance.
2. Batch Tracking and Traceability: Maintaining a complete record of each batch, including ingredients, production parameters, and quality test results, is essential for traceability and compliance. ERP systems facilitate this by integrating with production equipment and quality control instruments.
3. Bill of Materials (BOM) Management: Accurate BOMs are critical for process manufacturing, listing all raw materials and their quantities needed for each product. ERP systems manage BOMs effectively, allowing for easy updates and revisions.
4. Quality Management System (QMS) Integration: Seamless integration with a QMS ensures adherence to quality standards and regulatory compliance. This allows for the tracking of quality metrics, non-conformances, and corrective actions.
5. Production Planning and Scheduling: ERP systems optimize production schedules based on demand forecasts, available resources, and production capacity. This minimizes downtime and maximizes efficiency.
6. Inventory Control and Management: Precise inventory management is vital in process manufacturing to avoid stockouts and minimize waste. ERP systems offer real-time inventory visibility, facilitating better planning and procurement.
The Interplay Between QMS and ERP
The connection between a robust QMS and a well-implemented ERP is critical for success in process manufacturing. An integrated approach allows for automated quality checks at various stages of production, reduces manual data entry, and improves overall efficiency. Real-time data from the production floor can be fed directly into the QMS, allowing for immediate identification and resolution of quality issues. This integrated approach minimizes errors, improves product quality, and streamlines regulatory compliance processes. The ability to quickly trace a product back to its raw materials and production process is crucial for recalls and investigations.
Connecting Quality Management (QMS) and ERP
The relationship between QMS and ERP is symbiotic. A powerful ERP system feeds data (batch numbers, production dates, raw material usage, etc.) into the QMS, providing a comprehensive audit trail for quality control. Conversely, the QMS provides real-time feedback to the ERP, flagging potential quality issues and allowing for proactive adjustments to the production process. This bidirectional data flow minimizes production delays and improves overall efficiency. Companies with integrated QMS and ERP systems often have a significant competitive advantage, particularly in highly regulated industries.
Exploring the Connection Between Data Analytics and ERP
Data analytics plays a crucial role in leveraging the full potential of ERP in process manufacturing. The wealth of data captured by the ERP system can be used to identify trends, optimize processes, and improve decision-making. This might include identifying bottlenecks in production, predicting equipment failures, and optimizing inventory levels. Advanced analytics techniques such as predictive modeling and machine learning can be applied to the data to gain deeper insights and improve operational efficiency further. By analyzing production data, companies can identify areas for improvement, reducing waste and enhancing profitability.
Dive Deeper into Data Analytics
Data analytics in process manufacturing goes beyond simple reporting. It involves using sophisticated techniques to extract actionable insights. This includes:
- Predictive Maintenance: Analyzing equipment performance data to predict potential failures and schedule maintenance proactively, minimizing downtime.
- Process Optimization: Identifying bottlenecks and inefficiencies in the production process and making data-driven improvements.
- Supply Chain Optimization: Analyzing supplier performance and lead times to optimize procurement strategies and minimize disruptions.
- Demand Forecasting: Utilizing historical data and market trends to predict future demand, allowing for better production planning.
Frequently Asked Questions (FAQ)
Q1: What is the average cost of implementing an ERP system for process manufacturing? A1: The cost varies significantly depending on the size of the company, the chosen ERP solution, and the level of customization required. Expect a range from tens of thousands to millions of dollars.
Q2: How long does it typically take to implement an ERP system? A2: Implementation timeframes vary, but a realistic estimate is between 6 months and 2 years, depending on the complexity of the project and the company's internal resources.
Q3: What are the key challenges in ERP implementation? A3: Challenges include data migration, user adoption, integration with existing systems, and managing change within the organization.
Q4: How can I ensure a successful ERP implementation? A4: Careful planning, selecting the right vendor, providing adequate training to employees, and obtaining executive sponsorship are crucial for success.
Q5: What are the key metrics to track after ERP implementation? A5: Key metrics include production efficiency, inventory turnover, on-time delivery, order fulfillment rates, and overall operational costs.
Q6: Can existing systems be integrated with a new ERP? A6: Yes, many ERP systems offer robust integration capabilities, allowing for the seamless integration of existing legacy systems.
Actionable Tips for Implementing ERP in Process Manufacturing
- Clearly define your business goals: Identify the specific problems you want the ERP to solve.
- Choose the right ERP vendor: Select a vendor with experience in process manufacturing and a good track record.
- Develop a detailed implementation plan: Outline the steps involved, timelines, and responsibilities.
- Provide adequate training to employees: Ensure that users are adequately trained on the new system.
- Establish clear communication channels: Maintain open communication between the implementation team and stakeholders.
- Test thoroughly before go-live: Conduct comprehensive testing to identify and resolve any issues before launching the system.
- Monitor and optimize post-implementation: Continuously monitor the system's performance and make adjustments as needed.
- Invest in ongoing support and maintenance: Ensure that you have access to ongoing support and maintenance from your vendor.
Conclusion
ERP software is a transformative tool for process manufacturers, offering significant improvements in efficiency, compliance, and profitability. By understanding the key features, implementation strategies, and the relationship with other critical technologies such as QMS and data analytics, process manufacturers can leverage the full potential of ERP to achieve significant operational gains and a competitive edge. The future of process manufacturing is inextricably linked to the adoption and effective utilization of advanced ERP solutions, driving innovation and growth in this dynamic industry. Investing in the right ERP system is not just an expense; it's a strategic investment in the future of your business.
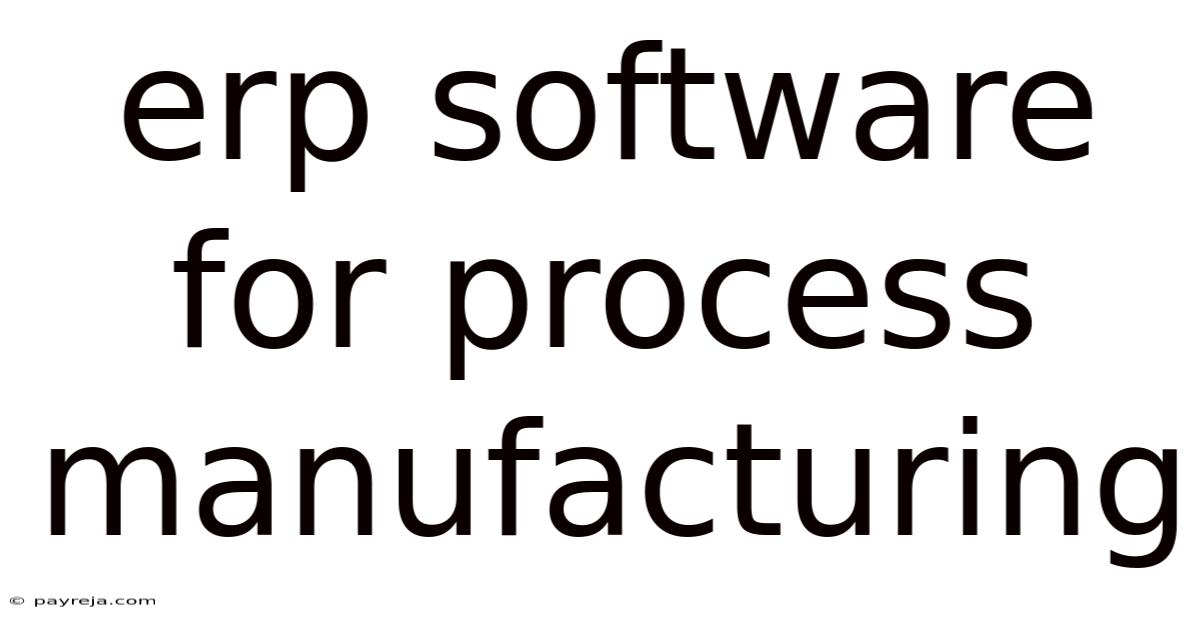
Thank you for visiting our website wich cover about Erp Software For Process Manufacturing. We hope the information provided has been useful to you. Feel free to contact us if you have any questions or need further assistance. See you next time and dont miss to bookmark.
Also read the following articles
Article Title | Date |
---|---|
Top Healthcare Erp Systems | Apr 17, 2025 |
Erp Workwear Industry | Apr 17, 2025 |
How To Remove Sap From Fabric | Apr 17, 2025 |
Global Link Erp | Apr 17, 2025 |
Pros And Cons Of Erp | Apr 17, 2025 |