Erp Ppsu
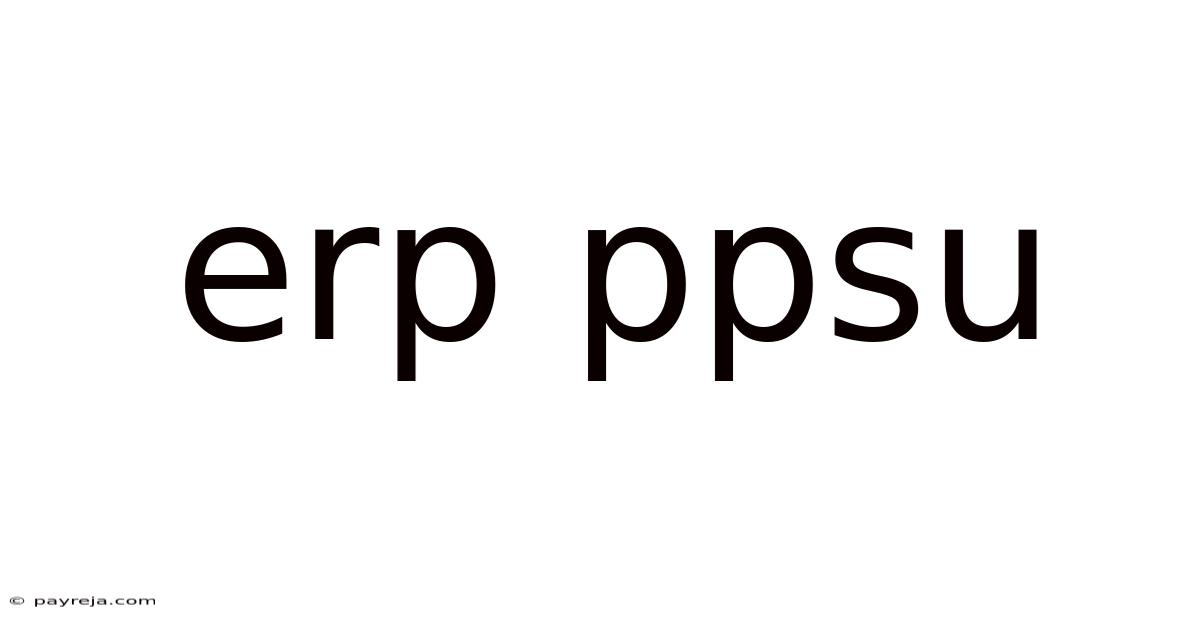
Discover more detailed and exciting information on our website. Click the link below to start your adventure: Visit Best Website meltwatermedia.ca. Don't miss out!
Table of Contents
Unlocking the Potential of ERP with PPSU: A Comprehensive Guide
What if integrating ERP with PPSU could revolutionize your manufacturing processes?
This powerful combination is transforming industries, driving efficiency, and unlocking unprecedented levels of productivity.
Editor’s Note: This article on ERP and PPSU integration has been published today, providing you with the latest insights and best practices in this rapidly evolving field.
Why ERP Integration with PPSU Matters
Enterprise Resource Planning (ERP) systems have long been the backbone of efficient business management, integrating various aspects of a company's operations. However, for manufacturers relying heavily on production planning and scheduling, integrating an ERP system with a sophisticated Production Planning and Scheduling System (PPS) utilizing Polyphenylene Sulfone (PPSU) technology offers a significant competitive advantage. This integration allows for greater precision, real-time visibility, and improved decision-making across the entire manufacturing lifecycle. The impact extends beyond simple efficiency gains; it touches upon cost reduction, waste minimization, improved customer satisfaction, and increased profitability. Businesses across diverse sectors, from automotive and aerospace to medical device manufacturing, are already reaping the rewards of this strategic synergy. This article will delve into the specifics of this powerful combination, exploring its functionalities, benefits, challenges, and future implications.
This article will cover:
- The fundamentals of ERP and PPS systems.
- The role of PPSU in advanced manufacturing.
- The benefits of integrating ERP with PPS.
- Key considerations for successful implementation.
- Case studies illustrating real-world applications.
- Future trends and potential advancements.
Understanding ERP and PPS Systems
ERP systems consolidate data from various departments—finance, human resources, supply chain, and manufacturing—onto a single platform. This centralized data provides a holistic view of business operations, facilitating better coordination and decision-making. Key ERP functionalities include inventory management, order processing, financial accounting, and production planning (though often at a higher, more aggregated level).
PPS systems, on the other hand, focus specifically on production planning and scheduling. They leverage advanced algorithms and optimization techniques to create detailed production schedules, taking into account factors like machine capacity, material availability, and labor constraints. The goal is to optimize production efficiency, minimize lead times, and ensure timely order fulfillment. The integration with ERP brings together the broader business context with the granular details of production.
The Role of PPSU in Advanced Manufacturing
While not directly a software component, PPSU (Polyphenylene Sulfone) plays a crucial role in the hardware and infrastructure supporting advanced manufacturing processes. PPSU is a high-performance thermoplastic known for its exceptional heat resistance, chemical resistance, and mechanical strength. This makes it ideal for applications requiring durable and reliable components in demanding manufacturing environments. For example, PPSU is often used in:
- High-temperature piping and valves: Ensuring efficient and safe handling of fluids and gases in manufacturing processes.
- Precision components in automation systems: Contributing to the reliability and longevity of robotics and automated machinery.
- Medical device components: Where biocompatibility and sterilization resistance are crucial.
The indirect relationship between PPSU and ERP/PPS integration lies in the improved efficiency and reliability of the manufacturing equipment itself. Robust and durable PPSU components contribute to less downtime, fewer maintenance issues, and ultimately, smoother production flows. This improved stability in the physical production process is then accurately reflected and managed within the integrated ERP/PPS system.
Benefits of Integrating ERP with PPS
The synergistic effect of integrating ERP and PPS systems, particularly in contexts where PPSU-based equipment is utilized, results in a significant improvement across several key areas:
- Enhanced Production Planning: Real-time data visibility from ERP allows the PPS system to dynamically adjust schedules based on actual material availability, machine performance, and order changes. This responsiveness minimizes disruptions and delays.
- Improved Inventory Management: Accurate forecasting driven by integrated data helps optimize inventory levels, reducing storage costs and preventing stockouts or overstocking.
- Reduced Lead Times: Optimized scheduling minimizes bottlenecks and maximizes resource utilization, leading to faster order fulfillment and improved customer satisfaction.
- Minimized Waste: Improved planning and scheduling reduce material waste through better resource allocation and reduced errors.
- Increased Transparency and Traceability: Complete visibility across the entire manufacturing process enables better tracking of materials, products, and production progress.
- Better Decision-Making: Centralized data provides managers with comprehensive insights, enabling informed decisions based on real-time data rather than estimations.
- Improved Capacity Utilization: Efficient scheduling maximizes the use of available resources, improving overall equipment effectiveness (OEE).
Key Considerations for Successful Implementation
Implementing an integrated ERP/PPS system requires careful planning and execution. Key considerations include:
- Data Migration: Transferring data from legacy systems to the new integrated platform requires meticulous planning and execution to ensure data integrity.
- System Integration: Ensuring seamless data flow between the ERP and PPS systems requires careful consideration of system compatibility and integration methods.
- User Training: Providing adequate training to users across different departments is crucial for successful adoption and efficient utilization of the system.
- Change Management: Effective communication and change management strategies are essential for minimizing resistance to change and ensuring smooth transition.
- Customization: Tailoring the system to meet the specific needs of the organization is important for optimal functionality and efficiency.
Case Studies: Real-World Applications
Numerous manufacturers have successfully implemented ERP/PPS integration, achieving significant improvements in efficiency and profitability. One example is a large automotive parts supplier that integrated its ERP system with a sophisticated PPS system, resulting in a 15% reduction in lead times and a 10% increase in production output. Another case involves a medical device manufacturer that used the integration to improve inventory management, reducing inventory holding costs by 8% and preventing several potential stockouts. These real-world examples demonstrate the transformative potential of this strategic combination.
Future Trends and Potential Advancements
The future of ERP/PPS integration is likely to see further advancements driven by emerging technologies such as:
- Artificial Intelligence (AI): AI-powered predictive analytics can help anticipate potential disruptions and optimize production schedules proactively.
- Machine Learning (ML): ML algorithms can learn from historical data to improve forecasting accuracy and optimize resource allocation.
- Internet of Things (IoT): Real-time data from connected manufacturing equipment provides greater visibility and enables more precise scheduling and optimization.
- Cloud Computing: Cloud-based ERP and PPS systems offer scalability, flexibility, and cost-effectiveness.
Exploring the Connection Between PPSU and ERP/PPS Integration
The relationship between PPSU and ERP/PPS integration is indirect but significant. The durability and reliability of PPSU components in manufacturing equipment contribute to improved uptime and reduced maintenance, creating a more stable and predictable production environment. This stability then translates directly into the accuracy and efficiency of the integrated ERP/PPS system. The system's planning and scheduling algorithms become more reliable as the underlying physical production process becomes less prone to unexpected disruptions. Accurate real-time data reflecting the true state of the production line becomes more readily available, leading to better decision-making and optimized resource allocation.
Roles and Real-World Examples: In a pharmaceutical manufacturing facility, PPSU valves in high-pressure fluid handling systems contribute to consistent and reliable operation, enabling precise production scheduling managed by the integrated ERP/PPS system.
Risks and Mitigations: The failure of PPSU components could disrupt production, impacting the accuracy of the ERP/PPS system's data. Regular maintenance and preventative measures minimize this risk.
Impact and Implications: Reliable PPSU components translate to better data for the ERP/PPS system, leading to more efficient planning, reduced waste, and improved overall profitability.
Dive Deeper into PPSU
PPSU's inherent properties—high strength, heat resistance, and chemical resistance—make it suitable for various high-performance applications in manufacturing. Its use minimizes equipment downtime due to component failures, fostering a stable and predictable production environment. This predictability allows the ERP/PPS system to function more effectively, generating accurate forecasts and optimizing scheduling.
Frequently Asked Questions (FAQ)
Q1: What are the main advantages of integrating ERP and PPS systems?
A1: Integrating ERP and PPS systems offers enhanced production planning, improved inventory management, reduced lead times, minimized waste, increased transparency, better decision-making, and improved capacity utilization.
Q2: How does PPSU contribute to the effectiveness of ERP/PPS integration?
A2: The reliability and durability of PPSU components in manufacturing equipment lead to less downtime and a more stable production environment, which enhances the accuracy and effectiveness of the integrated ERP/PPS system.
Q3: What are the key challenges in implementing an integrated ERP/PPS system?
A3: Key challenges include data migration, system integration, user training, change management, and system customization.
Q4: What are some future trends in ERP/PPS integration?
A4: Future trends include the integration of AI, ML, IoT, and cloud computing technologies.
Q5: Is ERP/PPS integration suitable for all manufacturing companies?
A5: While beneficial for many, the suitability of ERP/PPS integration depends on the size, complexity, and specific needs of the manufacturing company. Smaller companies might benefit from simpler solutions, while large-scale operations would benefit greatly from the capabilities of a fully integrated system.
Q6: How can I choose the right ERP/PPS system for my company?
A6: Careful evaluation of your company's specific needs, budget, and existing infrastructure is essential. Consider consulting with industry experts and seeking demonstrations of different systems before making a decision.
Actionable Tips on ERP/PPS Integration
- Conduct a thorough needs assessment: Identify your specific requirements and goals for ERP/PPS integration.
- Choose a reputable vendor: Select a vendor with proven experience and a strong track record of successful implementations.
- Develop a comprehensive implementation plan: Outline all steps, timelines, and responsibilities involved in the implementation process.
- Invest in adequate user training: Ensure all users receive sufficient training to use the system effectively.
- Monitor and optimize the system: Continuously monitor system performance and make adjustments as needed to improve efficiency.
- Embrace change management: Effectively communicate the benefits of the system to users and address any concerns or resistance to change.
- Integrate data from all relevant sources: Ensure comprehensive data integration for a holistic view of operations.
- Regularly review and update the system: Adapt the system to evolving business needs and technological advancements.
Conclusion
The integration of ERP and PPS systems, especially within a manufacturing context where PPSU contributes to stable equipment performance, offers significant potential for improving efficiency, reducing costs, and enhancing overall profitability. By carefully considering the key factors discussed and following best practices, manufacturers can unlock the full potential of this powerful combination, gaining a significant competitive advantage in today's dynamic market. The future of manufacturing hinges on embracing these advanced technologies and strategically leveraging their capabilities for optimal outcomes. Understanding the interplay between these elements is no longer a luxury—it's a necessity for sustained success in the manufacturing sector.
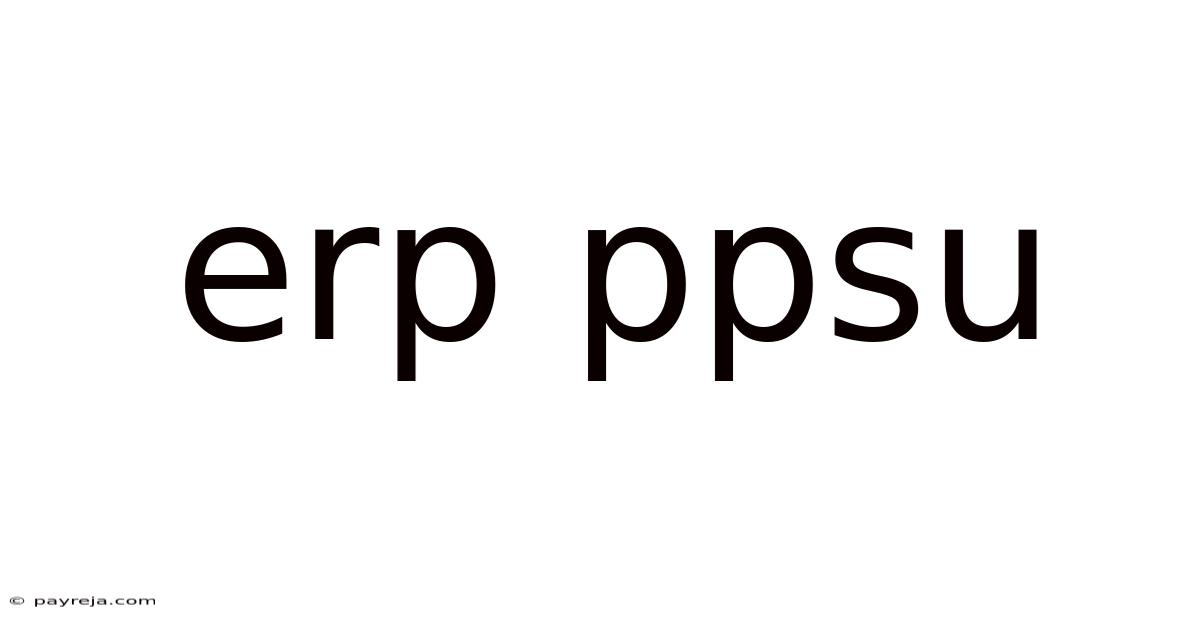
Thank you for visiting our website wich cover about Erp Ppsu. We hope the information provided has been useful to you. Feel free to contact us if you have any questions or need further assistance. See you next time and dont miss to bookmark.
Also read the following articles
Article Title | Date |
---|---|
Erp Business Analyst Salary | Apr 06, 2025 |
As400 Erp System | Apr 06, 2025 |
Erp Data Migration Checklist | Apr 06, 2025 |
Career In Erp Implementation | Apr 06, 2025 |
Erp Protocol | Apr 06, 2025 |