Erp Pps System
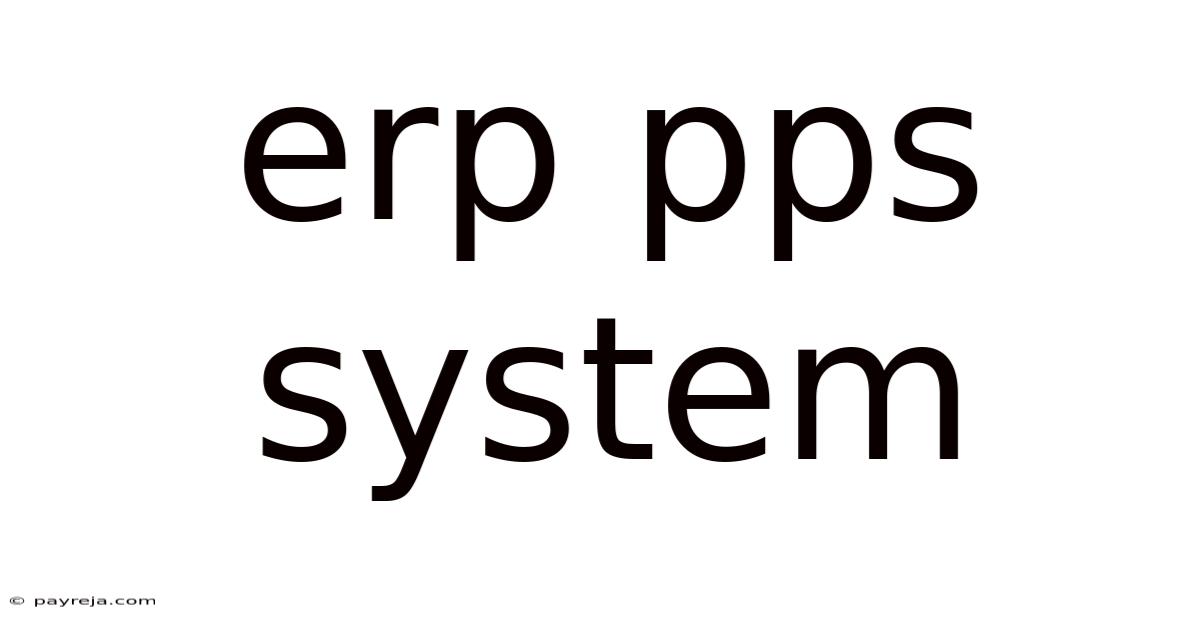
Discover more detailed and exciting information on our website. Click the link below to start your adventure: Visit Best Website meltwatermedia.ca. Don't miss out!
Table of Contents
Unlocking Efficiency: A Deep Dive into ERP PPS Systems
What if seamlessly integrating planning and production could revolutionize your manufacturing processes? ERP PPS systems are already transforming industries, streamlining operations, and boosting profitability.
Editor’s Note: This article on ERP PPS systems was published today, offering the most up-to-date insights and analysis in this rapidly evolving field.
Why ERP PPS Systems Matter
In today's competitive manufacturing landscape, efficiency and precision are paramount. Enterprise Resource Planning (ERP) systems, combined with Production Planning and Scheduling (PPS) modules, offer a powerful solution. ERP PPS systems integrate various aspects of a manufacturing business – from planning and scheduling to procurement, inventory management, and quality control – into a single, unified platform. This integration eliminates data silos, improves communication, and minimizes errors, ultimately leading to increased productivity, reduced costs, and improved customer satisfaction. The impact extends across various industries, including automotive, electronics, food processing, and pharmaceuticals, where precise production scheduling and efficient resource allocation are critical for success. For example, in the automotive industry, precise scheduling is essential to meet Just-In-Time (JIT) delivery requirements, while in the pharmaceutical sector, robust inventory management and quality control are paramount for regulatory compliance. Understanding and implementing a robust ERP PPS system is no longer a luxury but a necessity for competitive advantage.
This article will explore the key aspects of ERP PPS systems, covering their functionalities, benefits, implementation considerations, and future trends. Readers will gain a comprehensive understanding of how these systems can streamline their operations and drive significant improvements in their business. We will analyze the connection between effective capacity planning and successful ERP PPS implementation and delve into the intricacies of real-world applications and potential challenges.
A Bird's-Eye View of ERP PPS Systems
This article will cover the following key topics:
- Core Functionalities: Understanding the capabilities of a modern ERP PPS system.
- Capacity Planning Integration: The crucial role of capacity planning in optimizing production schedules.
- Real-World Applications and Case Studies: Examining how various industries utilize these systems.
- Implementation Challenges and Mitigation Strategies: Addressing potential hurdles and proposing solutions.
- Future Trends and Technological Advancements: Exploring the evolution of ERP PPS systems.
Understanding ERP PPS System Functionalities
ERP PPS systems are sophisticated software solutions designed to optimize the entire production process. Their core functionalities include:
- Demand Forecasting: Predicting future demand based on historical data and market trends.
- Production Planning: Creating detailed production plans that align with demand forecasts and available resources.
- Material Requirements Planning (MRP): Determining the exact quantities and timing of materials needed for production.
- Capacity Planning: Assessing the available resources (machines, labor, etc.) and ensuring they are sufficient to meet production demands.
- Scheduling: Optimizing the production schedule to maximize efficiency and minimize lead times.
- Inventory Management: Tracking inventory levels and optimizing stock to meet demand while minimizing storage costs.
- Shop Floor Control: Monitoring and controlling the production process in real-time.
- Quality Control: Integrating quality control checks throughout the production process to ensure product quality.
- Reporting and Analytics: Providing comprehensive reports and analytics to track key performance indicators (KPIs).
These functionalities work in concert to create a cohesive, efficient production process. For instance, accurate demand forecasting informs production planning, which in turn drives material requirements planning and capacity planning. Effective scheduling ensures that production runs smoothly and meets deadlines, while real-time shop floor control allows for immediate adjustments in response to unforeseen events. Finally, comprehensive reporting and analytics provide valuable insights into the entire production process, allowing for continuous improvement.
The Vital Link: Capacity Planning and ERP PPS Success
Effective capacity planning is absolutely crucial for the success of any ERP PPS implementation. It involves analyzing the available resources – machines, labor, space, and other production inputs – and comparing them to the planned production volume. Without accurate capacity planning, production schedules will be unrealistic, leading to delays, bottlenecks, and increased costs. A well-designed ERP PPS system will integrate capacity planning seamlessly into the production planning process, providing real-time visibility into resource utilization and enabling proactive adjustments to the schedule as needed.
For instance, if capacity planning reveals a shortage of skilled labor for a particular production step, the system can automatically adjust the production schedule to compensate, perhaps by shifting some tasks to a different time slot or assigning additional resources. This proactive approach ensures that production remains on track, minimizing the risk of delays and disruptions.
Real-World Applications and Case Studies
The applications of ERP PPS systems are vast and varied. Let’s consider a few examples:
-
Automotive Manufacturing: Automakers use ERP PPS systems to manage complex supply chains, optimize production schedules to meet stringent delivery deadlines, and track the quality of parts throughout the manufacturing process. This ensures that vehicles are produced efficiently and meet the highest quality standards.
-
Electronics Manufacturing: Electronics manufacturers utilize these systems to manage the intricate assembly processes involving numerous components and suppliers. Accurate inventory management and efficient scheduling are critical for meeting demand and minimizing lead times in this fast-paced industry.
-
Pharmaceutical Manufacturing: In the pharmaceutical industry, adherence to strict regulatory requirements is paramount. ERP PPS systems ensure that production processes comply with Good Manufacturing Practices (GMP) and track the movement of materials and finished goods to maintain traceability.
-
Food and Beverage Production: Food and beverage producers use these systems to manage perishable goods effectively, optimize production schedules to minimize waste, and track the entire lifecycle of their products to ensure food safety and quality.
These examples highlight the versatility and adaptability of ERP PPS systems across diverse manufacturing environments. The specific requirements and functionalities of the system will, of course, vary depending on the industry and the size of the organization.
Implementation Challenges and Mitigation Strategies
Implementing an ERP PPS system can present significant challenges. Some common obstacles include:
- Data Migration: Transferring data from legacy systems to the new ERP PPS system can be a complex and time-consuming process.
- Integration with Existing Systems: The ERP PPS system needs to integrate seamlessly with other systems used by the organization, such as CRM and supply chain management systems.
- Change Management: Implementing a new system requires significant changes to business processes and employee workflows, which can lead to resistance from employees.
- Cost and Resources: Implementing an ERP PPS system can be expensive and requires significant resources.
- System Customization: Often, standard ERP solutions need customization to meet the specific needs of the organization.
However, these challenges can be mitigated through careful planning and execution. A phased rollout approach, comprehensive training for employees, and strong project management can help to overcome these hurdles. It is also crucial to select an ERP vendor with a proven track record and extensive experience in the target industry.
Future Trends and Technological Advancements
The future of ERP PPS systems is bright, driven by technological advancements such as:
-
Artificial Intelligence (AI) and Machine Learning (ML): AI and ML can significantly improve demand forecasting, optimize production schedules, and enhance predictive maintenance.
-
Internet of Things (IoT): IoT devices can provide real-time data on production processes, enabling more efficient monitoring and control.
-
Cloud Computing: Cloud-based ERP PPS systems offer greater flexibility, scalability, and cost-effectiveness.
-
Blockchain Technology: Blockchain can enhance transparency and traceability throughout the supply chain.
-
Digital Twins: Creating virtual representations of production processes allows for simulation and optimization before implementation.
These advancements will continue to improve the efficiency, effectiveness, and adaptability of ERP PPS systems, enabling manufacturers to stay ahead of the curve in an increasingly competitive global market.
Key Insights: A Summary
Insight | Description |
---|---|
Seamless Integration | ERP PPS systems integrate various aspects of manufacturing for a unified platform. |
Enhanced Efficiency & Productivity | Optimized processes lead to reduced costs, improved lead times, and increased output. |
Data-Driven Decision Making | Comprehensive reports and analytics provide valuable insights for continuous improvement. |
Improved Supply Chain Visibility | Real-time monitoring and tracking offer better control over materials, production, and delivery. |
Reduced Operational Costs | Minimizing waste, errors, and delays contributes to significant cost savings. |
Enhanced Customer Satisfaction | Meeting delivery deadlines and providing high-quality products improves customer satisfaction and loyalty. |
Adaptability and Scalability | These systems are adaptable to different industries and can scale to meet the growing needs of the organization. |
Technological Advancements Driving Innovation | AI, IoT, cloud computing, and blockchain enhance capabilities, creating smarter, more efficient production environments. |
The Interplay Between Capacity Planning and ERP PPS System Success
Capacity planning forms the backbone of a successful ERP PPS implementation. Without accurate capacity assessments, the production plans generated by the system will be inherently flawed, leading to scheduling conflicts, delays, and ultimately, project failures. The ERP PPS system leverages the capacity data to create realistic production schedules, optimize resource allocation, and identify potential bottlenecks before they disrupt the workflow. For instance, if the capacity plan reveals insufficient machine time for a particular operation, the system can either suggest overtime, prioritize other tasks, or even recommend investing in additional equipment.
Roles and Real-World Examples: In a manufacturing facility producing automotive parts, capacity planning might reveal that the assembly line is operating at 90% capacity. The ERP PPS system can then utilize this information to create a schedule that optimizes production flow and prevents bottlenecks. If demand suddenly increases, the system can analyze the capacity constraints and propose solutions, such as adjusting staffing levels or temporarily outsourcing certain tasks.
Risks and Mitigations: Failure to adequately assess capacity can lead to production delays, cost overruns, and missed delivery deadlines. This can damage relationships with customers and impact the company’s reputation. Mitigation strategies include conducting thorough capacity assessments before implementation, continuously monitoring capacity utilization, and using the ERP PPS system's reporting tools to identify potential issues proactively.
Impact and Implications: Accurate capacity planning integrated with an ERP PPS system has a profound impact on a manufacturing organization's efficiency and profitability. It enhances productivity, reduces lead times, minimizes waste, and improves customer satisfaction. The long-term impact includes increased competitiveness and improved market share.
Deep Dive into Capacity Planning
Capacity planning involves a multi-faceted approach that considers both short-term and long-term needs. Short-term capacity planning focuses on optimizing the allocation of resources to meet immediate production demands, while long-term capacity planning anticipates future needs and ensures that the organization has sufficient resources to meet projected demand growth. Various techniques are employed, including:
- Break-even Analysis: Determining the production volume required to cover costs.
- Linear Programming: Optimizing resource allocation to maximize output.
- Simulation Modeling: Simulating different scenarios to evaluate the impact of various decisions.
The choice of techniques depends on the complexity of the production process, the available data, and the organization's specific needs. The data gathered during capacity planning is then fed into the ERP PPS system to create accurate and realistic production schedules.
Frequently Asked Questions (FAQ)
Q1: What is the difference between an ERP system and an ERP PPS system?
A1: An ERP system is a comprehensive software solution that integrates various business functions, including finance, human resources, and supply chain management. An ERP PPS system is a specialized module within an ERP system that focuses specifically on production planning and scheduling.
Q2: How much does an ERP PPS system cost?
A2: The cost of an ERP PPS system varies widely depending on the size of the organization, the complexity of the system, and the level of customization required. Costs can range from tens of thousands to millions of dollars.
Q3: How long does it take to implement an ERP PPS system?
A3: Implementation time depends on several factors, including the size and complexity of the organization, the scope of the implementation, and the level of customization needed. Implementation can take anywhere from several months to over a year.
Q4: What are the key benefits of using an ERP PPS system?
A4: Key benefits include improved efficiency, reduced costs, enhanced visibility, better decision-making, improved quality control, and increased customer satisfaction.
Q5: What are the risks associated with implementing an ERP PPS system?
A5: Risks include high implementation costs, potential disruptions to operations, resistance to change from employees, and integration challenges with existing systems.
Q6: What are some key metrics to track the success of an ERP PPS implementation?
A6: Key metrics include on-time delivery rates, production lead times, inventory turnover, machine utilization rates, and overall equipment effectiveness (OEE).
Actionable Tips for Successful ERP PPS Implementation
- Clearly define your requirements: Before selecting an ERP PPS system, carefully define your specific needs and requirements.
- Select a reputable vendor: Choose a vendor with a proven track record and experience in your industry.
- Develop a comprehensive implementation plan: Create a detailed plan that outlines all phases of the implementation process.
- Provide thorough training to employees: Train your employees on how to use the new system effectively.
- Monitor the system closely: Track key performance indicators (KPIs) to ensure that the system is meeting your expectations.
- Continuously improve the system: Regularly review and update the system to ensure that it remains efficient and effective.
- Integrate capacity planning: Ensure that capacity planning is integrated seamlessly into the ERP PPS system.
- Embrace change management: Foster a culture of continuous improvement and encourage employee participation in the implementation process.
Conclusion
ERP PPS systems are transforming the manufacturing landscape, driving efficiency, reducing costs, and improving overall productivity. The integration of capacity planning is critical for success, ensuring that production schedules are realistic and resource allocation is optimized. While implementation challenges exist, careful planning and execution can mitigate these risks. The future of ERP PPS systems is marked by exciting technological advancements that promise even greater efficiency and improved decision-making capabilities. By understanding the functionalities, benefits, and potential challenges associated with these systems, manufacturing organizations can position themselves for success in a dynamic and competitive global market. The journey towards optimized production begins with a commitment to understanding and implementing the power of a well-integrated ERP PPS system.
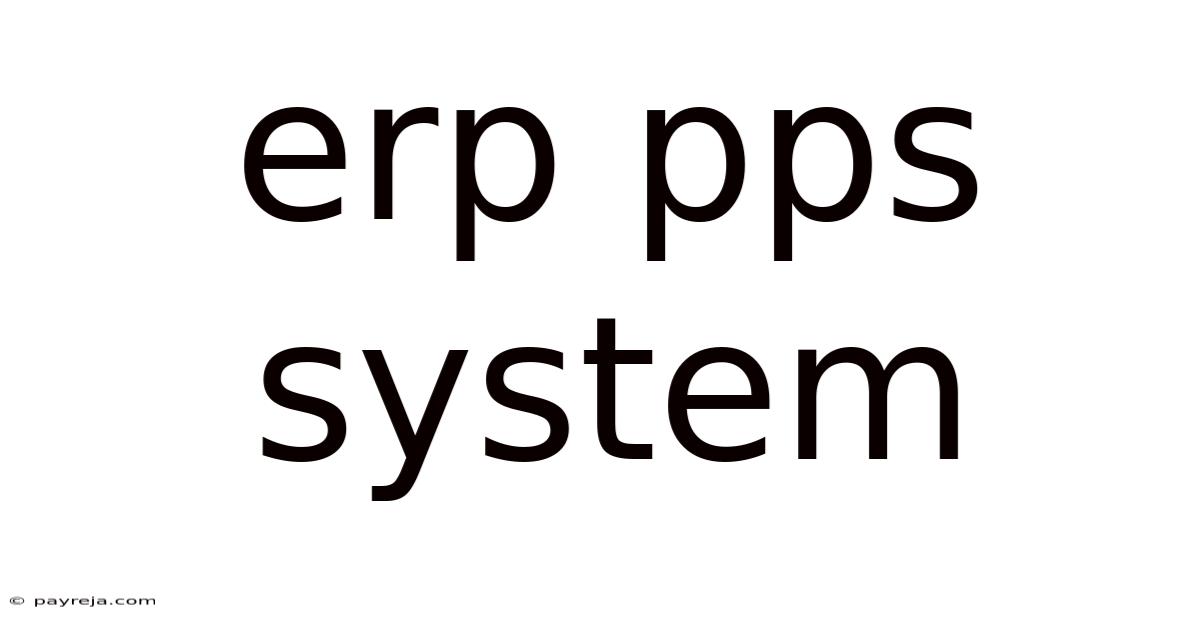
Thank you for visiting our website wich cover about Erp Pps System. We hope the information provided has been useful to you. Feel free to contact us if you have any questions or need further assistance. See you next time and dont miss to bookmark.
Also read the following articles
Article Title | Date |
---|---|
Erp Pro 10 | Apr 06, 2025 |
Erp 2022 Payments | Apr 06, 2025 |
Erp Manufacturing System | Apr 06, 2025 |
Erp Pour Gestion Logistique | Apr 06, 2025 |
Erp Comparisons | Apr 06, 2025 |