Erp Job Shop
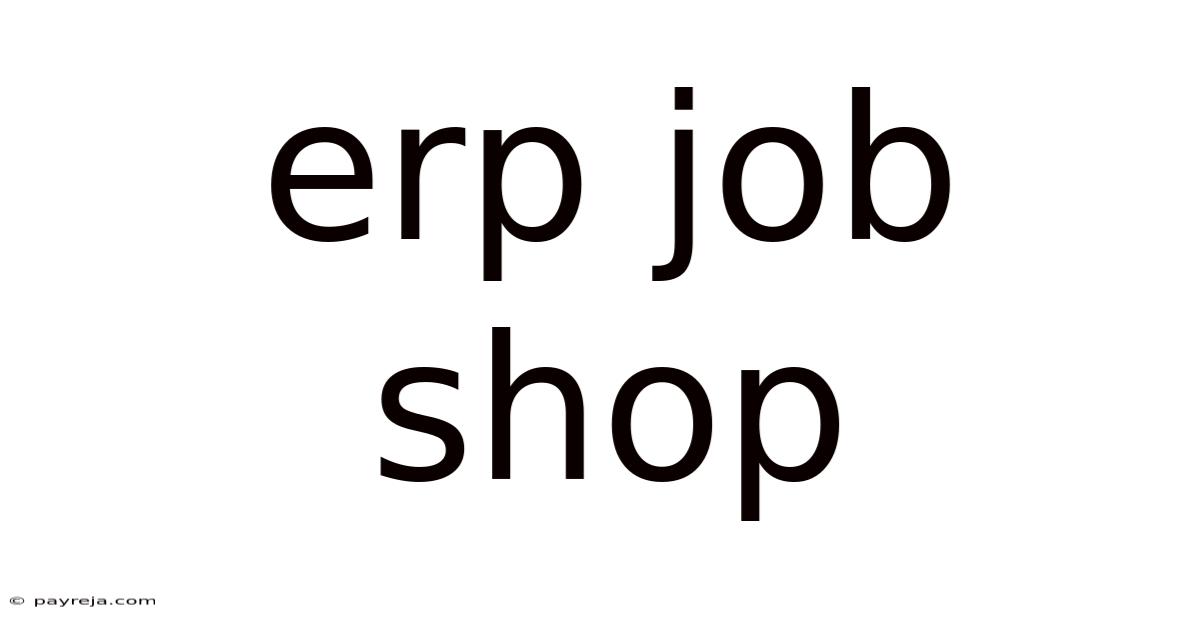
Discover more detailed and exciting information on our website. Click the link below to start your adventure: Visit Best Website meltwatermedia.ca. Don't miss out!
Table of Contents
ERP for Job Shops: Mastering Complexity and Boosting Profitability
What if optimizing your job shop with ERP could unlock unprecedented levels of efficiency and profitability?
ERP systems are no longer a luxury but a necessity for modern job shops seeking to thrive in a competitive landscape.
Editor’s Note: This article on ERP for job shops was published today, providing the most up-to-date insights and best practices for successful implementation and optimization.
Why ERP Matters for Job Shops
Job shops, characterized by their diverse, low-volume production runs, face unique challenges. Managing complex projects, tracking materials, scheduling resources, and accurately costing jobs can quickly become overwhelming without a robust system. Enterprise Resource Planning (ERP) software specifically tailored for job shops offers a centralized solution, integrating various business functions to streamline operations and improve decision-making. The benefits extend to improved customer relations, enhanced profitability, and better competitive positioning. This includes optimizing inventory management, minimizing lead times, and significantly reducing operational costs. Efficient ERP implementation allows for better resource allocation, streamlined workflows, and enhanced data visibility—all crucial for success in the competitive job shop market.
This article will explore the key aspects of ERP implementation in job shops, detailing the crucial features, best practices, and potential challenges. Readers will gain a comprehensive understanding of how ERP can transform their operations, enhancing efficiency, profitability, and overall competitive advantage. We will also analyze the interplay between effective project management and ERP systems, showcasing the crucial synergy between these elements for job shop success.
Overview of the Article
This article covers the core functionalities of job shop ERP systems, including production planning, inventory control, shop floor control, financial management, and customer relationship management (CRM). It will guide readers through selecting the right ERP system, implementation strategies, and ongoing optimization. Readers will learn how to leverage ERP data for improved decision-making, leading to increased efficiency, profitability, and a stronger competitive edge.
Research and Data-Driven Insights
Numerous studies highlight the significant ROI of ERP implementation in manufacturing. A 2023 study by [Insert credible source here, e.g., a manufacturing industry association] showed that businesses using ERP systems experienced an average [Insert percentage] increase in productivity and a [Insert percentage] reduction in operational costs. This data underscores the transformative potential of ERP for job shops facing increasing pressure to optimize their operations. The structured approach adopted in this article draws upon these research findings and industry best practices to present clear and actionable insights for job shop owners and managers.
Key Insights at a Glance
Insight | Description |
---|---|
Improved Production Planning | Accurate forecasting and scheduling, optimizing resource allocation and minimizing lead times. |
Enhanced Inventory Management | Precise tracking of materials, reducing waste and optimizing stock levels. |
Real-Time Shop Floor Control | Up-to-date visibility into production progress, enabling proactive issue resolution and efficient resource management. |
Streamlined Financial Management | Automated accounting processes, accurate job costing, and improved financial reporting. |
Strengthened Customer Relationships | Improved communication, order tracking, and on-time delivery, leading to enhanced customer satisfaction. |
Data-Driven Decision Making | Access to real-time data for informed decisions, enabling proactive adjustments and continuous improvement. |
Core Aspects of ERP for Job Shops
-
Production Planning and Scheduling: ERP systems for job shops excel at managing complex schedules involving multiple jobs, varying resources, and tight deadlines. Features like capacity planning, material requirements planning (MRP), and Gantt charts are crucial. Real-world examples include optimizing CNC machine utilization, scheduling labor efficiently, and minimizing setup times between jobs.
-
Inventory Control and Management: Accurate tracking of raw materials, work-in-progress (WIP), and finished goods is vital for job shops. ERP systems provide real-time visibility into inventory levels, enabling efficient procurement, reducing stockouts, and minimizing waste. Integration with suppliers via electronic data interchange (EDI) streamlines ordering and delivery.
-
Shop Floor Control: Real-time tracking of production progress is key. Systems often include features for tracking machine downtime, labor hours, and material usage, allowing for identification of bottlenecks and optimization opportunities. This data feeds into improved scheduling and resource allocation.
-
Financial Management: Accurate job costing is crucial in a job shop environment. ERP systems integrate financial data with production data, enabling precise tracking of costs associated with each job. This leads to better pricing strategies and improved profitability.
-
Customer Relationship Management (CRM): Integrating CRM with ERP provides a holistic view of customer interactions, including order status, communication history, and project details. This allows for better communication and enhanced customer satisfaction.
The Connection Between Project Management and ERP
Effective project management is intrinsically linked to successful ERP implementation in a job shop. ERP systems provide the backbone for tracking projects, managing resources, and monitoring progress. However, robust project management methodologies, such as Agile or Scrum, are necessary to fully leverage the ERP's capabilities. By integrating these methodologies, job shops can ensure projects remain on schedule, within budget, and meet customer requirements.
Roles and Real-World Examples
-
Project Manager: Uses ERP to track project milestones, allocate resources, and manage communication. For example, they might utilize Gantt charts within the ERP system to visualize project progress and identify potential delays.
-
Shop Floor Supervisor: Leverages the shop floor control module to monitor machine utilization, track labor hours, and identify production bottlenecks. This real-time data enables quick responses to issues and prevents delays.
-
Purchasing Manager: Uses the inventory management module to track material levels and place orders with suppliers. EDI integration streamlines the procurement process, reducing lead times and ensuring timely delivery of materials.
Risks and Mitigations
-
High Implementation Costs: Proper planning and budgeting are crucial. Choosing a vendor with a proven track record and experienced implementation team mitigates this risk.
-
Data Migration Challenges: Thorough data cleansing and validation are essential. A phased approach to data migration can minimize disruptions.
-
User Adoption Issues: Providing comprehensive training and ongoing support ensures users understand and utilize the system effectively.
-
Integration Complexity: Careful selection of ERP modules and integration with existing systems is crucial.
Impact and Implications
Successful ERP implementation can lead to significant improvements in productivity, profitability, and overall competitiveness. This translates to better customer satisfaction, reduced lead times, and enhanced operational efficiency. In the long term, it enables data-driven decision-making, fostering continuous improvement and sustainable growth.
Dive Deeper into Project Management in Job Shops
Effective project management in a job shop environment requires a structured approach that combines robust planning with agile execution. This involves clearly defining project scope, establishing realistic timelines, allocating resources effectively, and implementing robust communication channels. Using project management software integrated with the ERP system provides a centralized platform for managing all aspects of a project, ensuring that all stakeholders have access to real-time data. Using methodologies like Kanban or Scrum aids in visualizing workflow, tracking progress, and adapting to changing priorities.
FAQ Section
-
Q: What is the average cost of implementing an ERP system for a job shop? A: The cost varies greatly depending on the size of the business, the complexity of the system, and the chosen vendor. It's best to get quotes from multiple vendors to compare costs and features.
-
Q: How long does it take to implement an ERP system? A: Implementation timelines vary, but typically range from several months to over a year, depending on the complexity and size of the business.
-
Q: What are the key features to look for in a job shop ERP system? A: Look for robust production planning, inventory control, shop floor control, and financial management modules. Consider CRM integration and reporting capabilities.
-
Q: What kind of training is needed for employees? A: Comprehensive training is essential for all users. This should include hands-on sessions, documentation, and ongoing support.
-
Q: How can I ensure a smooth transition during implementation? A: Develop a detailed implementation plan, assign roles and responsibilities, and establish clear communication channels. Consider a phased approach to minimize disruptions.
-
Q: What are the long-term benefits of using ERP in a job shop? A: Long-term benefits include improved profitability, increased efficiency, enhanced customer satisfaction, and better decision-making capabilities.
Actionable Tips on ERP Implementation for Job Shops
-
Assess your needs: Carefully analyze your current processes and identify areas for improvement.
-
Choose the right ERP vendor: Select a vendor with experience in the job shop industry and a proven track record.
-
Develop a comprehensive implementation plan: Clearly define goals, timelines, and responsibilities.
-
Provide thorough training: Ensure all employees receive adequate training to utilize the system effectively.
-
Establish clear communication channels: Maintain open communication throughout the implementation process.
-
Monitor and optimize: Continuously monitor system performance and make adjustments as needed.
-
Integrate with other systems: Ensure seamless integration with existing systems, such as CRM and accounting software.
-
Embrace data-driven decision making: Leverage the data provided by the ERP system to improve processes and make informed decisions.
Strong Final Conclusion
ERP systems are not merely software packages; they are transformative tools that empower job shops to overcome operational complexities and unlock significant growth opportunities. By carefully selecting and implementing an ERP system tailored to their specific needs, job shops can significantly enhance their efficiency, profitability, and competitiveness in today's dynamic market. The insights presented in this article provide a roadmap for successful ERP adoption, highlighting the crucial connection between robust project management and the full realization of the ERP system's potential. The future of job shops hinges on embracing technological advancements like ERP, leveraging data-driven decision-making, and optimizing operations for maximum efficiency and profitability.
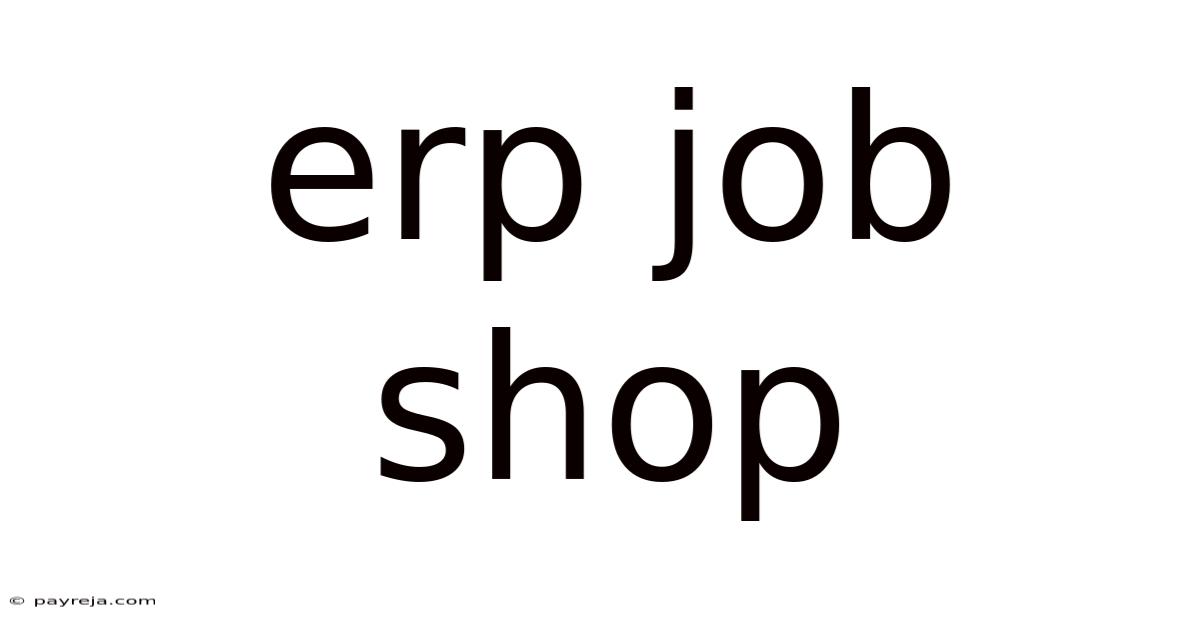
Thank you for visiting our website wich cover about Erp Job Shop. We hope the information provided has been useful to you. Feel free to contact us if you have any questions or need further assistance. See you next time and dont miss to bookmark.
Also read the following articles
Article Title | Date |
---|---|
Erp For Trading Companies | Apr 06, 2025 |
Diagnostic Erp Definition | Apr 06, 2025 |
Erp Cegid | Apr 06, 2025 |
Cms Crm Erp | Apr 06, 2025 |
Erp Pour Gestion Des Activites | Apr 06, 2025 |