Erp Implementation In Manufacturing Industry
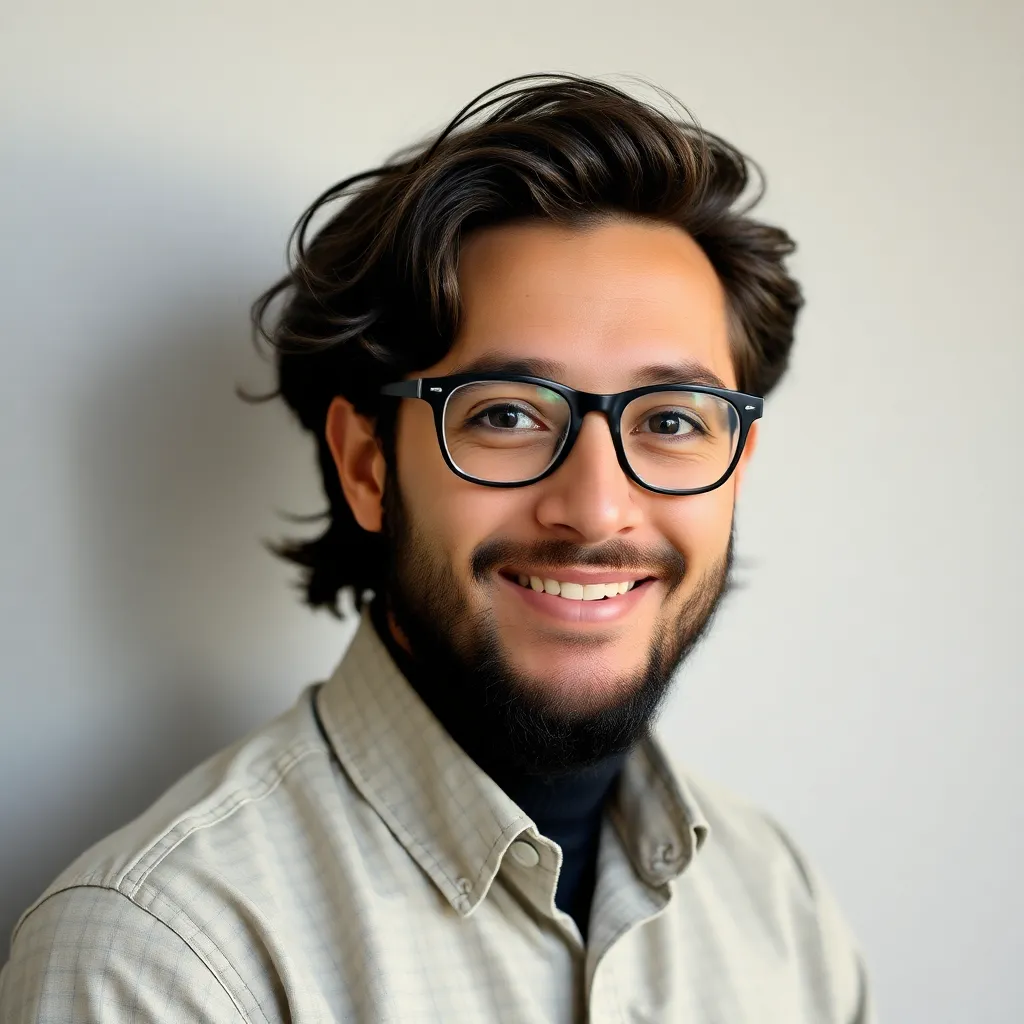
adminse
Apr 06, 2025 · 10 min read

Table of Contents
ERP Implementation in the Manufacturing Industry: A Comprehensive Guide
Unlocking the Power of ERP: Transforming Manufacturing Operations
Implementing an ERP system is no longer a luxury but a necessity for manufacturing companies seeking to thrive in today's competitive landscape.
Editor’s Note: This article on ERP implementation in the manufacturing industry was published on [Date]. The information presented reflects the current best practices and trends in the field.
Why ERP Matters in Manufacturing
The manufacturing industry is characterized by complex processes, intricate supply chains, and demanding customer expectations. Efficient management of resources, accurate forecasting, and streamlined operations are crucial for survival and growth. Enterprise Resource Planning (ERP) systems offer a unified solution to address these challenges. By integrating various business functions—from procurement and production to sales and finance—ERP systems provide a holistic view of the manufacturing process, enabling data-driven decision-making and operational optimization. This leads to improved efficiency, reduced costs, enhanced customer satisfaction, and increased profitability. The ability to manage inventory effectively, track production in real-time, and gain insights into overall operational performance are all key benefits driving the widespread adoption of ERP in manufacturing. Furthermore, improved supply chain visibility contributes to better risk management and faster response times to market fluctuations.
This article will explore the key aspects of ERP implementation in the manufacturing sector, covering the process, challenges, and best practices for a successful deployment. Readers will learn about the selection process, change management strategies, and post-implementation support necessary to maximize the return on investment (ROI) from an ERP system. Finally, the article will delve into the relationship between data analytics and ERP success, emphasizing how data-driven insights can further enhance operational efficiency and profitability.
Overview of the Article
This article provides a comprehensive guide to ERP implementation in the manufacturing industry. It covers the following key topics:
- Understanding ERP and its relevance to manufacturing.
- The ERP implementation lifecycle: from planning to post-implementation support.
- Key considerations for selecting the right ERP solution.
- Addressing the challenges of ERP implementation, including change management and data migration.
- Leveraging data analytics for optimizing ERP performance.
- The connection between data analytics and successful ERP implementation.
- Frequently asked questions about ERP implementation.
- Actionable tips for a smooth and successful ERP implementation.
Readers will gain valuable insights into the process of implementing an ERP system, enabling them to make informed decisions and optimize their manufacturing operations.
The ERP Implementation Lifecycle
The successful implementation of an ERP system in a manufacturing environment follows a well-defined lifecycle, typically consisting of several key phases:
1. Planning & Requirements Gathering: This initial phase involves a thorough assessment of the current manufacturing processes, identifying pain points, and defining the specific business needs that the ERP system should address. This includes defining key performance indicators (KPIs) that will be used to measure the success of the implementation. Stakeholder engagement is crucial at this stage to ensure that the system meets the needs of all relevant departments.
2. Vendor Selection: Choosing the right ERP vendor is critical. This involves evaluating different ERP solutions based on factors such as functionality, scalability, cost, vendor support, and integration capabilities. Request for Proposals (RFPs) are often used to solicit bids from multiple vendors, allowing for a comparative analysis.
3. System Design & Customization: Once a vendor is selected, the system is designed to meet the specific needs of the manufacturing organization. This may involve customizing certain modules or integrating with existing systems. Careful planning and collaboration between the implementation team and the vendor are essential to ensure a seamless integration.
4. Data Migration: This critical phase involves transferring data from existing systems to the new ERP system. Thorough data cleansing and validation are necessary to ensure data accuracy and integrity. A well-defined migration plan is essential to minimize disruption to business operations.
5. System Testing & Training: Rigorous testing is essential to identify and resolve any bugs or issues before the system goes live. Comprehensive training for end-users is crucial to ensure they can effectively utilize the system's functionalities.
6. Go-Live & Post-Implementation Support: The go-live phase marks the official launch of the ERP system. Post-implementation support is crucial for addressing any unexpected issues and ensuring the continued smooth operation of the system. Regular system maintenance and updates are also vital.
Key Considerations for ERP Selection
The selection of the right ERP system is crucial for the success of the implementation. Key considerations include:
- Industry-Specific Functionality: The ERP system should be tailored to the specific needs of the manufacturing industry, offering features such as manufacturing execution system (MES) integration, production planning, inventory management, and quality control.
- Scalability and Flexibility: The system should be able to scale to accommodate the growth of the manufacturing organization. Flexibility is also essential to adapt to changing business requirements.
- Integration Capabilities: The ERP system should integrate seamlessly with existing systems, such as CRM, supply chain management (SCM), and MES systems.
- Vendor Support and Reputation: Choose a vendor with a strong reputation for providing excellent customer support and a proven track record of successful ERP implementations.
- Cost and ROI: Consider the total cost of ownership (TCO) and the potential return on investment (ROI) of the ERP system.
Challenges of ERP Implementation
ERP implementation can be challenging, with common hurdles including:
- Change Management: Successfully implementing an ERP system requires significant changes in business processes and employee workflows. Effective change management strategies are essential to address resistance to change and ensure smooth adoption.
- Data Migration: Migrating data from legacy systems can be complex and time-consuming, requiring careful planning and execution to minimize data loss and ensure accuracy.
- Integration Complexity: Integrating the ERP system with existing systems can be challenging, requiring technical expertise and careful planning.
- Cost Overruns: ERP implementations can be expensive, and cost overruns are a common problem. Careful budgeting and project management are essential to avoid cost overruns.
- Lack of User Adoption: If end-users are not properly trained and do not understand the benefits of the new system, adoption rates will suffer, rendering the implementation less effective.
Leveraging Data Analytics for Optimizing ERP Performance
Modern ERP systems generate vast amounts of data. Leveraging data analytics is crucial for extracting valuable insights from this data to optimize manufacturing operations. This includes:
- Predictive Maintenance: Analyzing machine data to predict potential equipment failures and schedule maintenance proactively.
- Supply Chain Optimization: Analyzing supply chain data to identify bottlenecks and improve efficiency.
- Production Planning and Scheduling: Analyzing production data to optimize production schedules and minimize lead times.
- Quality Control: Analyzing quality data to identify defects and improve product quality.
- Inventory Management: Analyzing inventory data to optimize inventory levels and minimize storage costs.
The Connection Between Data Analytics and Successful ERP Implementation
The connection between data analytics and successful ERP implementation is strong. By leveraging the data generated by the ERP system, manufacturers can gain valuable insights into their operations, leading to improved efficiency, reduced costs, and increased profitability. This data-driven approach to decision-making is essential for maximizing the return on investment from an ERP system.
Explore the Connection Between Data Analytics and ERP Implementation
Data analytics significantly impacts the success of ERP implementation in several ways. First, it helps in the initial planning phase by providing a clearer understanding of existing processes and identifying areas for improvement. This data-driven approach informs the selection of appropriate ERP modules and customization options. During the implementation phase, data analytics helps in efficient data migration by identifying and resolving data inconsistencies. Post-implementation, data analytics monitors system performance, allowing for proactive adjustments and optimization. Companies that leverage data analytics during and after ERP implementation enjoy greater efficiency gains, improved decision-making, and higher overall ROI.
Roles and Real-World Examples: Data analysts play a crucial role in extracting meaningful insights from ERP data, providing actionable recommendations for process improvement. For example, a manufacturer might use data analytics to identify a production bottleneck, leading to changes in the production process that reduce lead times and increase output.
Risks and Mitigations: The risk of inadequate data quality can negatively impact the insights derived from analytics. Mitigation strategies include robust data cleansing procedures and the implementation of data governance policies.
Impact and Implications: The successful integration of data analytics into ERP systems leads to a data-driven culture, enhancing operational efficiency and competitiveness. This results in improved financial performance, enhanced customer satisfaction, and greater agility in responding to market changes.
Dive Deeper into Data Analytics
Data analytics is a multi-faceted field. Different analytical techniques are applied depending on the specific objectives. Descriptive analytics summarizes past data, providing insights into historical performance. Diagnostic analytics investigates the reasons behind past performance, helping identify the root causes of problems. Predictive analytics uses historical data to forecast future outcomes, enabling proactive decision-making. Prescriptive analytics suggests optimal actions based on predictive models, guiding decision-makers towards the best course of action. Each technique contributes to a comprehensive understanding of manufacturing operations, improving efficiency and profitability.
Analytical Technique | Description | Example in Manufacturing |
---|---|---|
Descriptive | Summarizes past data | Analyzing historical production data to identify trends. |
Diagnostic | Investigates causes of past performance | Analyzing defect rates to identify root causes of quality issues. |
Predictive | Forecasts future outcomes | Predicting equipment failures to schedule maintenance proactively. |
Prescriptive | Recommends optimal actions | Suggesting optimal production schedules to minimize lead times. |
Frequently Asked Questions (FAQ)
Q1: What is the average cost of ERP implementation in manufacturing?
A1: The cost varies widely depending on the size of the organization, the complexity of the system, and the level of customization required. It can range from tens of thousands to millions of dollars.
Q2: How long does it typically take to implement an ERP system?
A2: The implementation timeline depends on the size and complexity of the project. It can range from several months to over a year.
Q3: What are the key benefits of ERP implementation in manufacturing?
A3: Key benefits include improved efficiency, reduced costs, enhanced customer satisfaction, increased profitability, better inventory management, real-time production tracking, and improved supply chain visibility.
Q4: What are some common challenges encountered during ERP implementation?
A4: Common challenges include change management, data migration, integration complexity, cost overruns, and lack of user adoption.
Q5: How can I ensure a successful ERP implementation?
A5: A successful implementation requires careful planning, thorough requirements gathering, effective change management, rigorous testing, and comprehensive user training. Choosing the right vendor and having a dedicated implementation team are also critical.
Q6: What is the role of data analytics in ERP implementation?
A6: Data analytics is crucial for extracting valuable insights from ERP data to optimize manufacturing operations, improve decision-making, and maximize the return on investment from the ERP system.
Actionable Tips for ERP Implementation Success
- Clearly Define Requirements: Thoroughly assess your manufacturing processes and define your specific business needs.
- Choose the Right Vendor: Carefully evaluate different ERP vendors and select the one that best meets your needs.
- Develop a Detailed Implementation Plan: Create a comprehensive plan that outlines all the phases of the implementation process.
- Engage Stakeholders: Involve key stakeholders from all departments in the implementation process.
- Provide Comprehensive Training: Provide thorough training to end-users to ensure they can effectively utilize the system.
- Implement Change Management Strategies: Develop and implement strategies to address resistance to change and ensure smooth adoption.
- Monitor and Evaluate Performance: Continuously monitor the performance of the ERP system and make adjustments as needed.
- Leverage Data Analytics: Utilize data analytics to extract valuable insights from ERP data and optimize manufacturing operations.
Conclusion
Implementing an ERP system in the manufacturing industry is a significant undertaking, but the potential benefits are substantial. By carefully planning, selecting the right system, and addressing the challenges proactively, manufacturers can achieve significant improvements in efficiency, profitability, and customer satisfaction. The integration of data analytics further enhances the value of the ERP system, enabling data-driven decision-making and continuous optimization of manufacturing operations. The ability to leverage real-time data, predict potential problems, and proactively adapt to changing market demands ultimately positions manufacturers for sustainable success in a highly competitive global market. A well-implemented ERP system is not just a technological investment; it's a strategic imperative for achieving long-term growth and competitiveness.
Latest Posts
Latest Posts
-
Best Crm For Small Business Free
Apr 08, 2025
-
Best Crm Software For Small Business
Apr 08, 2025
-
Broker Cxm
Apr 08, 2025
-
Crm For Brokers
Apr 08, 2025
-
Insurance Broking Crm Software
Apr 08, 2025
Related Post
Thank you for visiting our website which covers about Erp Implementation In Manufacturing Industry . We hope the information provided has been useful to you. Feel free to contact us if you have any questions or need further assistance. See you next time and don't miss to bookmark.