Erp For Paint Manufacturing
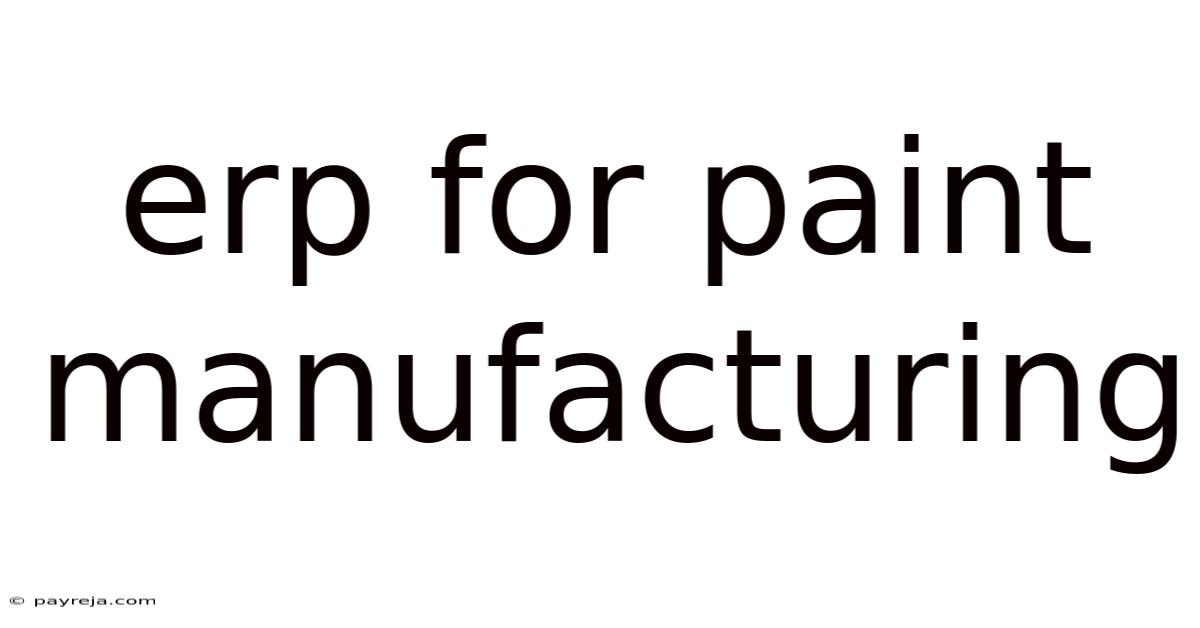
Discover more detailed and exciting information on our website. Click the link below to start your adventure: Visit Best Website meltwatermedia.ca. Don't miss out!
Table of Contents
ERP for Paint Manufacturing: Unlocking Efficiency and Growth
What if optimizing your paint manufacturing process could drastically reduce costs and boost profitability? Enterprise Resource Planning (ERP) systems are revolutionizing the paint industry, offering a streamlined approach to production, inventory, and sales.
Editor’s Note: This article on ERP for paint manufacturing was published today and offers the latest insights and best practices for the industry.
Why ERP Matters in Paint Manufacturing
The paint manufacturing industry faces unique challenges: managing complex formulations, precise color matching, stringent quality control, and fluctuating raw material prices. Traditional methods often lead to inefficiencies, inventory discrepancies, and missed production targets. ERP systems offer a centralized platform to address these challenges, improving operational efficiency, reducing costs, and enhancing overall profitability. Successful implementation allows for better inventory management, optimized production scheduling, enhanced customer relationship management (CRM), and improved financial reporting. This translates to increased competitiveness in a dynamic market. Understanding and leveraging the capabilities of an ERP system is crucial for sustainable growth and market leadership within the paint manufacturing sector.
Article Overview
This article will explore the critical aspects of implementing an ERP system in a paint manufacturing environment. We will delve into the key functionalities, discuss the integration with various business processes, analyze the impact on different departments, and address potential challenges. Readers will gain valuable insights into selecting the right ERP system, maximizing its benefits, and achieving a successful implementation. The article will also address the connection between raw material management and ERP success, examining how efficient raw material handling directly impacts the bottom line.
Research Methodology
The information presented here is based on a review of industry reports, case studies, and expert opinions from leading ERP vendors and paint manufacturing companies. We have focused on presenting clear, actionable insights, supported by credible sources to ensure accuracy and relevance.
Key Takeaways
Key Insight | Explanation |
---|---|
Improved Inventory Management | Real-time visibility into stock levels minimizes waste and prevents stockouts. |
Optimized Production Planning & Scheduling | Streamlined workflows enhance efficiency and reduce production lead times. |
Enhanced Quality Control | Comprehensive tracking of batches ensures consistent product quality and minimizes defects. |
Strengthened Customer Relationships | Improved order processing and delivery tracking leads to greater customer satisfaction and loyalty. |
Better Financial Reporting | Accurate and timely financial data provides valuable insights for strategic decision-making. |
Reduced Operational Costs | Automation of processes and minimized waste contribute to significant cost savings. |
Improved Supply Chain Visibility | Better tracking of raw materials and finished goods enhances responsiveness to market demands. |
Data-Driven Decision Making | Access to real-time data enables informed decisions based on accurate and up-to-date information. |
Core Discussion: ERP Functionality in Paint Manufacturing
Implementing an ERP system for paint manufacturing requires careful consideration of specific industry needs. Here are some key functionalities to look for:
1. Raw Material Management:
- Formulation Management: Accurately manage complex paint formulations, including precise ingredient ratios and batch-specific adjustments. The system should allow for easy modification of recipes and tracking of changes.
- Inventory Control: Real-time tracking of raw materials, including pigments, resins, solvents, and additives, ensuring sufficient stock levels while minimizing storage costs and waste.
- Supplier Management: Efficiently manage supplier relationships, track orders, and monitor delivery schedules to ensure timely procurement.
- Quality Control: Track raw material quality throughout the supply chain, ensuring compliance with standards and minimizing the risk of defects.
2. Production Planning and Control:
- Production Scheduling: Optimize production schedules based on demand forecasts, available resources, and production capacity. The system should allow for efficient batch processing and real-time adjustments.
- Manufacturing Execution System (MES) Integration: Integrate with MES systems for real-time monitoring of production processes, ensuring on-time delivery and efficient resource utilization.
- Quality Control: Track production processes and ensure adherence to quality standards throughout the manufacturing cycle.
3. Inventory Management:
- Warehouse Management: Optimize warehouse layout and operations, streamlining the movement of raw materials, work-in-progress, and finished goods.
- Lot Tracking: Track individual batches of paint throughout the entire production process, enabling traceability and facilitating recall management if necessary.
- Demand Forecasting: Utilize historical data and market trends to predict future demand, optimizing inventory levels and preventing stockouts.
4. Sales and Distribution:
- Order Management: Efficiently manage customer orders, track order status, and ensure timely delivery.
- Customer Relationship Management (CRM) Integration: Integrate with CRM systems for better customer relationship management, enabling personalized communication and improved customer service.
- Distribution Management: Optimize delivery routes and schedules, minimizing transportation costs and ensuring timely delivery of products to customers.
5. Financial Management:
- Cost Accounting: Accurately track production costs, including raw materials, labor, and overhead, to improve profitability.
- Financial Reporting: Generate comprehensive financial reports for management decision-making, providing real-time insights into the financial health of the business.
The Connection Between Raw Material Management and ERP Success
Efficient raw material management is crucial for the success of an ERP implementation in paint manufacturing. Inefficient management can lead to significant losses due to spoilage, stockouts, and production delays. An ERP system provides the tools to optimize raw material procurement, storage, and usage, minimizing waste and maximizing profitability. Real-time tracking of inventory levels, coupled with demand forecasting, ensures that sufficient materials are always available without excessive stockpiling. This translates to reduced storage costs, minimized risk of stockouts, and improved overall production efficiency.
Exploring the Connection Between Quality Control and ERP
Quality control is paramount in the paint manufacturing industry. An ERP system supports comprehensive quality control by providing detailed traceability of raw materials and finished goods. This allows for precise tracking of batches throughout the entire production process, enabling swift identification and resolution of quality issues. Moreover, the system facilitates continuous monitoring of production parameters, ensuring consistency and adherence to established quality standards. This minimizes defects, reduces waste, and enhances customer satisfaction. The integration of quality control data into the ERP system provides valuable insights for process improvement and ongoing quality enhancement.
Roles and Real-World Examples:
- Production Managers: Utilize ERP for production scheduling, real-time monitoring, and efficient resource allocation. For example, a production manager can adjust schedules based on real-time inventory data and customer demand.
- Inventory Managers: Leverage ERP for accurate inventory tracking, demand forecasting, and optimized warehouse management. A well-implemented system reduces stockouts and minimizes excess inventory.
- Sales and Marketing Teams: Utilize ERP-integrated CRM systems to manage customer relationships, track sales orders, and improve customer service. This allows for personalized communication and better response to customer inquiries.
Risks and Mitigations:
- High Implementation Costs: Thorough planning and selection of the right ERP vendor can mitigate costs.
- Data Migration Challenges: A phased approach and meticulous data cleansing can minimize disruptions.
- User Adoption Issues: Comprehensive training and change management strategies are crucial for successful adoption.
Impact and Implications:
Successful ERP implementation leads to increased efficiency, reduced costs, enhanced quality control, and improved customer satisfaction. This translates to improved profitability and a stronger competitive position in the market.
Dive Deeper into Quality Control
Effective quality control relies on several key factors:
- Raw Material Testing: Thorough testing of incoming materials ensures compliance with standards.
- In-Process Monitoring: Continuous monitoring of production parameters prevents defects.
- Finished Goods Inspection: Rigorous testing of finished products ensures consistent quality.
Quality Control Aspect | Description |
---|---|
Raw Material Inspection | Testing of incoming materials for purity, consistency, and compliance with standards. |
In-Process Quality Checks | Monitoring of production parameters to identify and address potential defects. |
Finished Goods Testing | Testing of completed products to ensure consistency and compliance with standards. |
FAQ Section:
Q1: What is the average cost of implementing an ERP system in a paint manufacturing company?
A1: The cost varies significantly depending on the size of the company, the chosen ERP solution, and the scope of implementation. It's advisable to get quotes from several vendors to determine the appropriate cost.
Q2: How long does it take to implement an ERP system?
A2: Implementation timeframes vary depending on the complexity of the system and the size of the company. It can range from several months to over a year.
Q3: What are the key benefits of using ERP in paint manufacturing?
A3: Key benefits include improved inventory management, optimized production planning, enhanced quality control, stronger customer relationships, better financial reporting, and reduced operational costs.
Q4: Can an ERP system integrate with existing systems?
A4: Yes, a well-chosen ERP system can integrate with existing systems such as CRM, MES, and other specialized software.
Q5: What are the challenges of implementing an ERP system?
A5: Challenges include high implementation costs, data migration complexities, user adoption issues, and potential disruptions to daily operations.
Q6: How can we ensure a smooth ERP implementation?
A6: A successful implementation requires thorough planning, careful selection of a vendor, comprehensive training for users, and a well-defined change management strategy.
Actionable Tips:
- Assess your current business processes: Identify areas for improvement and align your requirements with ERP functionalities.
- Choose the right ERP vendor: Select a vendor with experience in the paint manufacturing industry.
- Develop a detailed implementation plan: Outline timelines, resources, and responsibilities.
- Provide comprehensive training to users: Ensure users understand the system and are comfortable using it.
- Implement a change management strategy: Communicate effectively with stakeholders and address concerns.
- Monitor and evaluate the system regularly: Make adjustments as needed to optimize performance.
- Prioritize data integrity: Ensure accuracy and consistency of data throughout the implementation process.
- Establish key performance indicators (KPIs): Track progress and measure the impact of the ERP system.
Strong Final Conclusion:
ERP systems offer a transformative solution for paint manufacturers, enabling them to streamline operations, reduce costs, and enhance profitability. By leveraging the power of an ERP system, paint manufacturers can gain a competitive edge in a challenging market. The insights provided in this article offer a roadmap to successful implementation and long-term success in the paint manufacturing industry. Understanding the relationship between key functionalities, such as raw material management and quality control, and the overarching goals of efficiency and growth is crucial for realizing the full potential of an ERP investment. Embracing technological advancements and strategic ERP implementation is no longer a luxury, but a necessity for sustainable growth and market leadership.
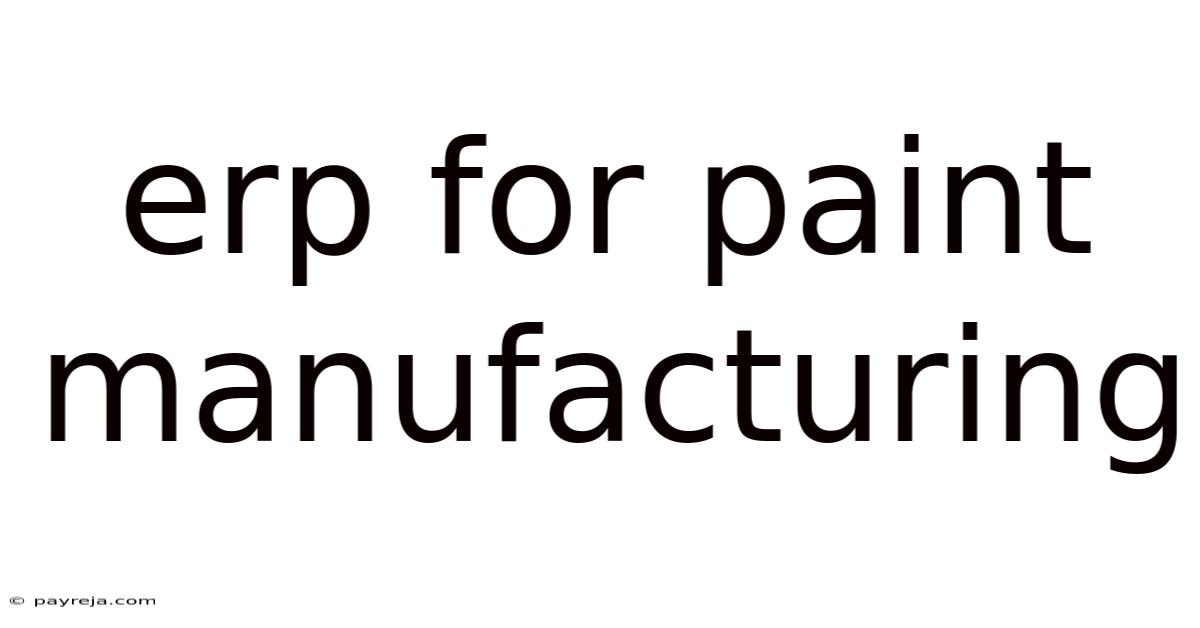
Thank you for visiting our website wich cover about Erp For Paint Manufacturing. We hope the information provided has been useful to you. Feel free to contact us if you have any questions or need further assistance. See you next time and dont miss to bookmark.
Also read the following articles
Article Title | Date |
---|---|
Chemical Erp Software | Apr 06, 2025 |
Best Erp Software Philippines | Apr 06, 2025 |
Accounting And Erp Software | Apr 06, 2025 |
Erp Protocol | Apr 06, 2025 |
Erp Projektleitung | Apr 06, 2025 |