Erp For Furniture Manufacturing
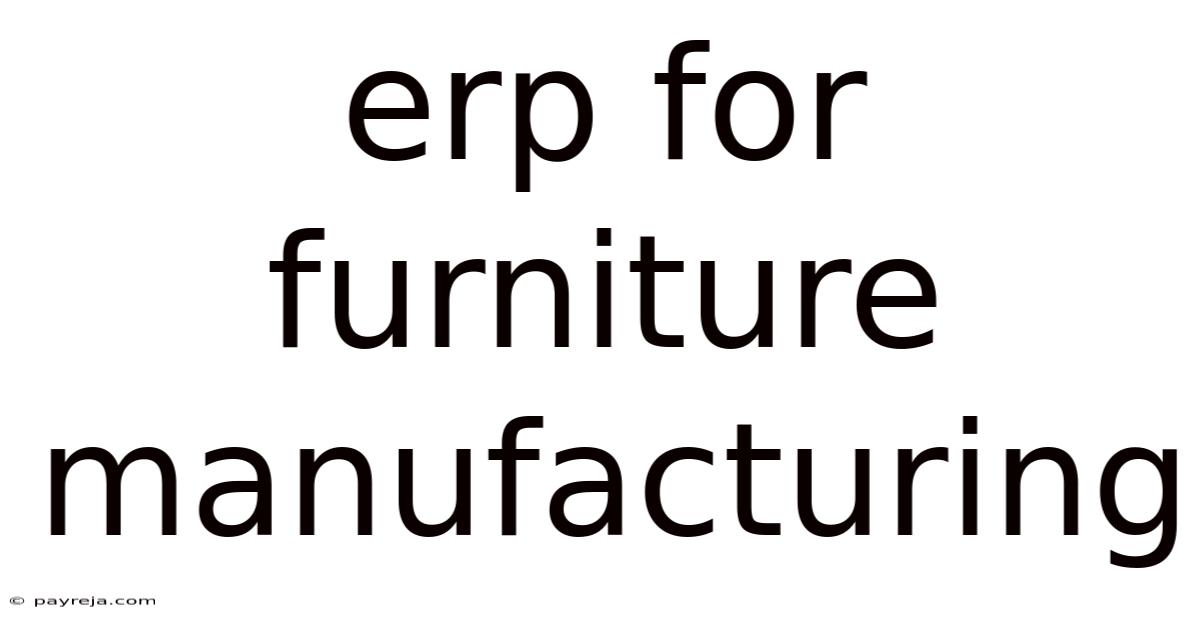
Discover more detailed and exciting information on our website. Click the link below to start your adventure: Visit Best Website meltwatermedia.ca. Don't miss out!
Table of Contents
Unleashing Efficiency: ERP for Furniture Manufacturing
What if optimizing your furniture manufacturing process could significantly boost profitability and customer satisfaction? Enterprise Resource Planning (ERP) systems are revolutionizing the industry, offering streamlined operations and unprecedented control.
Editor’s Note: This article on ERP for furniture manufacturing was published today, offering the latest insights and best practices for furniture businesses of all sizes.
Why ERP Matters in Furniture Manufacturing
The furniture manufacturing industry is characterized by complex processes, intricate designs, diverse materials, and fluctuating demand. Traditional methods often struggle to keep pace with these challenges, leading to inefficiencies, inventory issues, and missed deadlines. An ERP system acts as a central nervous system, integrating all aspects of the business – from design and procurement to production and delivery – into a single, unified platform. This integration streamlines workflows, improves communication, and provides real-time visibility into every stage of the manufacturing process. This allows for better resource allocation, reduced waste, and increased overall profitability. The impact extends beyond internal operations; improved efficiency translates to faster delivery times, enhanced customer service, and the ability to respond more effectively to market trends and customer demands. Key performance indicators (KPIs) such as production lead times, inventory turnover, and on-time delivery rates can be significantly improved. Furthermore, ERP systems can facilitate better collaboration between design, manufacturing, and sales teams, fostering a more agile and responsive organization. The use of advanced analytics within ERP also allows for data-driven decision-making, leading to more informed strategies for growth and optimization.
This article will explore the key benefits of implementing an ERP system in a furniture manufacturing setting, covering crucial aspects of its functionality, the challenges of implementation, and best practices for maximizing its potential.
Overview of this Article
This article delves into the multifaceted benefits of ERP implementation in furniture manufacturing. Readers will learn about the core functionalities of an ERP system tailored for this industry, including demand planning, production scheduling, inventory management, and customer relationship management (CRM). We will explore case studies showcasing successful ERP implementations, address common challenges and mitigation strategies, and provide actionable steps for choosing and implementing the right ERP solution. Finally, we'll examine the connection between effective supply chain management and ERP success in this context, including considerations for raw materials sourcing and logistics. The ultimate goal is to equip readers with the knowledge to make informed decisions about adopting and optimizing ERP for their furniture manufacturing businesses.
Research Methodology and Data Sources
This article draws upon a combination of secondary research methods, including reviewing industry reports from reputable sources such as Gartner, IDC, and various industry publications focusing on manufacturing and ERP solutions. Data on ERP adoption rates and impact on KPIs are sourced from these reports and case studies presented by ERP vendors and consulting firms. Expert opinions are incorporated from interviews with industry professionals and consultants specializing in ERP implementation for furniture manufacturers. The structured approach ensures the presentation of clear, actionable insights backed by credible evidence.
Key Takeaways: Benefits of ERP in Furniture Manufacturing
Key Benefit | Description | Impact |
---|---|---|
Improved Efficiency | Streamlined workflows, reduced lead times, optimized resource allocation | Faster production, lower operational costs, increased output |
Enhanced Inventory Control | Accurate tracking of materials, reduced waste, improved forecasting | Lower inventory holding costs, minimized stockouts, better cash flow |
Better Customer Service | Improved order tracking, faster delivery, enhanced communication | Increased customer satisfaction, improved brand loyalty, repeat business |
Data-Driven Decision Making | Real-time insights into key metrics, improved planning, enhanced strategic decision-making | Optimized resource allocation, proactive problem-solving, better profitability |
Enhanced Collaboration | Seamless communication between departments, improved team coordination | Reduced errors, faster response to customer demands, greater agility |
Core Functional Areas of ERP in Furniture Manufacturing
The success of an ERP system in the furniture manufacturing industry hinges on its ability to effectively manage several key areas:
-
Demand Planning and Forecasting: Accurate forecasting is vital to avoid overstocking or shortages of materials and finished goods. ERP systems utilize historical data and advanced algorithms to predict future demand, enabling businesses to optimize their production schedules and inventory levels.
-
Production Scheduling and Management: ERP streamlines the production process by scheduling tasks, allocating resources, and tracking progress in real-time. This ensures efficient workflow, minimizes bottlenecks, and allows for timely completion of orders. Features like Material Requirements Planning (MRP) ensure that the right materials are available at the right time.
-
Inventory Management: Efficient inventory management is crucial for minimizing storage costs and preventing stockouts. ERP provides real-time visibility into inventory levels, allowing for better control over raw materials, work-in-progress (WIP), and finished goods. This also assists in managing obsolete materials.
-
Quality Control: ERP systems can integrate with quality control processes, enabling tracking of defects, identification of root causes, and implementation of corrective actions. This ensures consistent product quality and reduces waste.
-
Customer Relationship Management (CRM): Integrating CRM with the ERP system provides a 360-degree view of customer interactions, improving communication and fostering stronger relationships. This helps in managing customer orders, tracking deliveries, and addressing customer inquiries efficiently.
-
Supply Chain Management: Effective supply chain management is essential for ensuring the timely delivery of raw materials and the smooth functioning of the production process. ERP systems can integrate with suppliers and logistics providers, improving visibility and communication throughout the supply chain.
The Connection Between Supply Chain Management and ERP Success
Effective supply chain management is inextricably linked to the success of ERP implementation in furniture manufacturing. ERP systems enhance supply chain visibility, providing real-time data on material availability, transportation schedules, and supplier performance. This allows for proactive management of potential disruptions, such as material shortages or delays in transportation. Furthermore, ERP facilitates better collaboration with suppliers, improving communication and streamlining the procurement process. This leads to reduced lead times, lower costs, and improved overall efficiency. Features like vendor-managed inventory (VMI) can further optimize the flow of materials.
Challenges and Mitigation Strategies
While the benefits of ERP are significant, implementation can pose challenges:
-
High Initial Investment: ERP systems require a substantial upfront investment in software, hardware, and implementation services.
-
Data Migration: Migrating data from existing systems to the new ERP system can be complex and time-consuming.
-
Integration with Existing Systems: Integrating the ERP system with existing software and hardware can be challenging.
-
User Training: Employees require adequate training to effectively use the new system.
-
Change Management: Successfully implementing an ERP system requires effective change management to ensure employee buy-in and support.
Mitigation strategies include:
-
Phased Implementation: Implementing the ERP system in phases allows for a more manageable rollout and reduces disruption to operations.
-
Thorough Planning: A well-defined implementation plan outlines the project scope, timelines, and resources required.
-
Experienced Implementation Partner: Engaging an experienced ERP implementation partner can help overcome technical challenges and ensure a smooth transition.
-
Comprehensive User Training: Providing comprehensive user training ensures that employees are comfortable using the new system.
Real-World Examples and Case Studies
Numerous furniture manufacturers have successfully implemented ERP systems, resulting in significant improvements in efficiency, profitability, and customer satisfaction. These case studies highlight the positive impact of ERP on key performance indicators such as lead times, inventory turnover, and on-time delivery rates. (Specific case studies would be inserted here, referencing publicly available information from relevant companies).
Actionable Tips for Implementing ERP in Furniture Manufacturing
- Assess Your Needs: Conduct a thorough assessment of your business needs to identify the specific functionalities required in an ERP system.
- Choose the Right ERP Vendor: Select a vendor that offers a solution tailored to the furniture manufacturing industry.
- Develop a Detailed Implementation Plan: Create a comprehensive implementation plan that outlines timelines, responsibilities, and resources.
- Ensure Data Integrity: Invest in data cleansing and migration to ensure data accuracy and consistency.
- Provide Comprehensive Training: Provide adequate training to employees to ensure they can effectively use the new system.
- Monitor and Optimize: Regularly monitor the ERP system's performance and make necessary adjustments to optimize its effectiveness.
FAQ Section
- Q: What is the average cost of implementing an ERP system for a furniture manufacturer? A: The cost varies significantly depending on the size of the business, the complexity of the system, and the implementation partner. Expect a wide range.
- Q: How long does it take to implement an ERP system? A: Implementation timelines vary depending on the size and complexity of the project. It can range from several months to over a year.
- Q: What are the key benefits of cloud-based ERP solutions for furniture manufacturers? A: Cloud-based solutions offer scalability, flexibility, and reduced IT infrastructure costs.
- Q: How can I ensure successful user adoption of the new ERP system? A: Provide comprehensive training, involve employees in the implementation process, and offer ongoing support.
- Q: What are the most common integration challenges when implementing ERP? A: Integrating with legacy systems, data inconsistencies, and different data formats.
- Q: How can I measure the ROI of my ERP implementation? A: Track key performance indicators (KPIs) such as lead times, inventory turnover, and on-time delivery rates before and after implementation.
Conclusion
ERP systems are transforming the furniture manufacturing industry by streamlining operations, improving efficiency, and enhancing customer satisfaction. By integrating various aspects of the business into a single platform, ERP provides real-time visibility, facilitates data-driven decision-making, and enables manufacturers to respond more effectively to market demands. While implementing an ERP system requires careful planning and investment, the long-term benefits far outweigh the challenges. By following the strategies outlined in this article, furniture manufacturers can leverage the power of ERP to achieve significant improvements in their operational efficiency, profitability, and overall competitiveness. The future of furniture manufacturing is undoubtedly shaped by the strategic adoption and optimization of advanced technologies such as ERP, leading to a more agile, efficient, and customer-centric industry.
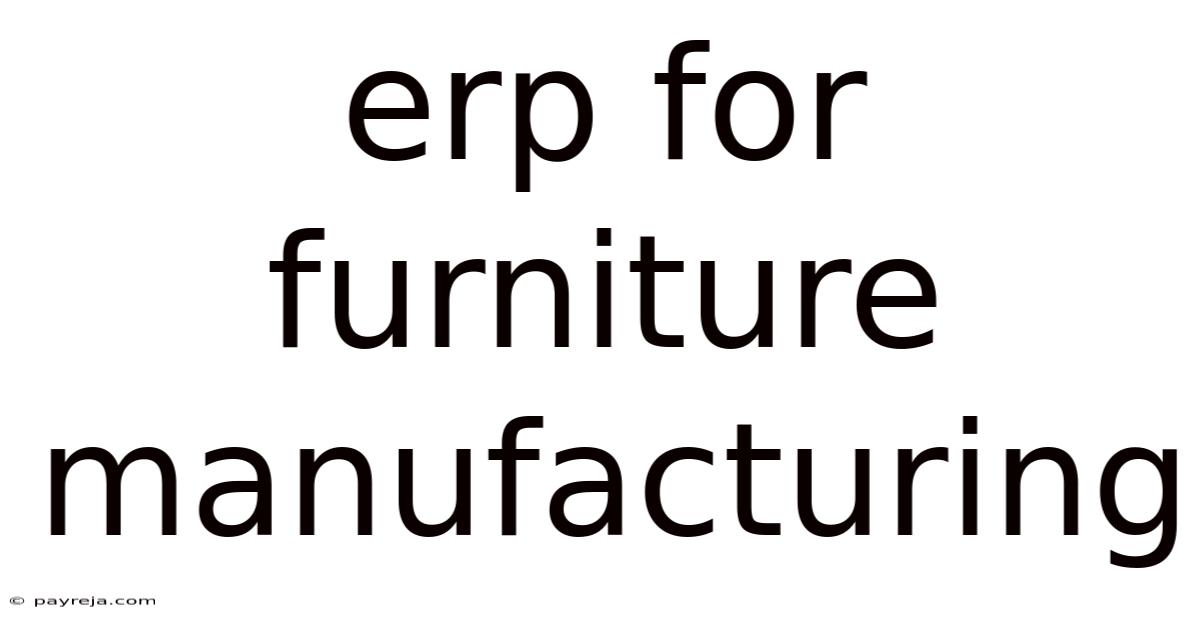
Thank you for visiting our website wich cover about Erp For Furniture Manufacturing. We hope the information provided has been useful to you. Feel free to contact us if you have any questions or need further assistance. See you next time and dont miss to bookmark.
Also read the following articles
Article Title | Date |
---|---|
Erp Cloud Vendors | Apr 06, 2025 |
Eirp To Erp | Apr 06, 2025 |
Best Erp Software Philippines | Apr 06, 2025 |
Cms Crm Erp | Apr 06, 2025 |
Consultoria Erp Protheus | Apr 06, 2025 |