Erp For Furniture Industry
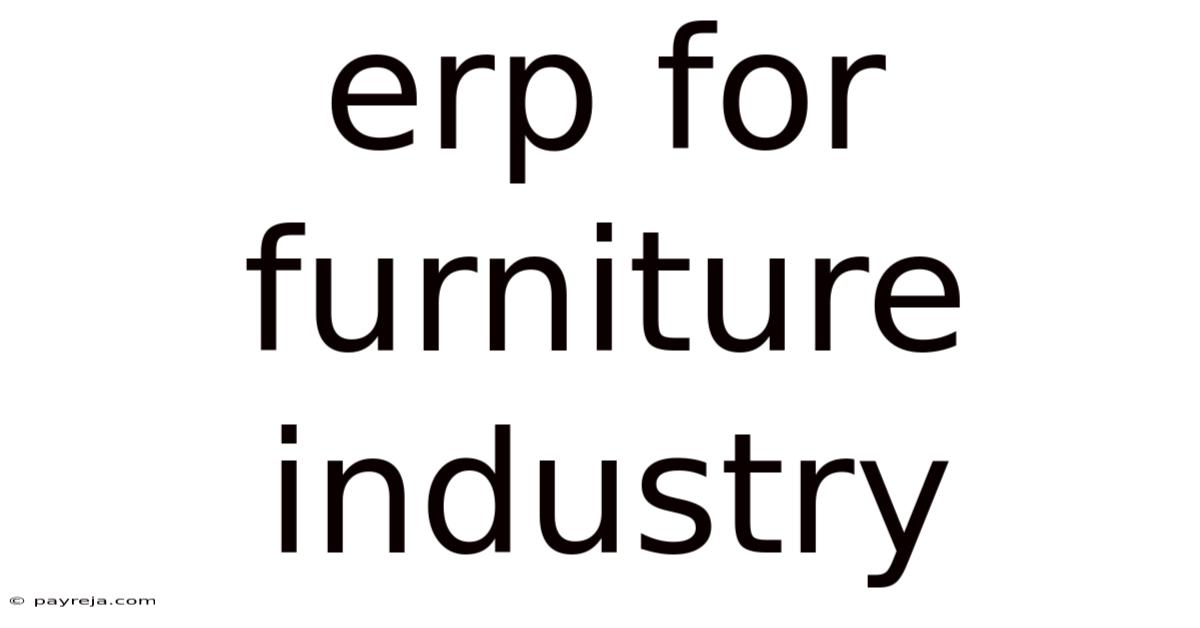
Discover more detailed and exciting information on our website. Click the link below to start your adventure: Visit Best Website meltwatermedia.ca. Don't miss out!
Table of Contents
Unleashing Growth: ERP for the Furniture Industry
What if optimizing your furniture business operations could unlock unprecedented growth and efficiency? Enterprise Resource Planning (ERP) systems are revolutionizing the furniture industry, streamlining processes and driving profitability.
Editor’s Note: This article on ERP for the furniture industry was published today, offering the latest insights and best practices.
The furniture industry, known for its intricate manufacturing processes, complex supply chains, and diverse product offerings, faces unique challenges in today's competitive market. Managing inventory, tracking production, and coordinating sales across multiple channels can be overwhelming. Enter Enterprise Resource Planning (ERP) systems – powerful tools designed to integrate and optimize all aspects of a business, from design and manufacturing to sales and distribution. This article explores the crucial role ERP plays in boosting efficiency, profitability, and overall success within the dynamic furniture sector.
This article will cover key topics such as selecting the right ERP system, integrating various modules, managing inventory effectively, streamlining production, optimizing supply chain management, improving customer relationship management (CRM), enhancing financial management, and leveraging reporting and analytics for data-driven decision-making. Readers will gain valuable insights into how ERP can transform their furniture businesses, leading to improved operational efficiency, increased sales, and enhanced customer satisfaction.
Why ERP Matters for Furniture Businesses
The furniture industry, encompassing diverse segments from custom-made pieces to mass-produced items, requires sophisticated management. Traditional methods often struggle to cope with the complexities of:
- Complex Bill of Materials (BOM): Furniture often involves numerous components and variations, making accurate BOM management crucial for efficient production.
- Varied Production Processes: Manufacturing processes can vary significantly depending on the type of furniture (e.g., handcrafted vs. mass-produced), requiring flexible systems.
- Long Lead Times: Furniture production often involves lengthy lead times, demanding careful planning and inventory management.
- Demand Fluctuations: Seasonal trends and changing consumer preferences can lead to significant fluctuations in demand, necessitating agile production and inventory control.
- High Inventory Costs: Storing raw materials, work-in-progress (WIP), and finished goods can be expensive, requiring optimized inventory management strategies.
- Customer Customization: Many furniture businesses offer customization options, demanding robust order management and production tracking systems.
ERP systems address these challenges by providing a centralized platform to manage all aspects of the business, improving communication, reducing errors, and facilitating data-driven decision-making. The integration of various modules – from sales and marketing to finance and manufacturing – ensures seamless data flow and minimizes manual processes.
Selecting the Right ERP System
Choosing the right ERP system is a crucial decision. Businesses should consider factors like:
- Business Size and Complexity: The scale and complexity of the furniture business will influence the required features and functionalities of the ERP system.
- Budget: ERP systems range in price, depending on the features, modules, and implementation costs.
- Industry-Specific Features: Look for systems with features tailored to the furniture industry, such as BOM management, production scheduling, and inventory control for diverse materials.
- Scalability and Flexibility: Choose a system that can adapt to future growth and changes in business needs.
- Integration Capabilities: The ability to integrate with existing systems (e.g., CRM, e-commerce platforms) is essential.
- Vendor Support and Training: Reliable vendor support and comprehensive training are crucial for successful implementation and ongoing operation.
Core Modules and Their Impact
A comprehensive ERP system for the furniture industry typically includes the following key modules:
- Sales and Marketing: Efficient order processing, customer relationship management (CRM), and marketing campaign management.
- Production Planning and Scheduling: Optimized production schedules based on demand, resource availability, and lead times. This includes managing work orders, tracking progress, and allocating resources effectively.
- Inventory Management: Real-time tracking of raw materials, WIP, and finished goods, minimizing stockouts and excess inventory. Effective management of various materials like wood, fabric, and hardware is critical.
- Supply Chain Management: Streamlined procurement, efficient vendor management, and improved logistics. This includes managing relationships with suppliers and optimizing transportation.
- Financial Management: Accurate accounting, financial reporting, and budgeting capabilities. This provides crucial insight into profitability, cash flow, and overall financial health.
- Customer Relationship Management (CRM): Integrated customer data, enabling personalized interactions and improved customer service.
- Project Management: Effective management of custom furniture projects, tracking progress and ensuring timely delivery.
Streamlining Production with ERP
ERP systems significantly enhance production efficiency in the furniture industry. Features like:
- Automated Work Orders: Reduce manual data entry and minimize errors.
- Real-time Production Tracking: Monitor production progress and identify bottlenecks.
- Resource Allocation: Optimize the allocation of machinery, personnel, and materials.
- Quality Control Integration: Track quality control metrics and identify areas for improvement.
These features, combined with robust BOM management, minimize waste, reduce lead times, and improve overall production output.
Optimizing the Supply Chain
Effective supply chain management is vital in the furniture industry, where sourcing raw materials and managing logistics can be complex. ERP systems offer:
- Vendor Management: Centralized management of vendor information, purchase orders, and delivery schedules.
- Procurement Optimization: Negotiate better pricing and ensure timely delivery of materials.
- Logistics Management: Track shipments, optimize transportation routes, and minimize delivery delays.
Improved supply chain management reduces costs, improves delivery times, and enhances customer satisfaction.
Enhancing Financial Management
Financial management is crucial for the success of any furniture business. ERP systems provide:
- Real-time Financial Reporting: Accurate and up-to-date financial information, allowing for timely decision-making.
- Improved Budgeting and Forecasting: More accurate predictions of revenue and expenses.
- Cost Accounting: Track production costs and identify areas for cost reduction.
This enhanced financial visibility strengthens business stability and supports strategic planning.
Leveraging Reporting and Analytics
ERP systems generate valuable data that can be used to improve business decisions. Features like:
- Customizable Dashboards: Visualize key performance indicators (KPIs) and monitor business performance.
- Advanced Reporting: Generate detailed reports on sales, production, inventory, and financials.
- Predictive Analytics: Forecast demand, optimize production schedules, and improve inventory management.
Data-driven insights enable proactive adjustments and strategic improvements.
Key Takeaways
Insight | Description |
---|---|
Enhanced Efficiency | Streamlined processes, reduced manual work, and improved productivity across departments. |
Improved Accuracy | Minimized errors in order processing, production scheduling, and inventory management. |
Better Inventory Control | Optimized inventory levels, reduced stockouts, and minimized storage costs. |
Stronger Supply Chain Management | Improved vendor relationships, efficient procurement, and streamlined logistics. |
Enhanced Customer Satisfaction | Faster order fulfillment, improved communication, and better customer service. |
Increased Profitability | Reduced costs, improved efficiency, and optimized resource allocation. |
Data-Driven Decision Making | Real-time insights and advanced analytics empower data-informed strategies. |
Scalability and Flexibility | Adaptable systems that grow with the business and accommodate future needs. |
The Interplay Between CRM and ERP in the Furniture Industry
Customer Relationship Management (CRM) plays a crucial role in enhancing the effectiveness of an ERP system within the furniture industry. A well-integrated CRM system complements the ERP's operational capabilities by providing a comprehensive view of customer interactions, preferences, and purchasing history. This allows for:
- Personalized Customer Service: CRM data enables sales teams to provide tailored service, addressing individual customer needs and preferences. This is particularly important in the furniture industry where customization is common.
- Targeted Marketing Campaigns: By analyzing customer data, businesses can create targeted marketing campaigns that resonate with specific customer segments.
- Improved Sales Forecasting: Predictive analytics based on CRM data enhances sales forecasting accuracy, enabling better inventory planning and resource allocation.
- Efficient Order Management: Seamless integration between CRM and ERP ensures efficient order processing, tracking, and delivery.
A well-integrated CRM system enhances the value of an ERP by creating a holistic view of the customer journey, improving communication, and enhancing the overall customer experience. For instance, a CRM system can track customer interactions from initial inquiry to post-sale support, providing valuable feedback for product development and improvement.
Risks and Mitigations
Implementing an ERP system involves potential risks, including:
- High Initial Investment: ERP implementation can be expensive, including software costs, consulting fees, and training expenses.
- Integration Challenges: Integrating different systems and data sources can be complex.
- Change Management: Resistance to change from employees accustomed to old processes is a common hurdle.
- Data Migration Issues: Transferring data from existing systems to the new ERP system can be challenging.
These risks can be mitigated through careful planning, thorough research, effective project management, and comprehensive employee training. Choosing a reputable vendor with strong implementation support is crucial.
Impact and Implications
The long-term impact of ERP implementation in the furniture industry is significant. Businesses can expect:
- Improved Competitiveness: Enhanced efficiency and customer satisfaction help businesses stand out in a crowded market.
- Increased Revenue and Profitability: Improved operations and streamlined processes contribute to greater profitability.
- Enhanced Business Growth: Optimized processes and better decision-making facilitate growth and expansion.
Diving Deeper into CRM Integration
The effective integration of CRM with an ERP system requires careful consideration of data synchronization, process automation, and user training. Key aspects of successful integration include:
- Real-time Data Synchronization: Ensuring that customer data is updated seamlessly across both systems, providing a unified view of customer interactions.
- Automated Workflows: Automating tasks such as order processing, lead generation, and customer communication.
- Unified User Interface: Creating a user-friendly interface that streamlines access to both CRM and ERP data.
- Customizable Dashboards and Reports: Creating customized dashboards that provide key performance indicators (KPIs) for both sales and operations.
A well-integrated CRM and ERP system creates a powerful synergy, improving overall business efficiency, strengthening customer relationships, and driving sustainable growth.
Frequently Asked Questions (FAQ)
Q1: What is the average cost of implementing an ERP system for a furniture business?
A1: The cost varies significantly based on the size of the business, the chosen ERP system, the level of customization, and the scope of implementation. It's essential to get detailed quotes from multiple vendors.
Q2: How long does it typically take to implement an ERP system?
A2: Implementation timelines vary, depending on the complexity of the system and the size of the business. It can range from several months to over a year.
Q3: What are the key benefits of using an ERP system for a small furniture business?
A3: Even small businesses can benefit from improved inventory management, streamlined order processing, and better financial visibility. This can lead to increased efficiency, reduced costs, and improved customer satisfaction.
Q4: Can an ERP system help with managing custom orders?
A4: Yes, ERP systems can effectively manage custom orders by tracking specific requirements, managing production schedules, and ensuring timely delivery.
Q5: How can an ERP system improve supply chain visibility?
A5: ERP systems provide real-time visibility into the entire supply chain, from raw material sourcing to finished goods delivery, helping to identify potential bottlenecks and optimize logistics.
Q6: What are the essential features to look for when selecting an ERP system for the furniture industry?
A6: Essential features include robust BOM management, production scheduling, inventory control for diverse materials, and integrated CRM capabilities.
Actionable Tips for Implementing ERP
- Assess Business Needs: Thoroughly analyze business processes to identify areas for improvement and determine the required ERP functionalities.
- Choose the Right Vendor: Select a vendor with proven experience in the furniture industry and strong implementation support.
- Develop a Detailed Implementation Plan: Create a comprehensive plan with clear timelines, milestones, and responsibilities.
- Provide Comprehensive Employee Training: Ensure employees receive adequate training to use the new system effectively.
- Monitor and Optimize: Continuously monitor system performance and make adjustments to optimize processes and enhance efficiency.
- Integrate with Existing Systems: Ensure seamless integration with existing CRM, e-commerce platforms, and other relevant systems.
- Consider Cloud-Based Solutions: Cloud-based ERP systems offer scalability, flexibility, and reduced IT infrastructure costs.
- Embrace Change Management: Communicate effectively with employees, address their concerns, and foster a culture of acceptance and collaboration.
Conclusion
Implementing an ERP system represents a significant investment, but the long-term benefits far outweigh the initial costs. For furniture businesses of all sizes, ERP systems offer a powerful solution for streamlining operations, optimizing supply chains, improving customer relationships, and driving sustainable growth. By carefully selecting the right system and implementing it effectively, furniture businesses can unlock new levels of efficiency, profitability, and competitiveness in today's dynamic market. The future of the furniture industry lies in leveraging technology to enhance operations and deliver exceptional customer experiences. Embracing ERP is a crucial step in achieving this vision.
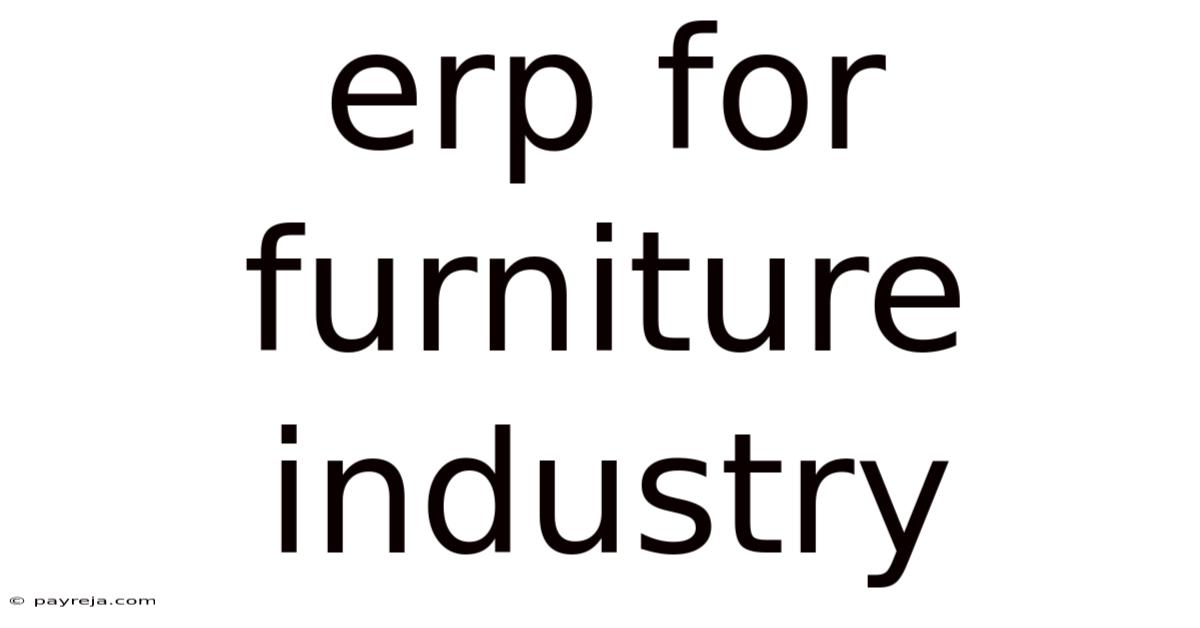
Thank you for visiting our website wich cover about Erp For Furniture Industry. We hope the information provided has been useful to you. Feel free to contact us if you have any questions or need further assistance. See you next time and dont miss to bookmark.
Also read the following articles
Article Title | Date |
---|---|
Effi Erp | Apr 06, 2025 |
Erp Chat Bot | Apr 06, 2025 |
Erp Energiateollisuuteen | Apr 06, 2025 |
Erp Integration Specialist | Apr 06, 2025 |
Erp For Hocd | Apr 06, 2025 |