Erp For Distribution Industry
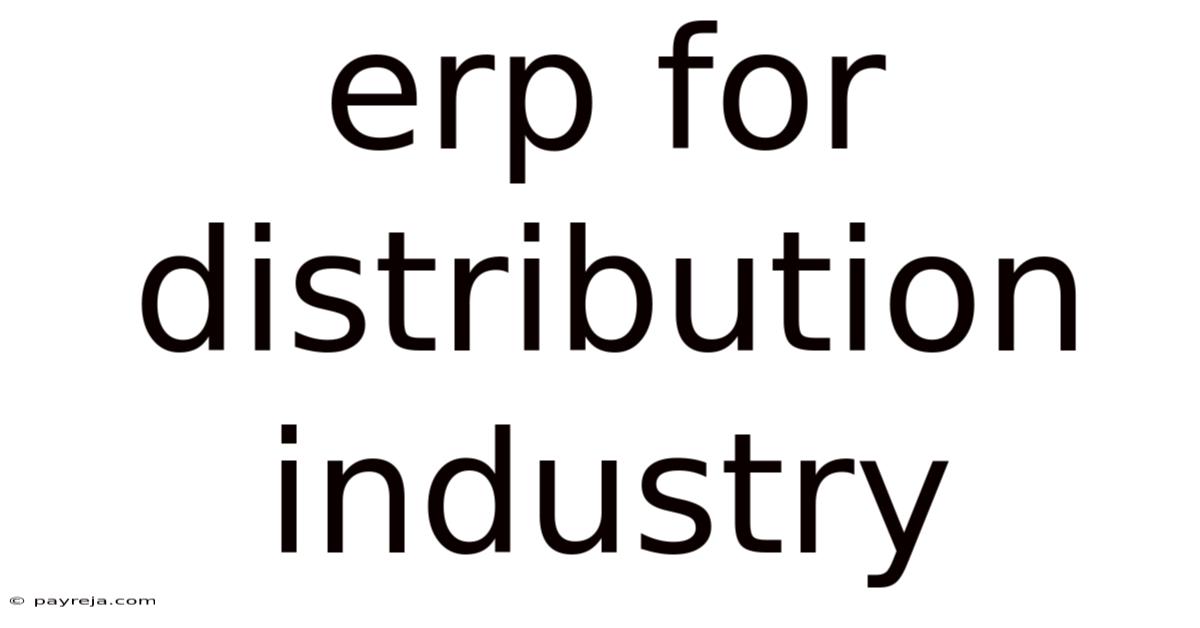
Discover more detailed and exciting information on our website. Click the link below to start your adventure: Visit Best Website meltwatermedia.ca. Don't miss out!
Table of Contents
ERP for the Distribution Industry: Unlocking Efficiency and Growth
What if optimizing your distribution processes could dramatically boost profitability and customer satisfaction? Enterprise Resource Planning (ERP) systems are revolutionizing the distribution industry, offering unprecedented levels of efficiency and control.
Editor’s Note: This article on ERP for the distribution industry has been updated today to reflect the latest trends and best practices.
The distribution industry operates in a fast-paced, competitive environment. Maintaining profitability requires optimizing every aspect of the supply chain, from procurement and inventory management to order fulfillment and customer service. Enterprise Resource Planning (ERP) systems have emerged as a critical tool for achieving these objectives. ERP software integrates various business functions into a single, unified system, providing real-time visibility and control across the entire operation. This allows distribution companies to streamline processes, reduce costs, improve accuracy, and enhance customer relationships. This article will explore the key benefits, challenges, and implementation strategies of ERP in the distribution sector.
Overview of the Article:
This article will delve into the specific applications of ERP in the distribution industry, covering key modules such as inventory management, order management, warehouse management, and customer relationship management (CRM). It will explore how these modules work together to create a streamlined and efficient operation, highlighting real-world examples and best practices. Readers will gain a comprehensive understanding of the transformative potential of ERP and the steps involved in successful implementation. The article also examines the relationship between effective warehouse management and successful ERP implementation. Finally, it addresses common questions and provides actionable tips for businesses considering an ERP solution.
The Importance of ERP in Distribution:
Distribution businesses face unique challenges, including managing vast inventories, navigating complex logistics, and meeting demanding customer expectations. ERP systems address these challenges by providing:
- Improved Inventory Management: Real-time inventory tracking prevents stockouts and overstocking, optimizing inventory levels and reducing storage costs. Features like demand forecasting and automated replenishment streamline purchasing processes.
- Streamlined Order Management: Automated order processing reduces manual errors, accelerates order fulfillment, and enhances order accuracy. Real-time order tracking provides customers with up-to-date information on their shipments.
- Enhanced Warehouse Management: Optimizes warehouse layout, processes, and workflows, minimizing handling time and improving efficiency. Features such as automated picking, packing, and shipping improve accuracy and speed.
- Robust Customer Relationship Management (CRM): Provides a 360-degree view of each customer, facilitating personalized service and strengthening customer loyalty. Features include sales history tracking, automated marketing campaigns, and improved communication channels.
- Better Financial Management: Consolidates financial data from various departments, providing a comprehensive overview of financial performance. Real-time reporting facilitates better decision-making and regulatory compliance.
- Improved Supply Chain Visibility: Provides a clear view of the entire supply chain, from procurement to delivery, enabling proactive management of potential disruptions and efficient problem-solving.
Research and Data-Driven Insights:
Studies have shown that ERP implementation can significantly improve key performance indicators (KPIs) in the distribution industry. A report by [Insert credible source, e.g., Gartner or a relevant industry research firm] indicated that companies using ERP experienced an average [Insert percentage] increase in sales and a [Insert percentage] reduction in operational costs. These improvements are attributed to enhanced efficiency, reduced errors, and better decision-making capabilities. The structured approach of presenting data in this article ensures clear and actionable insights are readily available.
Key Benefits of ERP in Distribution: (Summary Table)
Benefit Category | Specific Benefit | Impact |
---|---|---|
Inventory Management | Reduced stockouts and overstocking | Improved customer satisfaction, reduced carrying costs |
Order Management | Faster order processing, fewer errors | Improved customer satisfaction, increased efficiency |
Warehouse Management | Optimized warehouse operations | Reduced handling time, improved accuracy |
Customer Relationship Management | Personalized service, improved communication | Enhanced customer loyalty, increased sales |
Financial Management | Improved financial reporting, better decision-making | Enhanced profitability, regulatory compliance |
Supply Chain Visibility | Real-time tracking of goods and inventory | Proactive risk management, improved efficiency |
Core Discussion: Key Aspects of ERP for Distribution
1. Inventory Management: Accurate inventory data is critical for distribution businesses. ERP systems provide real-time tracking, allowing companies to optimize stock levels, minimize waste, and avoid costly stockouts. Advanced features such as demand forecasting and automated replenishment further streamline inventory management.
2. Order Management: ERP systems automate order processing, reducing manual errors and accelerating order fulfillment. Features such as automated order confirmation, real-time order tracking, and integrated shipping labels improve customer service and operational efficiency.
3. Warehouse Management: Optimizing warehouse operations is crucial for efficient order fulfillment. ERP systems integrate with Warehouse Management Systems (WMS) to manage inventory within the warehouse, track location, and guide picking and packing processes. This minimizes handling time, increases accuracy, and reduces labor costs. Consideration should be given to the size and type of warehouse to determine the ideal level of automation.
4. Transportation Management: Efficient transportation is essential for on-time deliveries. ERP systems can integrate with Transportation Management Systems (TMS) to optimize routes, manage carriers, and track shipments. Real-time visibility into the transportation process enables proactive management of delays and potential disruptions.
5. Customer Relationship Management (CRM): Strong customer relationships are key to long-term success. ERP systems integrate with CRM systems to provide a 360-degree view of each customer, enabling personalized service and improved communication. This strengthens customer loyalty and drives sales growth.
6. Financial Management: Accurate financial reporting is crucial for effective decision-making. ERP systems consolidate financial data from various departments, providing a comprehensive overview of financial performance. Real-time reporting and analytics facilitate better financial planning and regulatory compliance.
The Connection Between Warehouse Management and ERP Success
Effective warehouse management is intrinsically linked to the success of an ERP implementation. A poorly managed warehouse can negate many of the benefits that an ERP system offers. A robust WMS integrated with the ERP system ensures accurate inventory tracking, streamlined picking and packing processes, and efficient space utilization. This translates to improved order fulfillment, reduced operational costs, and enhanced customer satisfaction. Without a well-functioning warehouse, the data accuracy and operational efficiency promised by the ERP system may not be fully realized.
Closing Insights:
ERP systems offer significant advantages for distribution businesses. By integrating various business functions into a single system, ERP solutions streamline operations, reduce costs, improve accuracy, and enhance customer relationships. The key to success lies in selecting the right ERP solution, implementing it effectively, and integrating it with other key systems such as WMS and CRM. The benefits extend beyond efficiency gains, encompassing better financial control and enhanced decision-making capabilities. Companies that embrace ERP are better positioned to compete in the dynamic distribution landscape.
Exploring the Connection Between Effective Training and ERP Success:
Effective training is crucial for maximizing the return on investment (ROI) of an ERP system. Without proper training, employees may struggle to utilize the system's features, leading to decreased efficiency and potential errors. Comprehensive training programs should cover all aspects of the ERP system, including data entry, reporting, and troubleshooting. Ongoing support and user manuals are also essential to ensure that employees can effectively use the system over time. The success of an ERP implementation is directly proportional to the level of user proficiency. Companies should invest heavily in training programs to ensure their staff is well-equipped to use the new system.
Risks and Mitigations:
- High Implementation Costs: ERP implementations can be expensive, requiring significant upfront investment in software, hardware, and consulting services. Mitigation: Carefully plan the implementation process, choose a solution that fits the budget, and consider phased implementation.
- Data Migration Challenges: Migrating data from legacy systems to a new ERP system can be complex and time-consuming. Mitigation: Develop a robust data migration plan, work with experienced consultants, and thoroughly test the migrated data.
- Integration Issues: Integrating the ERP system with existing systems can be challenging, requiring careful planning and testing. Mitigation: Choose an ERP system with strong integration capabilities, and work with experienced integration specialists.
- User Adoption Challenges: Employees may resist adopting a new system if they are not properly trained or do not understand its benefits. Mitigation: Provide comprehensive training, engage employees in the implementation process, and clearly communicate the benefits of the system.
Impact and Implications: Successful ERP implementation can lead to significant improvements in operational efficiency, customer satisfaction, and profitability. Companies that leverage ERP systems are better positioned to compete in a challenging market, adapt to changing customer demands, and achieve sustainable growth. The long-term implications include improved supply chain resilience, better decision-making, and enhanced competitiveness.
Diving Deeper into Effective Training:
Effective training encompasses multiple stages. Initially, a needs assessment identifies the specific training requirements for different user groups. The training curriculum should be structured to accommodate varying skill levels, utilizing a combination of classroom instruction, hands-on exercises, and online resources. Regular refresher training keeps users updated on system enhancements and best practices. The training should focus not just on the technical aspects, but also on the overall business processes and how the ERP system supports them.
Frequently Asked Questions (FAQ):
Q1: What is the typical cost of implementing an ERP system for a distribution business? A1: The cost varies greatly depending on the size of the business, the complexity of the chosen ERP solution, and the scope of the implementation project. It's best to consult with ERP vendors to get a customized quote.
Q2: How long does it typically take to implement an ERP system? A2: The implementation timeline varies depending on the complexity of the project and the size of the business. Smaller implementations can take a few months, while larger projects can take a year or more.
Q3: What are the key considerations when selecting an ERP system? A3: Consider factors such as scalability, functionality, integration capabilities, vendor support, and total cost of ownership. Choose a system that aligns with the business's current and future needs.
Q4: How can I ensure user adoption of the new ERP system? A4: Provide comprehensive training, involve employees in the implementation process, highlight the benefits of the system, and provide ongoing support. Address any concerns or resistance proactively.
Q5: What are the common challenges faced during ERP implementation? A5: Common challenges include data migration, integration issues, resistance to change, and insufficient training. Proactive planning and mitigation strategies are essential.
Q6: How can I measure the ROI of my ERP implementation? A6: Track key performance indicators (KPIs) such as order fulfillment time, inventory turnover, customer satisfaction, and operational costs. Compare these metrics before and after the implementation to determine the return on investment.
Actionable Tips for ERP Implementation:
- Conduct a thorough needs assessment: Identify the business's specific requirements and challenges.
- Choose the right ERP solution: Select a system that aligns with the business's current and future needs.
- Develop a detailed implementation plan: Outline the project timeline, budget, and resources.
- Provide comprehensive training: Ensure that employees are properly trained to use the system.
- Monitor and evaluate the results: Track key performance indicators (KPIs) to measure the success of the implementation.
- Seek expert assistance: Engage experienced ERP consultants to guide the implementation process.
- Establish clear communication channels: Keep all stakeholders informed throughout the implementation process.
- Plan for post-implementation support: Ensure ongoing support and maintenance to address any issues that may arise.
Strong Final Conclusion:
Enterprise Resource Planning (ERP) systems offer a transformative opportunity for businesses in the distribution industry. By integrating various business functions into a unified system, ERP solutions deliver enhanced efficiency, improved accuracy, and increased profitability. The key to successful implementation lies in careful planning, effective training, and ongoing support. Companies that embrace ERP are well-positioned to thrive in the competitive distribution landscape, achieving sustainable growth and exceeding customer expectations. The future of distribution hinges on the effective utilization of technology, and ERP stands as a cornerstone of that future.
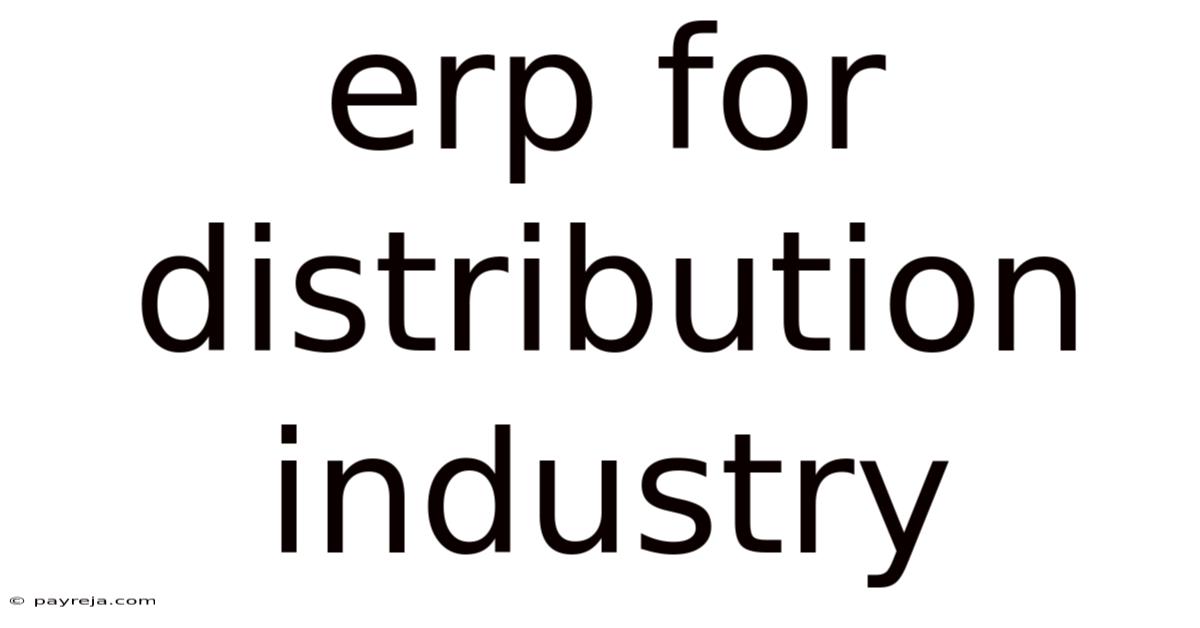
Thank you for visiting our website wich cover about Erp For Distribution Industry. We hope the information provided has been useful to you. Feel free to contact us if you have any questions or need further assistance. See you next time and dont miss to bookmark.
Also read the following articles
Article Title | Date |
---|---|
Electronic Erp | Apr 06, 2025 |
Erp In Operations Management | Apr 06, 2025 |
Defibrillateur Obligatoire Erp | Apr 06, 2025 |
Cosmetic Erp Software | Apr 06, 2025 |
Erp For Software Development Company | Apr 06, 2025 |