Brewery Erp
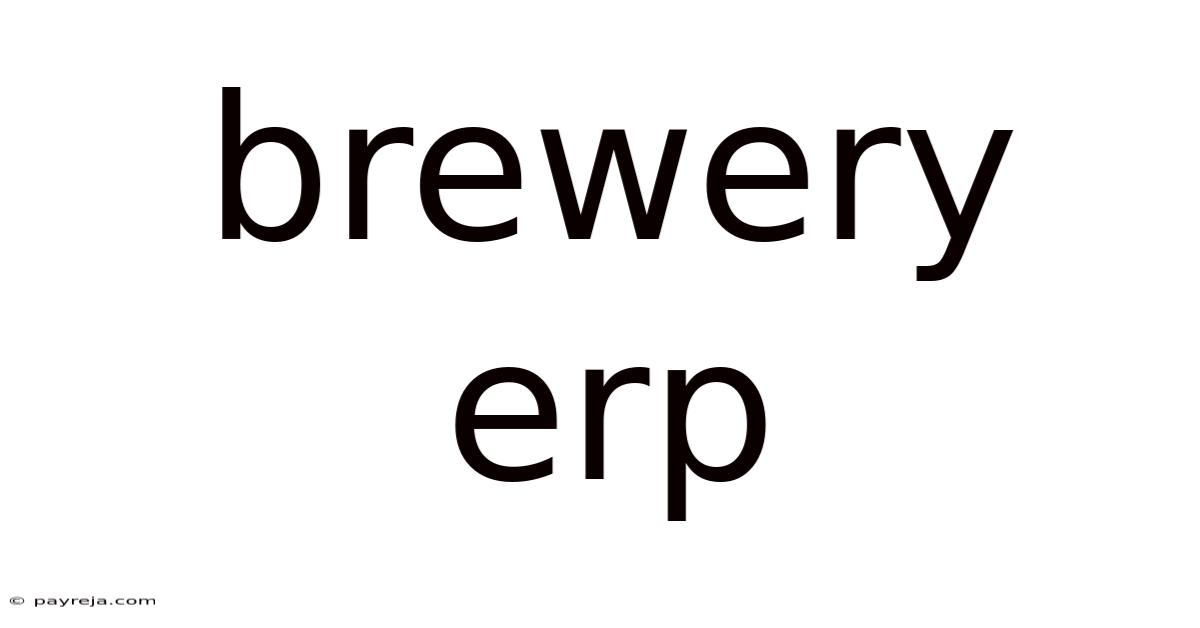
Discover more detailed and exciting information on our website. Click the link below to start your adventure: Visit Best Website meltwatermedia.ca. Don't miss out!
Table of Contents
Unleashing Brewery Efficiency: A Deep Dive into Brewery ERP Systems
What if optimizing your brewery's operations could unlock unprecedented growth and profitability? Brewery ERP systems are revolutionizing the craft brewing industry, transforming how breweries manage every aspect of their business.
Editor’s Note: This article on Brewery ERP systems has been updated today to reflect the latest industry trends and technological advancements.
Why Brewery ERP Matters
The craft brewing industry is booming, but success demands more than just exceptional beer. Modern breweries face complex challenges: managing inventory across multiple locations, tracking production costs, ensuring regulatory compliance, and optimizing supply chains. A Brewery Enterprise Resource Planning (ERP) system offers a centralized platform to streamline these operations, fostering efficiency, profitability, and scalability. From small craft breweries to large-scale production facilities, an ERP solution can provide a significant competitive edge by automating processes, improving decision-making, and reducing operational costs. Key areas impacted include inventory management, production planning, quality control, sales and distribution, and financial management. The ability to integrate these disparate functions into a single, unified system is crucial for long-term growth and sustainability. Effective use of a brewery ERP can also improve customer relations through better order tracking and fulfillment, resulting in enhanced customer satisfaction.
Article Overview
This article provides a comprehensive exploration of Brewery ERP systems. It will cover the core functionalities, the selection process, implementation considerations, and the overall impact on brewery operations. Readers will gain a clear understanding of how these systems can optimize various aspects of their business, from raw material procurement to finished goods distribution. The article will also delve into the connection between effective data management (a key element of any successful ERP) and the overall success of a brewery.
Showcase Research and Data-Driven Insights
The growth of the craft brewing industry is undeniable, with a substantial increase in the number of breweries and overall production volume in recent years (Source: Brewers Association statistics). However, maintaining profitability in a competitive market requires operational excellence. Studies have shown that businesses using ERP systems experience significant improvements in efficiency, cost reduction, and overall profitability (Source: Gartner research on ERP implementation). These improvements are particularly relevant in the context of breweries, where managing complex production processes, ingredient sourcing, and distribution networks is paramount. A well-implemented ERP system can reduce waste, minimize errors, and provide real-time insights into operational performance, contributing significantly to the bottom line.
Key Insights at a Glance
Key Insight | Explanation |
---|---|
Streamlined Production Planning | Optimize production schedules, reduce downtime, and improve resource allocation. |
Enhanced Inventory Management | Real-time visibility into ingredient and finished goods inventory, minimizing stockouts and waste. |
Improved Quality Control | Track batch information, ensure consistency, and meet regulatory compliance requirements. |
Optimized Supply Chain Management | Manage relationships with suppliers, optimize procurement processes, and ensure timely delivery of raw materials. |
Automated Financial Reporting | Generate accurate financial reports, track profitability, and make informed business decisions. |
Strengthened Customer Relationship Management (CRM) Integration | Seamlessly integrate with CRM for better customer service, order tracking, and personalized communication. |
Brewery ERP: A Deep Dive
Production Planning & Scheduling: A Brewery ERP system allows for detailed scheduling of brewing batches, taking into account ingredient availability, equipment capacity, and demand forecasts. This optimization minimizes downtime, maximizes production efficiency, and ensures timely fulfillment of orders. Features such as batch tracking and recipe management ensure consistency and traceability across all batches.
Inventory Management: Effective inventory control is crucial for breweries. An ERP system provides real-time visibility into raw material (malt, hops, yeast) and packaging inventory levels, preventing stockouts and minimizing waste. It also supports just-in-time inventory management strategies, reducing storage costs and improving cash flow. Sophisticated features can even predict demand and suggest optimal stock levels.
Quality Control: Brewery ERPs incorporate modules for detailed quality control. Every stage of the brewing process, from ingredient inspection to finished product testing, can be tracked and monitored. This ensures consistency in product quality, meets regulatory compliance standards, and allows for quick identification and resolution of any quality issues. Batch traceability enables swift response to potential contamination or defects.
Supply Chain Management: Effective management of the supply chain is essential for a smooth brewing operation. A Brewery ERP system facilitates streamlined procurement processes, managing relationships with suppliers, tracking deliveries, and ensuring the timely arrival of necessary ingredients. This enhances efficiency and reduces potential disruptions to production. It can also provide insights into supplier performance and facilitate negotiation of better terms.
Sales & Distribution: The sales and distribution module of a Brewery ERP allows for efficient order management, tracking shipments, and managing customer relationships. Real-time order status updates improve customer service and enhance communication. Integration with transportation management systems (TMS) optimizes logistics and reduces shipping costs.
Financial Management: A Brewery ERP system offers comprehensive financial management capabilities, including cost accounting, budgeting, and reporting. It enables accurate tracking of production costs, sales revenue, and profitability. This crucial data informs business decisions and facilitates better financial planning.
The Connection Between Data Management and Brewery Success
Effective data management is the cornerstone of a successful Brewery ERP implementation. The system's ability to collect, analyze, and interpret data from various sources – production, inventory, sales, finance – provides crucial insights into operational performance. This data-driven approach enables breweries to make informed decisions, identify areas for improvement, and optimize processes for increased efficiency and profitability. Without robust data management, the ERP system becomes a mere collection of disconnected modules, failing to deliver its full potential.
Exploring the Connection Between Data Analytics and Brewery ERP
Data analytics, fueled by the data captured within the Brewery ERP system, is becoming increasingly important. Analyzing production data can reveal bottlenecks, optimize ingredient usage, and predict future demand. Sales data provides insights into customer preferences, allowing for better product development and targeted marketing. Financial data informs pricing strategies and identifies cost-saving opportunities. By leveraging data analytics, breweries can gain a competitive edge and make more strategic decisions.
Roles and Real-World Examples:
- Small Craft Breweries: A small brewery might use an ERP system to manage inventory, track production costs, and streamline order fulfillment, improving efficiency and allowing them to focus on brewing. Examples include using cloud-based ERP solutions for scalability and cost-effectiveness.
- Mid-Sized Breweries: These breweries can leverage more advanced ERP features, such as sophisticated forecasting, supply chain management tools, and CRM integration to enhance customer relations and optimize distribution.
- Large-Scale Breweries: Larger operations utilize enterprise-grade ERP systems with advanced analytics and reporting capabilities to manage complex production processes across multiple locations, optimizing supply chains and enhancing overall efficiency.
Risks and Mitigations:
- Implementation Challenges: ERP implementation can be complex and time-consuming. Thorough planning, experienced consultants, and dedicated internal resources are essential for a successful rollout.
- Cost: The initial investment in an ERP system can be significant. A careful cost-benefit analysis should be conducted to assess the return on investment.
- Data Migration: Migrating existing data to the new ERP system can be challenging. A well-defined data migration plan is crucial to avoid data loss or inconsistencies.
- Integration Issues: Integrating the ERP system with other existing software applications can be complex. Careful planning and testing are needed to ensure seamless integration.
Impact and Implications:
- Increased Efficiency: Streamlined operations, reduced waste, and optimized production scheduling lead to significant efficiency gains.
- Improved Profitability: Reduced costs, increased output, and better inventory management contribute to improved profitability.
- Enhanced Scalability: An ERP system provides a scalable platform that can support future growth and expansion.
- Better Decision-Making: Data-driven insights facilitate more informed business decisions.
FAQ: Brewery ERP Systems
Q1: What is the cost of a Brewery ERP system?
A1: The cost varies widely depending on the size of the brewery, the features required, and the chosen vendor. Cloud-based solutions typically offer a subscription model, while on-premise systems involve a higher upfront investment. It's crucial to get detailed quotes from multiple vendors.
Q2: How long does it take to implement a Brewery ERP system?
A2: Implementation time varies depending on the complexity of the system and the size of the brewery. Smaller breweries might complete implementation in a few months, while larger breweries may require a year or more.
Q3: What are the key features to look for in a Brewery ERP system?
A3: Essential features include production planning and scheduling, inventory management, quality control, supply chain management, sales and distribution, and financial management. Look for systems with robust reporting and analytics capabilities.
Q4: Do I need specialized ERP software for a brewery, or can I use a generic system?
A4: While generic ERP systems might offer some functionality, specialized brewery ERP solutions are designed to address the unique challenges and requirements of the brewing industry. They often include features tailored to recipe management, batch tracking, and quality control specific to brewing.
Q5: Can a Brewery ERP system integrate with my existing systems?
A5: A good Brewery ERP system should offer seamless integration with other business applications, such as CRM, accounting software, and warehouse management systems. This integration is key to maximizing efficiency and data flow.
Q6: What kind of training is needed for Brewery ERP system users?
A6: Comprehensive training is essential for all users. Vendors typically offer training programs, and it's important to ensure that staff are adequately trained on all aspects of the system before going live.
Actionable Tips for Implementing a Brewery ERP
- Assess your needs: Carefully evaluate your brewery's specific requirements and choose a system that meets those needs.
- Choose the right vendor: Select a vendor with experience in the brewing industry and a proven track record of successful implementations.
- Plan thoroughly: Develop a detailed implementation plan that includes timelines, resources, and a clear scope of work.
- Involve your team: Ensure that your team is involved in the selection and implementation process. Their input is invaluable.
- Test thoroughly: Conduct rigorous testing before going live to identify and resolve any issues.
- Provide adequate training: Ensure that your team is adequately trained on how to use the system effectively.
- Monitor and optimize: Continuously monitor system performance and make adjustments as needed to optimize its effectiveness.
Conclusion
Brewery ERP systems are transforming the craft brewing industry by providing a powerful platform for optimizing operations and improving profitability. By streamlining processes, enhancing data management, and improving decision-making, these systems empower breweries to navigate the complexities of the modern marketplace and achieve sustainable growth. Understanding the capabilities, implementation considerations, and the connection between data and success is crucial for breweries looking to leverage technology for competitive advantage. The future of brewing is data-driven, and a well-implemented ERP system is a critical tool for success in this dynamic industry. Investing in the right Brewery ERP is not merely an expense but a strategic investment in the future of your brewery.
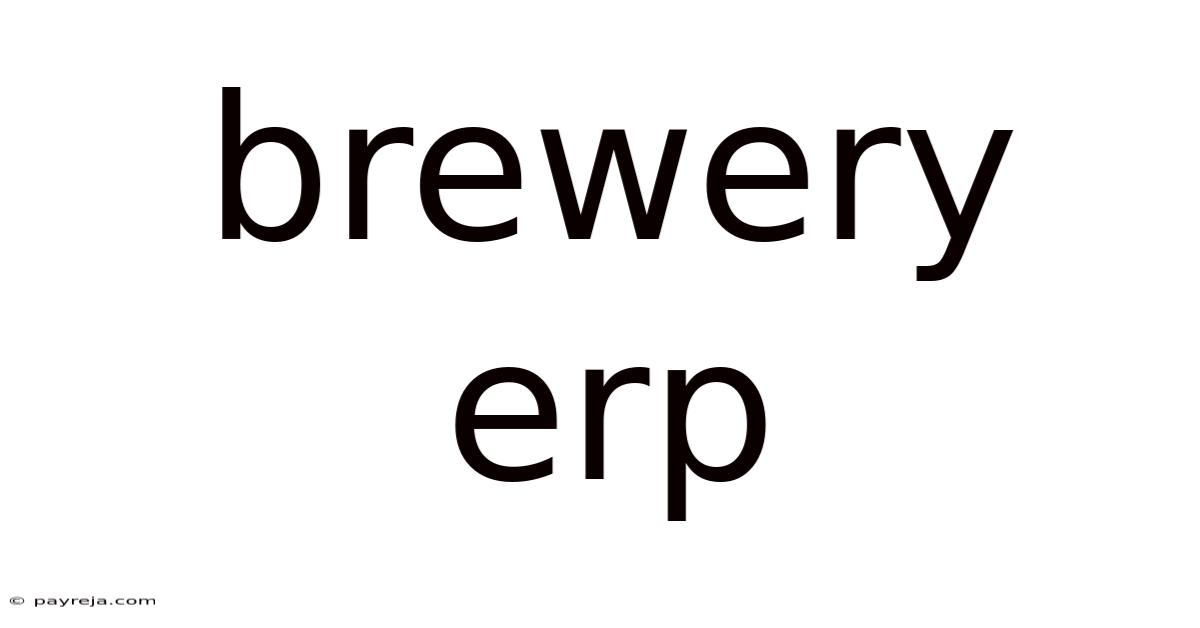
Thank you for visiting our website wich cover about Brewery Erp. We hope the information provided has been useful to you. Feel free to contact us if you have any questions or need further assistance. See you next time and dont miss to bookmark.
Also read the following articles
Article Title | Date |
---|---|
Automotive Tier Suppliers Erp | Apr 06, 2025 |
Erp For Industrial Machinery | Apr 06, 2025 |
Erp B2b | Apr 06, 2025 |
Erp Prozessindustrie | Apr 06, 2025 |
Erp 2022 Usda | Apr 06, 2025 |