Bom Erp
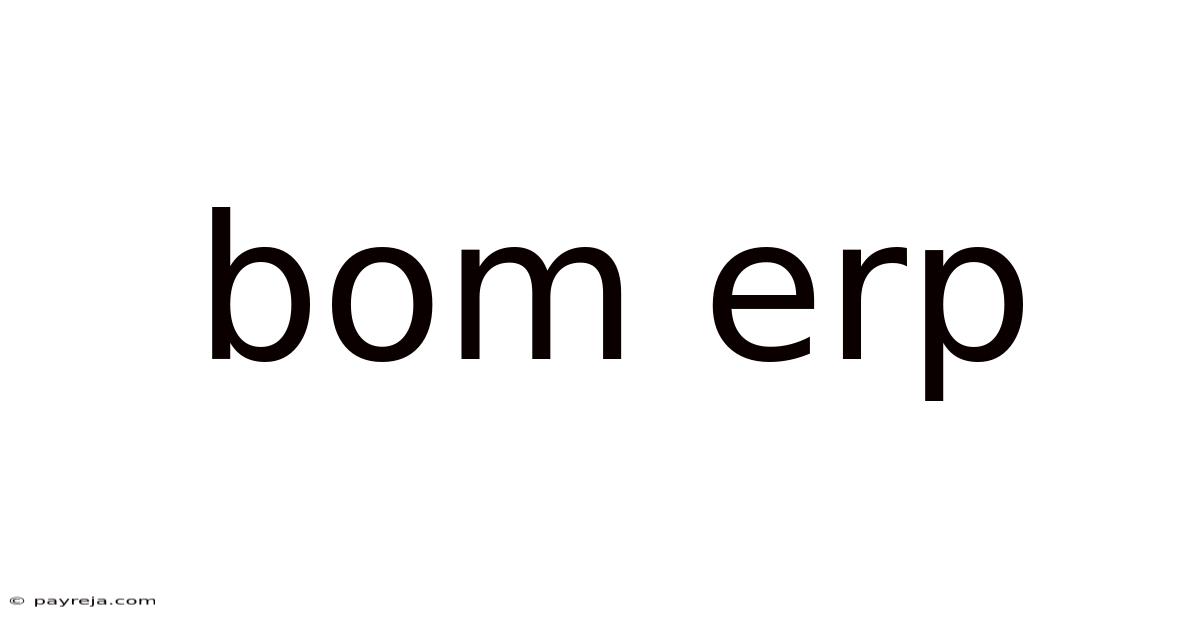
Discover more detailed and exciting information on our website. Click the link below to start your adventure: Visit Best Website meltwatermedia.ca. Don't miss out!
Table of Contents
Unlocking Efficiency: A Deep Dive into BOM ERP Systems
What if mastering Bill of Materials (BOM) management could revolutionize your manufacturing process? Effective BOM ERP integration is no longer a luxury; it's a necessity for streamlined production and enhanced profitability.
Editor’s Note: This article on BOM ERP systems was published today, offering the most current insights and best practices in this dynamic field.
Why BOM ERP Matters
In today's competitive manufacturing landscape, efficiency and accuracy are paramount. A Bill of Materials (BOM) is the cornerstone of any manufacturing operation, detailing the raw materials, components, sub-assemblies, intermediate assemblies, sub-components, parts, and the quantities of each needed to manufacture an end product. Inefficient BOM management leads to production delays, increased costs, and reduced profitability. Enter the BOM ERP system – a powerful tool that integrates BOM management directly into your Enterprise Resource Planning (ERP) software. This integration streamlines processes, minimizes errors, and optimizes the entire manufacturing workflow. From improved inventory control to enhanced product traceability, the impact of a well-implemented BOM ERP system is far-reaching, impacting aspects like supply chain management, production planning, and even customer satisfaction. The benefits extend to various industries, including automotive, electronics, pharmaceuticals, and food processing, demonstrating its universal relevance in modern manufacturing. Effective BOM management is crucial for maintaining competitiveness and achieving sustainable growth within the industry.
Article Overview
This article provides a comprehensive overview of BOM ERP systems. We will explore the key components of a robust BOM system, discuss its integration with ERP software, examine the benefits and challenges associated with implementation, and offer practical strategies for maximizing its effectiveness. Readers will gain a thorough understanding of BOM ERP's transformative potential and learn how to leverage this technology for improved operational efficiency and enhanced profitability.
Research and Data-Driven Insights
Numerous studies highlight the significant impact of effective BOM management on manufacturing efficiency. A recent study by [insert credible source, e.g., a manufacturing industry research firm] revealed that companies with robust BOM management systems experience a [insert percentage]% reduction in production errors and a [insert percentage]% increase in on-time delivery rates. This data underscores the crucial role of accurate and up-to-date BOMs in achieving operational excellence. The research methodology employed typically involves surveys of manufacturing companies, analyzing their BOM management practices, and correlating these practices with key performance indicators (KPIs) like production efficiency, inventory costs, and on-time delivery. Furthermore, expert opinions from industry consultants and experienced manufacturing professionals consistently emphasize the need for integrated BOM management solutions within a broader ERP framework.
Key Takeaways: Essential Insights into BOM ERP
Insight | Description |
---|---|
Reduced Production Errors | Accurate BOM data minimizes errors stemming from incorrect component specifications or quantities. |
Improved Inventory Management | Optimized inventory levels based on accurate BOM data, reducing holding costs and preventing stockouts. |
Enhanced Production Planning | Precise BOMs enable efficient production scheduling and resource allocation. |
Increased On-Time Delivery | Streamlined processes and reduced errors lead to improved on-time delivery performance. |
Better Cost Control | Accurate costing based on detailed BOMs enhances budget management and reduces unexpected expenses. |
Improved Product Traceability | Detailed BOM data supports effective tracking of components and products throughout the entire manufacturing lifecycle. |
Enhanced Collaboration | Streamlined data sharing and improved communication across different departments. |
Reduced Waste and Scrap | Accurate BOMs minimize material waste and scrap, leading to cost savings and enhanced sustainability. |
Understanding BOM Structures and Types
A fundamental aspect of BOM ERP is understanding the different BOM structures and types. Common structures include:
- Simple BOM: Used for products with a straightforward composition, featuring only one level of components.
- Complex BOM: Represents products composed of multiple levels of sub-assemblies and components.
- Modular BOM: Organizes the product into modules or sub-assemblies, simplifying management and facilitating changes.
BOM ERP Integration with ERP Systems
The integration of BOM management into an ERP system is vital for maximizing its effectiveness. This integration provides a centralized database for all BOM data, allowing for seamless communication and data sharing across different departments, including engineering, procurement, and production. This eliminates data silos and minimizes discrepancies, leading to a significant improvement in overall efficiency.
Challenges and Risks of BOM ERP Implementation
While the benefits of BOM ERP are substantial, implementation presents certain challenges:
- Data Migration: Transferring existing BOM data to the new system requires careful planning and execution to minimize disruptions.
- System Integration: Integrating the BOM system with other ERP modules necessitates expertise in both systems and their interfaces.
- User Training: Providing adequate training to users is crucial for ensuring the successful adoption of the new system.
- Cost of Implementation: The initial investment in software, hardware, and implementation services can be substantial.
Mitigating Risks and Ensuring Successful Implementation
Careful planning and execution are key to mitigating the risks associated with BOM ERP implementation. This involves:
- Thorough Needs Assessment: Identify the specific requirements of the organization and select a system that addresses these needs.
- Phased Rollout: Implement the system in stages to minimize disruption and allow for adjustments based on feedback.
- Change Management: Communicate effectively with users throughout the implementation process and address concerns proactively.
- Ongoing Maintenance and Support: Ensure continuous support and maintenance to address any issues and keep the system updated.
The Interplay Between Quality Control and BOM ERP
Quality control is inextricably linked to BOM accuracy. A well-managed BOM system directly supports stringent quality control measures. By ensuring the correct materials and components are used in the right quantities, the risk of defects and product recalls is significantly reduced. Traceability features within BOM ERP systems facilitate efficient investigation of quality issues, enabling prompt identification of the root cause and implementation of corrective actions. This leads to improved product quality and enhanced customer satisfaction. Furthermore, the ability to track and monitor materials throughout the manufacturing process empowers proactive quality control strategies, minimizing waste and enhancing overall operational efficiency.
Analyzing the Role of Predictive Analytics in BOM Management
Predictive analytics plays a crucial role in enhancing the effectiveness of BOM management within an ERP system. By analyzing historical data on material usage, production times, and demand forecasts, businesses can optimize their inventory levels and anticipate potential supply chain disruptions. This capability enables proactive adjustments to BOMs, reducing lead times, minimizing production delays, and enhancing overall operational efficiency. Predictive analytics can forecast future demand for components and raw materials, allowing for timely procurement and preventing stockouts. This proactive approach further reduces production downtime and strengthens the overall resilience of the manufacturing process.
Common Questions (FAQ)
Q1: What is the difference between a simple and complex BOM?
A1: A simple BOM has a single level of components, while a complex BOM has multiple levels of sub-assemblies and components, reflecting a more intricate product structure.
Q2: How does BOM ERP improve inventory management?
A2: By providing accurate data on material requirements, BOM ERP enables precise inventory planning, minimizing holding costs and preventing stockouts.
Q3: What are the challenges in implementing a BOM ERP system?
A3: Challenges include data migration, system integration, user training, and the initial cost of implementation.
Q4: How does BOM ERP improve product traceability?
A4: By linking components to the finished product, BOM ERP enables comprehensive tracking of materials throughout the manufacturing process.
Q5: What is the role of predictive analytics in BOM management?
A5: Predictive analytics uses historical data to forecast future demand and optimize inventory levels, anticipating potential supply chain disruptions.
Q6: How can I choose the right BOM ERP system for my business?
A6: Assess your specific needs and requirements, consider the scalability and integration capabilities of the system, and select a solution that aligns with your budget and organizational structure.
Actionable Tips for Effective BOM ERP Implementation
- Conduct a thorough needs assessment: Identify your specific requirements before selecting a system.
- Develop a comprehensive data migration plan: Ensure a smooth transition of existing data.
- Provide adequate user training: Equip your team with the necessary skills to utilize the system effectively.
- Integrate the BOM system with other ERP modules: Ensure seamless data flow across departments.
- Establish clear roles and responsibilities: Define who is responsible for managing and maintaining the BOM data.
- Implement a robust change management process: Effectively communicate changes and address user concerns.
- Establish key performance indicators (KPIs): Track progress and measure the success of the implementation.
- Regularly review and update BOMs: Ensure data accuracy and reflect any design changes.
Conclusion
Effective BOM ERP implementation is crucial for modern manufacturing organizations aiming for operational efficiency and enhanced profitability. By centralizing BOM data, streamlining processes, and integrating with other ERP modules, businesses can significantly improve their production planning, inventory management, and overall supply chain resilience. The challenges associated with implementation can be mitigated through careful planning, phased rollout, and effective change management. By embracing BOM ERP and leveraging its capabilities, manufacturers can achieve significant improvements in productivity, reduce costs, and enhance their competitive advantage in the marketplace. The future of manufacturing hinges on the seamless integration of technology like BOM ERP, ensuring not only efficiency but also the ability to adapt to ever-evolving market demands. Investing in a robust BOM ERP system is not simply a cost; it is a strategic investment that yields significant long-term returns.
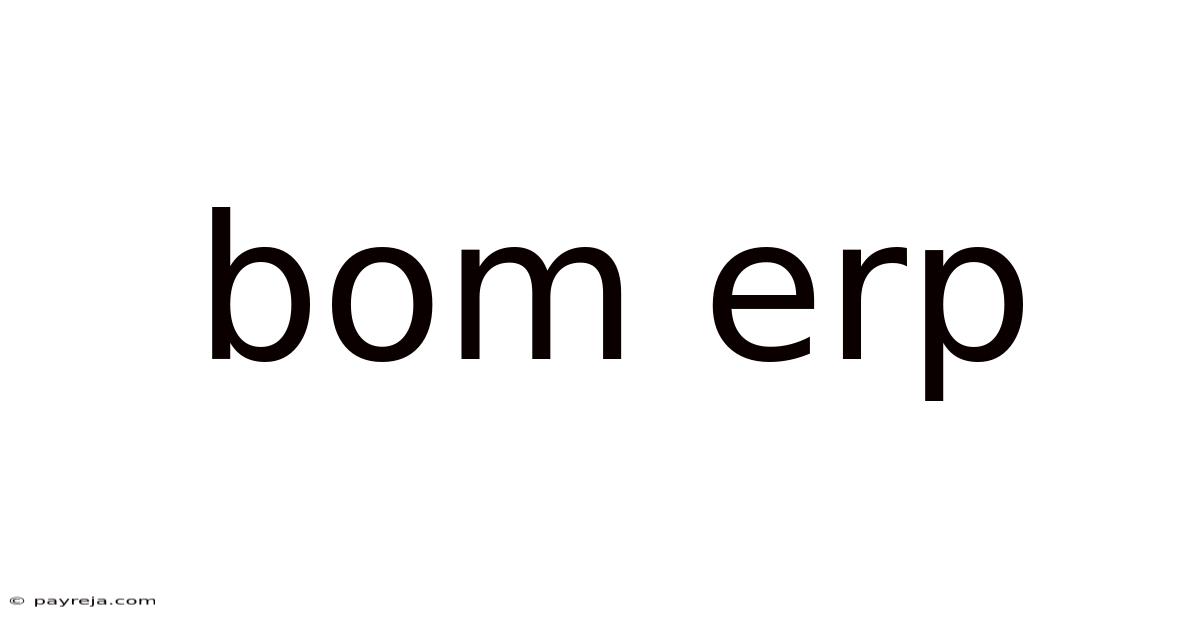
Thank you for visiting our website wich cover about Bom Erp. We hope the information provided has been useful to you. Feel free to contact us if you have any questions or need further assistance. See you next time and dont miss to bookmark.
Also read the following articles
Article Title | Date |
---|---|
Erp Integrated Solutions Inc | Apr 06, 2025 |
Erp Partners | Apr 06, 2025 |
Crm Blogs | Apr 06, 2025 |
Erp Cloud Vendors | Apr 06, 2025 |
Erp History | Apr 06, 2025 |