Axle Made
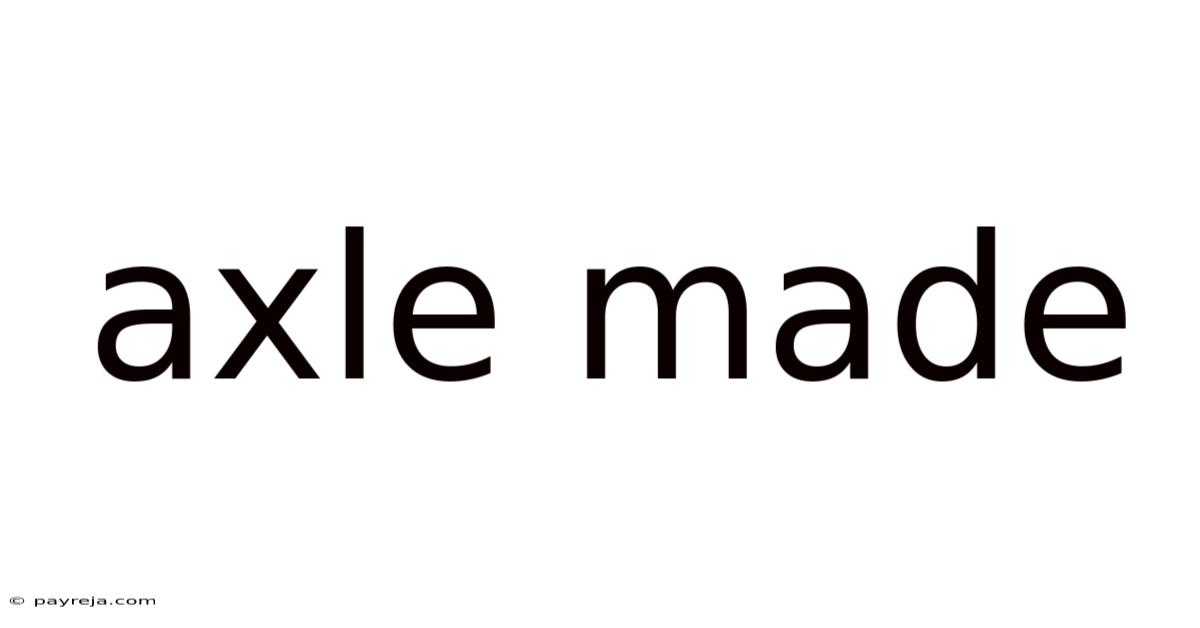
Discover more detailed and exciting information on our website. Click the link below to start your adventure: Visit Best Website meltwatermedia.ca. Don't miss out!
Table of Contents
Unveiling the Secrets of Axle Manufacturing: A Deep Dive into Design, Processes, and Innovation
What if mastering axle manufacturing could revolutionize transportation and engineering?
Axle manufacturing is at the heart of modern mobility, driving innovation across diverse sectors.
Editor’s Note: This article on axle manufacturing has been updated today to reflect the latest advancements and industry trends.
Axle manufacturing is a critical component of various industries, from automotive and heavy-duty trucking to aerospace and railway systems. Axles are fundamental load-bearing components, transmitting power and supporting the weight of vehicles and machinery. Understanding the complexities of axle design, manufacturing processes, and the continuous drive for innovation is vital for appreciating the technological advancements that underpin modern mobility. This article will explore the multifaceted world of axle manufacturing, covering design considerations, production techniques, quality control, and future trends.
What this article covers: This article provides a comprehensive overview of axle manufacturing, covering material selection, forging, machining, heat treatment, finishing processes, quality control, and the influence of emerging technologies. Readers will gain an in-depth understanding of the entire manufacturing lifecycle, from initial design to final product. The article will also explore the relationship between material science and axle design, highlight industry challenges and solutions, and examine future trends shaping the industry.
The Significance of Axle Manufacturing
Axles are the backbone of countless moving machines. Their integrity directly impacts safety, efficiency, and operational lifespan. The automotive sector relies heavily on axles for passenger cars, trucks, and SUVs. Heavy-duty vehicles, such as semi-trailers and construction equipment, require axles capable of withstanding extreme loads and stresses. The aerospace industry utilizes highly specialized axles in landing gear, while railway systems depend on robust axles for train carriages and locomotives. The economic impact of axle manufacturing is substantial, underpinning global transportation and industrial operations.
Design Considerations in Axle Manufacturing
The design of an axle is a delicate balance between strength, durability, and weight optimization. Several crucial factors must be considered:
-
Load Capacity: Axles must be capable of supporting the designated weight of the vehicle or machinery. This involves meticulous calculations considering factors like axle length, diameter, material properties, and anticipated operating conditions.
-
Material Selection: Material choice plays a crucial role in axle performance. Common materials include steel alloys (high-strength low-alloy steels, alloy steels), and in some specialized applications, titanium alloys or composite materials. The selection is influenced by factors such as strength-to-weight ratio, cost, and corrosion resistance.
-
Geometry and Configuration: Axle geometry (straight, bent, or tapered) is determined by the vehicle's design and application. Configurations can include single axles, tandem axles, and bogie axles, each tailored to specific load requirements and weight distribution.
-
Fatigue Resistance: Axles are subjected to repetitive cyclic loading, leading to potential fatigue failure. Therefore, design must incorporate features to mitigate fatigue issues, such as optimized stress concentrations and the incorporation of surface treatments to enhance durability.
Manufacturing Processes in Axle Manufacturing
The manufacturing process for axles is a multi-stage procedure that often involves forging, machining, heat treatment, and surface finishing.
-
Forging: Forging is a crucial initial step for many axle designs. Hot forging, in particular, is commonly used to shape the axle blank from a steel billet, enhancing its strength and grain structure. This process ensures superior mechanical properties compared to casting.
-
Machining: After forging, precision machining is employed to create the final axle shape and dimensions. Operations may include turning, milling, drilling, and grinding to achieve the required tolerances and surface finish. Computer Numerical Control (CNC) machining offers high precision and repeatability.
-
Heat Treatment: Heat treatment is essential for enhancing the mechanical properties of the axle, improving its strength, hardness, and toughness. Processes such as quenching and tempering are commonly employed to achieve the desired microstructure and mechanical properties. This step is critical to ensuring the axle's resilience against fatigue and wear.
-
Surface Finishing: Surface finishing techniques, such as shot peening or coating (e.g., zinc plating, powder coating), can further improve axle durability and corrosion resistance. Shot peening induces compressive residual stresses on the surface, enhancing fatigue life. Coatings provide protection against environmental factors.
Quality Control and Testing
Throughout the manufacturing process, rigorous quality control measures are employed to ensure that axles meet stringent specifications. These include:
-
Dimensional Inspection: Precise measurements are taken to confirm that the axles conform to the design drawings. Sophisticated measuring equipment, such as coordinate measuring machines (CMMs) and optical measuring systems, are often used.
-
Material Testing: Material properties are verified through tensile testing, hardness testing, and impact testing. These tests ensure that the chosen material meets the required strength, hardness, and toughness levels.
-
Non-Destructive Testing (NDT): NDT methods, such as ultrasonic testing, magnetic particle inspection, and liquid penetrant inspection, are used to detect internal flaws or surface defects. This is crucial for identifying potential weaknesses before the axle is put into service.
-
Fatigue Testing: Axles are subjected to fatigue testing to simulate the repetitive loading experienced in real-world applications. This test helps determine the axle's fatigue life and identify potential design weaknesses.
The Connection Between Material Science and Axle Design
The evolution of axle design is inextricably linked to advancements in material science. The development of high-strength low-alloy steels (HSLA) has significantly enhanced axle strength and durability while reducing weight. Further research into advanced materials, such as carbon fiber composites and titanium alloys, is exploring the potential for even lighter, stronger, and more durable axle designs. This continuous quest for improved material properties is vital for enhancing vehicle performance, fuel efficiency, and overall operational lifespan.
Challenges and Solutions in Axle Manufacturing
The axle manufacturing industry faces several ongoing challenges:
-
Cost Optimization: Balancing material costs, manufacturing processes, and quality control measures is a constant challenge. Innovations in manufacturing techniques and material selection are crucial to cost-effective production.
-
Sustainability: Environmental concerns are driving the industry towards sustainable manufacturing practices. This includes reducing waste, optimizing energy consumption, and using environmentally friendly materials and processes.
-
Automation and Robotics: The increasing adoption of automation and robotics in manufacturing is improving efficiency, consistency, and safety. However, the implementation of advanced automation systems requires significant investment.
-
Product Lifecycle Management (PLM): Efficient PLM systems are essential for managing the entire lifecycle of an axle design, from initial conception to end-of-life recycling. This integrated approach streamlines processes and facilitates collaboration across various teams.
Future Trends in Axle Manufacturing
Several significant trends are reshaping the axle manufacturing landscape:
-
Additive Manufacturing: 3D printing, or additive manufacturing, is gaining traction for creating complex axle geometries and customized designs. This technology allows for the production of lightweight, high-strength axles with intricate internal structures.
-
Smart Axles: The incorporation of sensors and embedded systems is transforming axles into intelligent components, enabling real-time monitoring of operating conditions. This data can be used for predictive maintenance, enhancing safety and extending the axle's lifespan.
-
Lightweighting: The ongoing push for improved fuel efficiency and reduced emissions is driving the demand for lighter axles. This is being addressed through advanced materials, innovative designs, and optimized manufacturing processes.
-
Increased Use of Simulation: Computer-aided engineering (CAE) and finite element analysis (FEA) are playing increasingly critical roles in axle design and optimization. Simulations help engineers predict axle performance under various loading conditions, improving design accuracy and reducing the need for costly physical prototypes.
Key Takeaways: A Summary of Axle Manufacturing Insights
Insight | Description |
---|---|
Material Selection is Crucial | The choice of material significantly influences axle strength, weight, cost, and durability. |
Forging Enhances Mechanical Properties | Hot forging improves grain structure, enhancing strength and fatigue resistance compared to casting. |
Heat Treatment is Essential | Heat treatment processes (quenching and tempering) are critical for achieving desired strength, hardness, and toughness. |
Quality Control is Paramount | Rigorous testing (dimensional, material, NDT, fatigue) ensures that axles meet stringent quality standards and safety requirements. |
Innovation Drives the Industry | Advancements in material science, manufacturing processes, and automation continue to shape the future of axle manufacturing, driving cost-effectiveness and performance enhancements. |
Exploring the Connection Between Material Science and Axle Manufacturing
Material science underpins virtually every aspect of axle manufacturing. The selection of appropriate materials dictates the axle's strength, durability, weight, and cost-effectiveness. Advancements in materials, such as high-strength steel alloys, have led to the development of stronger, lighter axles. The use of advanced alloys and composite materials is constantly being explored to meet the ever-increasing demands for higher load capacities, improved fatigue resistance, and extended service life. For instance, the use of titanium alloys in aerospace applications demonstrates the critical role of material science in creating specialized axles capable of withstanding extreme conditions.
Roles and Real-World Examples
-
High-Strength Steel Alloys: Widely used in automotive and heavy-duty truck applications. These alloys provide excellent strength-to-weight ratios, enhancing vehicle performance and fuel efficiency.
-
Titanium Alloys: Used in demanding aerospace applications where high strength-to-weight ratios and corrosion resistance are critical. These alloys enable the development of lightweight yet robust landing gear axles.
-
Composite Materials: Emerging as a potential solution for future axle designs. These materials offer the possibility of even lighter, stronger, and more durable axles, but challenges related to cost and manufacturing remain.
Risks and Mitigations
-
Material Failure: Improper material selection or manufacturing defects can lead to premature failure. Rigorous quality control measures and NDT techniques help mitigate this risk.
-
Fatigue Failure: Repetitive loading can induce fatigue cracks, leading to unexpected failure. Design optimization, heat treatment, and surface treatments can significantly improve fatigue life.
-
Corrosion: Exposure to environmental factors can cause corrosion. Protective coatings and surface treatments help minimize corrosion and extend the axle's service life.
Impact and Implications
The continuous advancement of axle manufacturing significantly impacts transportation and various industries. Lighter, stronger axles improve fuel efficiency, reduce emissions, and enhance vehicle performance. Innovations in manufacturing processes increase production efficiency and reduce costs. The development of smart axles allows for real-time monitoring and predictive maintenance, enhancing safety and minimizing downtime.
Reinforcing the Connection in the Conclusion
Material science and axle manufacturing are inextricably linked. The evolution of materials and our understanding of their properties have directly influenced axle design and performance. Continued advancements in material science will undoubtedly continue to drive innovation in axle manufacturing, leading to lighter, stronger, more durable, and cost-effective axles in the future.
Diving Deeper into Material Science
Material science involves the study of the properties of materials and their relationship to their structure and processing. This understanding is crucial for selecting and optimizing materials for axle manufacturing. Factors such as tensile strength, yield strength, hardness, fatigue resistance, and corrosion resistance are all critical in determining a material's suitability for axle applications. The development of advanced materials, such as high-strength steel alloys and composites, directly addresses the need for stronger, lighter, and more durable axles.
Frequently Asked Questions (FAQs)
Q1: What are the most common materials used in axle manufacturing? A1: High-strength low-alloy steels and alloy steels are the most prevalent materials. In specialized applications, titanium alloys and composite materials are also used.
Q2: How is the strength of an axle determined? A2: The strength of an axle depends on factors like material properties, geometry, manufacturing processes, and heat treatment. Various tests, such as tensile testing and fatigue testing, are employed to assess the axle's strength.
Q3: What are the benefits of using forging in axle manufacturing? A3: Forging enhances the material's grain structure, resulting in improved mechanical properties (strength, toughness, fatigue resistance) compared to casting.
Q4: What is the role of heat treatment in axle manufacturing? A4: Heat treatment processes like quenching and tempering control the microstructure of the axle material, optimizing its strength, hardness, and toughness to meet specific performance requirements.
Q5: How is quality control ensured in axle manufacturing? A5: Rigorous quality control involves dimensional inspections, material testing, non-destructive testing, and fatigue testing throughout the manufacturing process.
Q6: What are the future trends in axle manufacturing? A6: Future trends include the adoption of additive manufacturing, the development of smart axles with embedded sensors, a focus on lightweighting, and the increased use of simulation in design optimization.
Actionable Tips on Axle Manufacturing
- Prioritize material selection: Carefully choose materials based on specific load requirements, environmental conditions, and cost constraints.
- Optimize the manufacturing process: Select efficient processes like forging and CNC machining to enhance quality and reduce costs.
- Employ rigorous quality control: Implement comprehensive testing protocols to ensure that axles meet stringent standards and safety regulations.
- Invest in automation and robotics: Improve production efficiency, consistency, and safety by adopting advanced automation techniques.
- Embrace sustainable manufacturing practices: Reduce waste, optimize energy consumption, and utilize environmentally friendly materials to minimize environmental impact.
- Stay updated on industry trends: Keep abreast of the latest advancements in material science, manufacturing processes, and technology to maintain a competitive edge.
- Collaborate with material science experts: Engage with specialists to ensure the utilization of the most advanced and appropriate materials for axle manufacturing.
- Implement robust PLM systems: Optimize efficiency and collaboration throughout the entire lifecycle of axle design and production.
Conclusion
Axle manufacturing is a vital sector underpinning diverse industries. The interplay of material science, advanced manufacturing techniques, and stringent quality control ensures the production of robust, reliable axles crucial for transportation and industrial applications. Future advancements in materials, manufacturing processes, and automation will further enhance the performance, durability, and sustainability of axle manufacturing, driving technological innovation across the globe. The ongoing exploration of lighter, stronger, and more efficient axles will continue to shape the future of mobility and industrial progress.
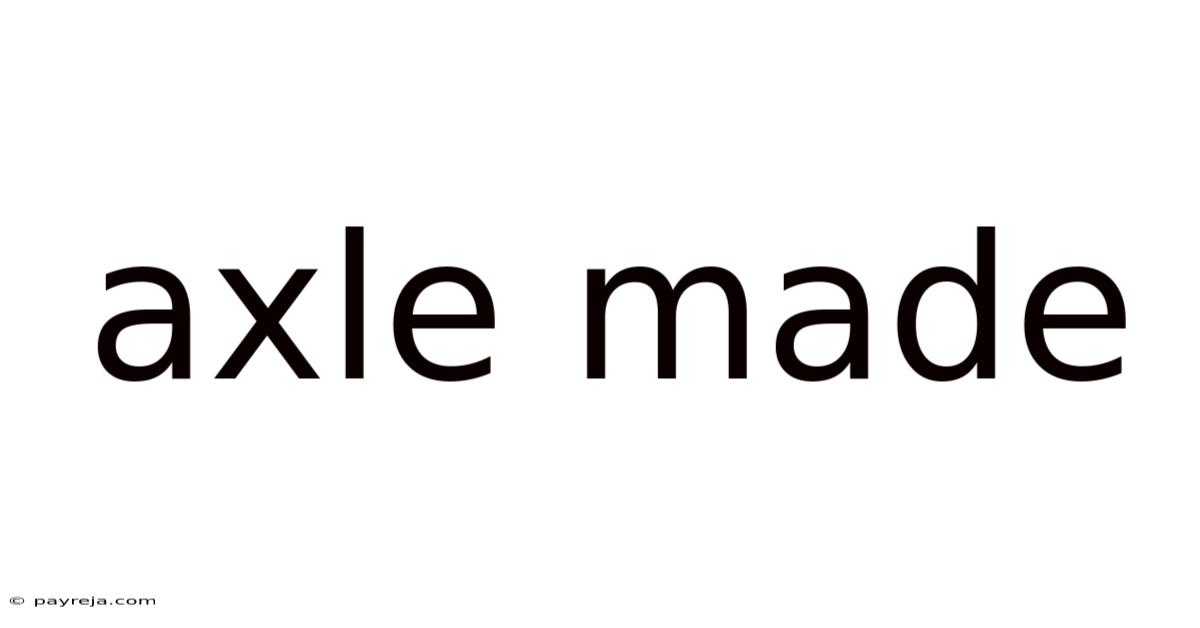
Thank you for visiting our website wich cover about Axle Made. We hope the information provided has been useful to you. Feel free to contact us if you have any questions or need further assistance. See you next time and dont miss to bookmark.
Also read the following articles
Article Title | Date |
---|---|
What Does Pipedrive Mean | Apr 26, 2025 |
Customer Relationship Management System Project Report | Apr 26, 2025 |
Crm 360 | Apr 26, 2025 |
Customer Relationship Management Report Sample | Apr 26, 2025 |
Salesforce To Salesforce Connector Limitations | Apr 26, 2025 |